As the automation industry begins its reach into the cloud, manufacturing communities will not only improve productivity, they will begin to reclaim the prominence the industry once claimed in the economy.
Rush LaSelle | Adept Technology, Inc
Manufacturers and processors of anything from snack foods to automobiles are being driven to offer higher levels of variety in what they offer their customers. Invariably, supply chain power is shifting to buyers and consumers. This shift has been driven by numerous factors including the proliferation of information available to shoppers on all forms of digital devises effectively creating larger consideration sets. As the choices increase, sellers and ultimately suppliers are forced to increasingly adhere to fads and rapidly changing consumer sentiment to retain market share. If we were to define the optimal supply chain to meet this trend it would be one where any item, no matter its level of complexity, would be produced on demand. Further, even the most commoditized and low cost items such as confectionaries would be produced in a batch size of one to permit mass customization. This would enable a buyer to select a picture of the family dog from their iPad, upload it to a manufacturer’s website and a few days later a delivery van would arrive at the door with a box of chocolates each in the shape of Scruffy.
Markets are best served by catering to the individual tastes and preferences of the consumer. Therefore, we are compelled to determine how manufacturing can adapt to move past today’s linear processes to achieve a batch size of one. The innovation required to enable manufacturers to offer this, the ultimate level of production flexibility, will be drawn from fast-paced/cutting edge/advanced industries such as gaming and information technology.
Enter Cloud Manufacturing as technologies already exist in all facets of packaging, labeling, and decorating permitting rapid change of color, pattern, and form. The pacing item is process control and ultimately the information from the consumer. With the unprecedented speed of digital connections between people and the commercial world through social networks and the realization of Big Data, this valuable information can be made more readily available to manufacturers through the cloud. Cloud manufacturing represents the convergence of information, learned processes, and intelligent motion or activity.
Definition
Cloud Manufacturing is a model for enabling convenient, on-demand network access to a shared pool of configurable manufacturing resources (e.g., robotics, control systems, networks, applications, and services) permitting the comparison of digital process control with physical operation. The networking of sensory input, databases, and computing resources facilitates the management of sufficient data to recognize complex patterns and execute algorithms to evolve behaviors. Reconciliation of environmental conditions and information available in the cloud permits mechatronics to serve as the conduit between the digital and physical world.
Dynamic Process Control
To illustrate the concept, consider a robot tasked with dispensing icing on a cake. Today a robot is programmed to process certain patterns and graphics taught by its user. The robot would be outfitted with the ability to dispense various colors with different nozzles and the system would produce cakes with various images. In a highly controlled environment, a cell with set programmed paths will produce the images without incident. However, what happens if the environment or process changes. Consider the impact of the following;
- Viscosity of the icing
- Temperature within the facility
- Humidity
Viscosity of the icing is critical and most closely controlled. To keep the viscosity the same, the cake decorator is most likely locked into a single supplier to ensure consistency. In the event that the decorator produces his or her own icing, the level of process control to maintain the consistency is costly.
Temperatures in facilities affect a large number of parameters in the process. If the cake is cooled in ambient conditions it is subject to the changes in the plant’s temperature, which may impact the dimensions of the cake when it comes to the automated decorating station. If the icing sits in the delivery system for a period of time and the facility’s temperature varies day to day, the viscosity and properties of the icing are altered in kind.
Like temperature, humidity can impact numerous steps in the process. A higher level of moisture in the batter during one shift changes how the cake rises or its dimensions as it cools from the cakes produced the previous shift.
In some cases simple localized sensory input can adjust for environmental changes. If the cake height changes due to temperature, humidity, or upstream process changes, a variety of sensors might communicate the need for an offset to the robot for the dispense height to accommodate the change. This signifies a defined rule-based solution and is far from complex.
Viscosity can be measured though numerous sensing devises located in the delivery equipment or lines. With the appropriate delivery mechanisms, the manner in which the icing is pumped through the lines and ultimately though each nozzle can be profiled and managed to adjust for the changes in viscosity.
Therefore, it would appear through a rule-based system and the implementation of sensors that the cake-decorating system can accommodate environmental changes, correct? Not so fast. As humidity changes and temperature goes up or down the icing exhibits different properties of adhesion and set-up. So, while the robot is dispensing at the right height and the right volume, the desired flower form changes from a carnation to a dandelion. The interaction of the various environmental factors and effects now represent complex patterns.
When the inputs or variables become sufficiently large, this model exceeds what manageable rule-based solutions are capable of solving. In our cake-decorating example we are now going to add 3D vision which will record the decorated cake. The image will be analyzed with set parameters to determine if the critical features are within spec. The image will be correlated to environmental data to catalog plant temperature, humidity, icing, viscosity, cake height, and any other inputs we care to monitor. As the process compares predicted outcomes to actual outcomes, the system has the ability to dynamically adjust the process. Over time as patterns develop with the information, the process will evolve to where for all combinations of environmental conditions the system will learn how to modify the path of the robot to reliable draw a carnation.
Cloud Manufacturing enables machine learning given the networking of expected results or those stored in a database, input from what is observed in the environment, and comparison of the predicted outcome with the actual. In this model, the robotic system is the networking device that provides sensory input and ultimately uses the information processed in the cloud to intelligently process the part. Hence robots act as the connection between the digital and physical.
Batch Size of One
Let’s continue with our example of decorating cakes and return to the desire to personalize products for each individual consumer. The concept of cloud manufacturing allows access to a network where the consumer resides. In a basic model our baker has a website where a customer can upload a photo of their child playing lacrosse with the expectation that this photo will be reproduced on a birthday cake. This is a simple printing process for our baker, and there are web services that provide this service. But our baker wants to produce this image with depth to it as opposed to having it solely lay flat.
