ZIMMER GROUP’S NEW ZIMO FLEXIBLE ROBOT CELL SMOOTHS THE PATH TO AUTOMATION
The discussions surrounding automating the United States’ manufacturing sector have never been more sustained or indeed more relevant than today. There are few who would argue that the combination of labor and skills shortages, together with the drive to attain greater levels of productivity, means that automation is now becoming an essential part of manufacturing for a greater number of businesses, especially SMEs.
There are still however, certain perceived barriers inhibiting the adoption of automation for some businesses, amongst them are complexity, investment cost, training and skills. The new ZiMo flexible robot cell from Zimmer Group addresses these perceived barriers by offering a cost-effective and straightforward process automation solution for small, medium-sized and alternating batch sizes. Zimmer’s flexible robot cell enables both rapid deployment and intuitive operation, smoothing the path to the introduction of automation.
The proliferation of collaborative robots (cobots) in recent years, together with a general increase in the adoption of the smaller variety of industrial robots, has certainly sparked a greater interest in automation and encouraged many to explore the possibilities through the integration of robots for a wide range of tasks. The robot or cobot itself however is but one part of the overall solution. The robot still must be installed alongside the manufacturing process, interfaced to the line and equipped with the necessary tooling and technologies to enable it to perform the required tasks.
(Left to Right: ZiMo with small parts gripper – ZiMo with gripper change system – ZiMo for flexible applications)
Flexible, Mobile Process Automation
ZiMo’s compact design and mobile positioning concept enables the rapid deployment of the system where and when it is needed, overcoming the perception of complexity. This, combined with a comprehensive range of Gripper and EOAT options, means that the system can be easily configured for a variety of handling and process operations. The fact that ZiMo can be used without the need for any complex integration means that the handling system offers absolute freedom of use and the versatility to be quickly and easily reconfigured for new assembly, pick and place or even training requirements. A significant benefit for users of ZiMo is the fact that no prior programming knowledge is required when commissioning the system. ZiMo’s “robot neutral” concept means that this flexible robot cell can be used with a wide range of smaller industrial robots or cobots and be set up and commissioned intuitively via the Zimmer human machine interface (HMI). This saves valuable time and resources, allowing users to focus entirely on areas of production that offer real added value for their business.
A comprehensive range of accessories including gripper and vacuum systems, sensor technology and the MATCH robot modules, mean that should production needs or processes change, ZiMo can be reconfigured quickly, without any significant effort or expense, to meet the new requirements. In instances where the system is to be used in conjunction with one of the smaller industrial robot types, floor scanners can be integrated on each of the four corners of the system to provide the safe operating environment required when using this type of robot.
(Zimmer’s MATCH modules complement a comprehensive range of accessories for the ZiMo system)
Vincent Zimmer, Managing Director with ZIMMER Group US, comments on the advantages of the system: "ZiMo makes it possible for users, even those with no prior automation or programming experience, to take advantage of the benefits of a collaborative robot by supporting their employees in monotonous, time-consuming tasks throughout the day, and at night if required. The variable set-up options for the workbench and its compact size make ZiMo a reliable, flexible robot cell for almost any small robot application, including loading and unloading of machines, pick-and-place tasks, or assembly as well as laboratory automation. Users of the system will benefit from reduced cycle times, enhanced productivity and improvements in consistency and quality.”
The ZiMo concept of a mobile, flexible automation platform, capable of being used with small industrial robots or cobots from a wide variety of manufacturers, and which is simple and intuitive to set up and deploy, will no doubt alleviate the obstacles for those looking to take their first steps into automation, or indeed those seeking to further expand the use of this type of technology within their manufacturing operations.
Zimmer Group is a family-owned and operated company based in Rheinau – Freistett, Germany, with 17 branch offices and more than 1,300 employees worldwide. Their North American headquarters are located in Hickory, North Carolina.
The company is among the leading manufacturers in the automation industry with standardized solutions for mechanical and plant engineering that have become globally recognized as high-quality, durable products. Under the slogan “THE KNOW-HOW FACTORY”, Zimmer Group specializes in six technologies: Handling, Damping, Linear, Process, Machine Tooling and System Technology.
Their specialty is in manufacturing grippers and end-of-arm tooling components for robotics and the automation industry. They also manufacture clamping and braking elements, industrial shock absorbers, machine tooling components along with soft-close technology for the furniture industry.
Comments (0)
This post does not have any comments. Be the first to leave a comment below.
Featured Product
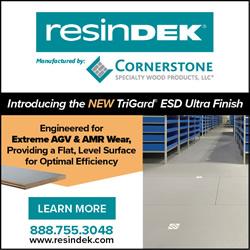