Having a wrong label on a can of food, or a wrong lid on a cup of margarine, could have serious consequences to the manufacturer and the retailer, as well as the consumer. An automatic identification solution using 1D and 2D barcodes is a reliable way to improve quality control in the food packaging process, ensure safety and to avoid human errors.
Contributed by | Microscan
Food manufacturers place high importance on ensuring product safety and quality for their customers. Not only is the industry highly regulated, but any errors can be very costly due to product recalls. Having a wrong label on a can of food, or a wrong lid on a cup of margarine, could have serious consequences to the manufacturer and the retailer, as well as the consumer. An automatic identification solution using 1D and 2D barcodes is a reliable way to improve quality control in the food packaging process, ensure safety and to avoid human errors.
Problem:
Prevent wrong labels on food packaging and ensure that all products within one sales batch are the same.
Project:
Automate quality control using 1D and 2D barcode technology.
Solution:
QX Hawk imager automatically matches lids to cups and immediately stops the production line if errors detected.
Result:
Quality control system ensures immediate reliable results and avoids human error. Full return on investment in less than three months.
CASE STUDY
Bunge Finland, founded in 2009, is a manufacturer of margarine that develops, produces and markets healthy and high quality vegetable-based margarines and vegetable oils. In the autumn of 2009 the company acquired Raisio’s margarine business, which has been a pioneer and expert in margarines in Finland for over 50 years.
In 2011, the company received a request from one of its large international customers to implement automated quality control checks to error-proof the packaging process in their factory in Raisio, Finland. The company placed a 2D Data Matrix code on the lids of the margarine products to match the correct lid to the correct cup. In addition, they needed to make sure that each sales batch of six margarine cups contained only the correct product.
In the past, quality control relied on visual and paperwork checks. The company wanted to rule out human errors, in case a cup from the previous batch would mistakenly enter the following batch, or that a package in the wrong language could slip into a delivery.
Bunge was already using the QX-830 industrial laser barcode readers from Microscan to read EAN-13 retail codes on the bottom of the cups. These readers were supplied by Informa, a Microscan partner and specialist in labeling and marking systems.
Now as Bunge needed to read the 2D Data Matrix code on the lids, they again opted for Microscan and Informa, to make sure that maximum synergy could be achieved. They selected the QX Hawk industrial 2D imagers from Microscan recommended by Informa. The QX Hawk is fully integrated with liquid lens technology which enables infinite focus flexibility.
The embedded processing, together with three high speed inputs/outputs directly from the reader, enable the QX Hawk to provide line level control functions. The QX Hawk decodes the Data Matrix code, compares it to a database and automatically stops the production line if an error is detected.
Bunge worked on a very tight schedule and were able to implement the solution together with Informa within three months from start to finish.
The solution has already proved its value to Bunge. Shortly after installation, they were able to stop a batch that contained the incorrect product from being packaged thanks to the quality checks with the QX Hawk imagers. They have thus achieved almost full return on investment immediately after implementation. Mika Tammi, Maintenance Manager at Bunge Finland comments: “We are very happy with this solution. Our customer is satisfied and we were able to finish the project on a very tight schedule. We have a great working relationship with Informa and Microscan is definitely the right choice for us.”
“This project has been a great opportunity for us to get more experience in Microscan’s 2D technology. Microscan’s application support assisted us in finetuning the system, and can be a great help to save time and to get the solution up and running even faster,” said Jari Hanén, Key Account Manager at Informa. In addition to fine-tuning, Bunge and Informa are optimizing the production line settings and planning improvements such as making the packaging line easier to clean and refining the lighting.
Bunge is planning to implement the 1D barcode readers on their other production lines, and will also look into expanding the use of 2D imagers. They are one of the first Bunge factories in Europe to use 2D barcode readers for quality control. “Expanding the system to also include machine vision could offer interesting possibilities, such as checking the best before date,” commented Hanén. “We find it important to make the most of technology and keep developing our service to meet customer requirements. This gives us a leading edge,” Tammi concludes.
Microscan is a technology leader focused on precision data acquisition and control solutions serving a wide range of automation and OEM markets.
The content & opinions in this article are the author’s and do not necessarily represent the views of RoboticsTomorrow
Comments (0)
This post does not have any comments. Be the first to leave a comment below.
Featured Product
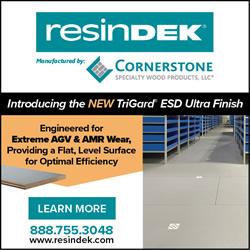