Even though robots are known as repeatable and not precise, many tools can be used to obtain robust and precise results such as force feedback components, vision systems, laser sensors, probing, active compliance, adaptive machining, closed-loop machining, Leica calibration, etc.
Eric Beauregard | AV&R Vision & Robotics
Please tell us a bit about AV&R Vision and Robotics --- what do you specialize in and why is it important?
AV&R Vision & Robotics offers precise industrial automation solutions to optimize manufacturing processes and quality control for gas turbine critical parts. We are known as the world leader in Robotic Finishing (deburring, profiling, polishing, blending and more) and in Automated Visual Inspection (2D and 3D) of gas turbine parts such as blades, variables vanes and blisks / IBRs.
When you think about an aircraft engine, you inevitably think it has been designed and manufactured with great care and precision. You are right about one thing; its design was created very precisely. The list of considerations taken into account when designing commercial aero engines is endless; engine efficiency, fuel burn, environmental emissions, engine noise, weight, temperature, material, durability, operating and maintenance costs… All these factors are carefully thought through before creating the design of every single part included in an engine. But what good is there to have groups of engineers take years to design extremely precise jet engine parts, considering more factors than we can think of, when these perfectly designed parts are not manufactured to these tolerances? Why spend so much time and energy designing critical rotating parts if the precision required to manufacture them is almost physically not achievable?
There is no doubt that the same attention put in the design should be put in manufacturing the critical parts but, sadly, reality reveals something different; today, humans manufacture critical rotating parts of jet engines so they evidently cannot easily and repeatedly reach the blueprints’ precision. Until recently, this is where the discussion ended. Luckily, the OEMs can now benefit from precise automation.
AV&R’s Factory, located in the Old-Port of Montreal
What are the main challenges in aerospace automation?
In aerospace, every process has been approved by the entire company (production department, quality department, etc.) and even sometimes by the final client. So, if you wish to change a process - let’s say automate it - you have to go through these approvals again. This requires a lot of time and investment that plant managers are not always willing to take.
Also, since the majority of applications requires a high level of precision, automation was not feasible before. Since there are variations in the production (at a high level of precision, every part slightly differs from another), the finishing process needs to be able to adapt itself to every part. This adaptive capability was not available in robotic systems in the past, so the automation of the finishing processes of aerospace parts was impossible.
This lack in the past has led to disbelief in automation in the aerospace industry: because of bad experiences with automation, many managers do not believe it in anymore. These bad experiences were often the result of trying to introduce a robotic system too early and it did not answer their precision needs (as it did not have the adaptability that now exists). Many aerospace managers are therefore reluctant to introduce automation in their processes, even more considering the efforts it requires them to get the process reapproved.
What are the main ways to reach the required precision with robots?
Even though robots are known as repeatable and not precise, many tools can be used to obtain robust and precise results such as force feedback components, vision systems, laser sensors, probing, active compliance, adaptive machining, closed-loop machining, Leica calibration, etc.
With a proper mix of these different tools, AV&R has developed Robotic Finishing Systems that can reach a level of accuracy as precise as ± 37.5 microns / ± 1.5 thousandths of an inch, a precision level unreached in industrial automation.
What are the benefits for a customer to automate his production (ex.: Automated Blade Leading and Trailing Edges Profiling System)?
From a business perspective, automation is a great way to save money and to achieve repeatability and consistency in production.
Per example, introducing AV&R’s Automated Blade Leading and Trailing Edges Profiling System to a manufacturer’s plant reduces workers’ injuries and plant’s abrasive material consumption up to 75%. It improves quality and consistency of the airfoils by eliminating human subjectivity, therefore creates better performing engines (parts more faithful to the design) which translates to substantial savings in fuel consumption for the airlines.
AV&R’s Automated Blade Profiling System
An example benefit realized by this system in the Maintenance Repair and Overhaul (MRO) market is the prolonged life of a blade. The system is able to calculate and remove the minimum amount of material to meet the required profile, thereby reducing any overwork or operation that would shorten the blade life.