When the system was set-up to make a carnation the decorator had programmed the robot to dispense the icing at a specified rate, in the right place, at a precise angle, and for the appropriate amount of time so that it created a layer of the image. It would continue to make layers of the icing on the cake’s surface until it produced the desired form. It is unlikely that this was a one pass programming effort; most likely it took time and refinement, (and many cakes) to get a rendering that would finally meet the decorator’s artistic standards. The challenge with the baker’s business model is that the decorator won’t have the luxury of processing the lacrosse picture numerous times due to the material loss and decorating machine availability required for each set-up.
Once again, we find a scenario where the patterns and data set are so large that it moves beyond where rule-based programming is feasible. Over time and through iterations, a database will be built and the behavior of the decorating machine will evolve to where the interaction with the icing already deposited and that extruded from the nozzle will be understood and the robot can process accordingly.
Reduction in Programming
To realize greater flexibility, manufacturing has come to depend on robotic automation to deliver incrementally better levels of customization for production and packaging. One of the greatest barriers to deployment and the largest complaint from users of industrial robots is the programming. Many have asked why they must become proficient in dedicated languages to accomplish moderately straight forward tasks using robots or mechatronics as a whole. The cloud offers solutions to these challenges today and offers even greater promise for the future.
Manufacturers have used networks in the manner defined by cloud computing where programs are stored remotely and shared across networks. If a cell installed in California is to be replicated in Beijing, a back-up located on a server is transferred to the machine, a calibration routine is implemented, and the program is shared. This effectively enables an operator in China to leverage the development or work done by a programmer in California. As languages become increasingly open, algorithms and established routines will be available in the cloud so that programmers can pull blocks as opposed to always having to program from scratch.
Machines are just beginning to gain the ability to search for these blocks and with certain conditions implement them to affect their activities dynamically. To help illustrate, let’s look at a recycling plant using robots to pick glass from a paper line. Today the robot is programmed to identify and remove hundreds of unique types of glass and sort them for optimal recycling. The robot determines all the known products using an onboard processor, which would have been programmed by identifying each piece of glass with a local camera. Not only is training the system to recognize hundreds of unique glass types cumbersome and prone to error, it leaves the system unable to adapt to unknown parameters and foreign materials.
If, however, the recycling system were to harness computational capabilities and information from the cloud, it might search terabytes of information to identify an object previously unseen at this system’s location. This would function very similar to how web crawlers search the web today for any other type of information when keyed into a computer or smart device. In this scenario once the item is matched to an image in the cloud, a resulting action would be performed as the image is crowded or grouped into a product class or family which would instruct the robot how to manipulate and place the item.
This now reduces the programming requirements for a system while simultaneously expanding its flexibility almost infinitely. The result is a system which costs significantly less to deploy and provides much greater economic value to the manufacturers or recycler in this example.
Ecosystem Drivers
The concept of cloud manufacturing is not solely driven by the demand for ever-increasing levels of flexibility and efficiency in deploying automated systems. As noted earlier, there is a supply side effect where technology and networks are now enabling higher levels of speed and low-cost processing previously unavailable. Factory automation and robotics must begin to view themselves not as industrial islands, but as devices within an information ecosystem. Historically, manufacturing equipment’s only connection to its environment included a power source, input of raw materials and output of processed goods. As such it was not adaptable to any form of change. During the industrial revolution while goods were finally being made cost-effective to where consumers could afford items previously considered a luxury, buyers were offered any color car they wanted from Ford as long as it was black. The industry focused on employing technology to enable mechanical processes to produce faster and more consistent products but flexibility was not an essential requirement.
As manufacturing begins participating in the information revolution, machinery and automation will generate and consume greater amounts of data to where they can offer higher levels of quality through dynamic process control, provide the flexibility to satisfy and insatiable consumer appetite for mass customization, and ultimately decrease costs of implementation through learned heuristics. Unlike the productivity gains of the Henry Ford era, today’s gains will be driven though better utilizing processing information technologies.
It can be expected that over the coming years that manufacturing will more fully capitalize on the information ecosystem surrounding it. This ecosystem spans the networking and data storage industries to the human machine interfaces currently being deployed by consumer electronics manufacturers and gaming technologies. As the automation industry begins its reach into the cloud, manufacturing communities will not only improve productivity, they will begin to reclaim the prominence the industry once claimed in the economy.
The content & opinions in this article are the author’s and do not necessarily represent the views of RoboticsTomorrow
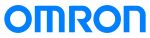
Omron Automation
Omron is an industrial automation partner that creates, sells and services fully integrated automation solutions that include robotics, sensing, motion, logic, safety, and more for manufacturers in the automotive, semiconductor, food and beverage packaging and other industries. Established in 1933, Omron helps businesses solve problems with creativity worldwide, with more than 37,000 employees serving over 110 countries. Adept Technologies is now a valued part of the Omron family.
Other Articles
Advancing Machine Design with the Power of Collaboration and AI
Preparing Your Facility for Mobile Robots: Key Considerations for Seamless Integration
Transforming Manufacturing Processes with AMRs: Boosting Efficiency and Adaptability
More about Omron Automation
Comments (0)
This post does not have any comments. Be the first to leave a comment below.
Featured Product
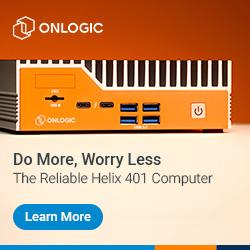