This document explains how companies can utilize advanced and emerging technologies to help deliver superior results. Prepare for the unexpected, understand your process, look at all the options, go back to the fundamentals, reengineer, gain stakeholder acceptance through a pilot program, and finally deliver. The savings are there for the taking.
Contributed by | Aberdeen Group
Traditionally, automated pallet handling equipment solutions, like Automated Guided Vehicle (AGV) solutions, have been limited in adoption to those companies where a substantial amount of the pallet movements are full pallet units. The higher investment costs of AGV solutions do not typically make them practical when the pallet must be broken to the case or each level for put-away or picking. However, unlike AGVs one technology segment, pallet robotics at both a full pallet and case level, is growing in relevance and beginning to challenge this traditional process-technology limitation.
Background: Synergy in Process and Technology
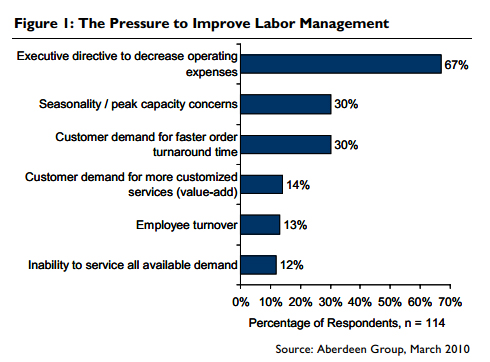
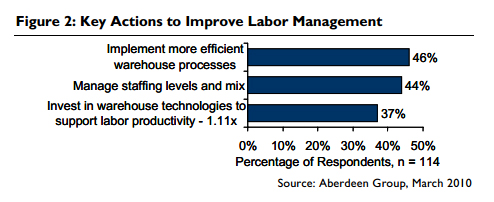
Performance Gaps – Automated Pallet Users vs. Others
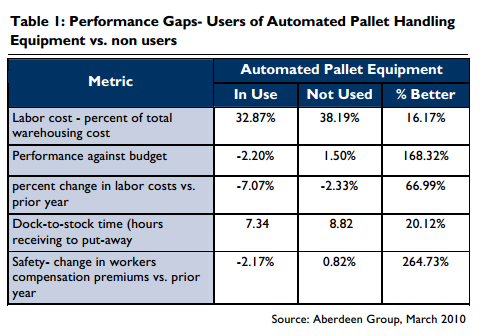
Case in Point: Midsized Auto Parts Manufacturer Deploys Robotics Solution and Improves Performance and Value
- Reduced labor costs. “Once the system is completely rolled out we will be able to reduce our material handling related labor force by about 10 full-time equivalents. Plus, the robots never get sick orneed days off,” said the VP of Manufacturing.
- Improved product visibility. “Each time the system transfers a load a log is created. We can analyze this data to optimize our material flow. Now we can better determine drop positions and floor layouts. This just isn’t practical without robots,” said the VP of Manufacturing.
Case in Point: Robots Decrease Dock-to-Stock Cycle Time
Cultural Background – Team Members are the Most Valuable Asset
Decreasing Travel Through Robotic Technology
Future Plans and Next Steps
Debunking Traditional Barriers
- Cost of ownership is lower. Compared to traditional AGVs the pallet robot is substantially less. In addition any maintenance worker that is trained on a walkie-rider is capable of performing setup and preventative maintenance. An AGV system is much more complicated (locked to physical constraints like lasers and wire guides) which are not easy to modify or alter with business and volume changes. Seegrid Robots on the other hand are easy to program, are easy to reprogram/repair, and are capable of multiple modes and routes depending on business needs and volume. The investment, training, and ongoing upkeep are substantially less with the Seegrid robots.
- Applicable unit volumes are much larger. With proper redesign of one's process users have demonstrated that robots can be complementary and synergistic with less-than-full pallet picking solutions. As companies match process with process/people in less-than-pallet operating areas, they are beginning to adapt to the more robust capabilities that robotics solutions provide.
- ROI thresholds are easier to obtain. The combination of lower investment and greater applicable volume (above) can generate acceptable cost/benefit analysis and ROI. Companies that understand this advantage are more likely to understand that they can meet or exceed the one to two year payback requirement that most enterprises demand.
Recommendations and Summary
- Understand and document current process and challenges. Document and understand the current method and streamline breakdown the process into its elements. Many companies are hampered by the challenges found in the sidebar to the right. For instance, over 56% of companies have not analyzed or measured current individual performance. Without having knowledge of what your costs and methods are, you cannot baseline for improvement. The companies that are getting maximum efficiencies from their new solution understand the limitations and barriers of the current system, understand their metrics, and work to understand company culture well before they attempt redesign. Making sure you know your current metrics and can understand the full flexibility and value of the new solution puts the control back in your hands to properly balance your people, processes and technology to find optimal performance. Unlike older AGV and even newer AGV technology, the case studies illustrate the ways companies are debunking the traditional barriers of AGV technology that simply isn't that flexible, compared to robots.
- Reengineer and redesign the process. Where you find barriers due to people, technology or process, be willing to break down and realign your work methods to take advantage of newer technology advancements. Get creative and look for synergy across people, process and technology. For example, from our March study (Labor Management: Instill Accuracy, Efficiency, and Productivity in the Warehouse and Retail Store,) we know that leading companies are 40% more likely than others to utilize the full capabilities of their warehouse management system. For example, one company, through simple table changes was able to use walkie-rider robots in their high volume case picking operations by simply instituting picking zones in their WMS system rather than using a full warehouse pick (this is similar to the Giant Eagle project on case picking that is now under study). The new solution allowed order selectors to build a store pallet without getting on and off their rider.
- Pilot extensively and obtain buy-in. Overall there is an increased focus and appetite for becoming more efficient as well as safety conscious throughout industry. About 30% to 40% of companies from the March study are looking to find technologies to complement or automate pallet handling. By testing and piloting the program first you can avoid resistance to change and insure the buy-in is in place from both the workforce and management.
The content & opinions in this article are the author’s and do not necessarily represent the views of RoboticsTomorrow
Comments (0)
This post does not have any comments. Be the first to leave a comment below.
Featured Product
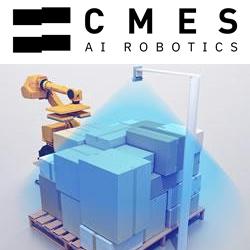