Indeed, the manufactured blades coming into our finishing systems are not identical; they have production variations which may seem minimal, but when you work at the precision of the third of the thickness of a sheet of paper, these differences are considerable. Therefore the automated system cannot use a fixed machining parameter. This is where AV&R’s expertise comes in; our profiling system uses adaptive machining. Adaptive means that the machining parameters will be automatically calculated by the system according to the specific geometry of each part. This allows for parts to come into the system with variations and leave with consistent results.
In some cases, we could also need to go into a closed-loop mode, meaning that after the adaptive profiling of the part is done, it is brought to the inspection device and verified, so, with this feedback, the profile can be automatically adjusted if required. This closed-loop capability can be useful for blades that are refurbished (MRO) since every blade coming in the system will be completely different, not just slightly different.
Moreover, outside some pre-set tolerances, the automated system can send an alarm signal so the customer can investigate the upstream issues and save precious time and money.
How can automation affect cost-per-part?
Cost-per-part is affected by many factors. One of the most obvious ones is the reduction of scrapped parts; fewer parts are badly finished and thrown away. The cycle time is also reduced, making the same batch of parts being done faster, allowing the customer to raise its production volume with the same staff costs.
When you evaluate the cost-per-part, you also have to consider the costs of the staff and abrasives that you use. AV&R’s systems reduce the abrasive consumption up to 75%, which leads directly to savings in the calculation of the cost-per-part. Moreover, ergonomics and safety are enhanced when robotic systems are making the repetitive and possibly harming tasks. Less employees being harmed means savings for the customer, savings which are taken into account when trying to figure the cost-per-part.
The entire process can be reviewed and downsized since AV&R’s solutions are consistent, repeatable and reliable.
Is part quality and consistency improved?
Absolutely! AV&R’s Automated Blade Profiling System reduces variation in production compared to when a human does the profiling. The system even adapts itself to the cyclic variations in the production. A follow-up of these batch variations is made, to allow the operator to react to it before it gets critical; let’s say the forge wears, leading to the blade’s chord length to slowly decrease. The system will react to this variation and do its job, but it also will flag the production tendency. This system monitors the quality of the production coming into the system, not just the quality of the blades getting out if it.
The biggest ROI for customers is the consistency of the result that this kind of system insures. The whole finishing process can be redefined with this technology and, as a result, customers experience an increase in throughput and a decrease in the cost of poor quality. Customers usually get a return on investment (ROI) of 1 year.
Are there other applications for the systems that you have developed?
AV&R’s profiling system is pretty niche: it profiles leading and trailing edges of blades and fan blades for the aerospace industry. But the biggest development in this system is the intelligence added to it, which includes adaptive manufacturing and closed-loop capabilities. Other applications such as deburring, polishing and blending have been developed by AV&R using these capabilities, allowing robots to become precise.
AV&R works mostly on gas turbine parts used in aerospace, but also works on the same parts used in energy, which basically are bigger. The precision level to reach being very high, we are specialized on these parts, but our intelligent robotics solutions can be adapted to any other part which needs to be finished with a high level of precision and that has variations in its production (medical devices, dental implants, diamond rings…).
AV&R also offers Automated Visual Inspection Systems which detect surface defects such as scratches, dents, pits, etc. These quality control systems can easily be adapted to consumer goods such as faucets and watches since no one would by an expensive watch that has a scratch on it.
What are some of the new developments that will shape the future of the robotics industry?
The adaptability of the robots will definitely change the future of the robotics industry. With high precision adaptive machining, it is now possible to get around robotic problems that were hard to counter before, such as the joints wear or even the temperature where the robot is used: if the robot is in a cold or hot environment, its joints will either shrink or stretch, leading to the robot’s actual position being different from the one intended. In high precision manufacturing, this problem was a game stopper, but no longer is since we have the capacity to follow the robots in real time, allowing the entire industry to raise their precision, which will undoubtedly open new processes and markets to automation.
We can now say that, even though robots are known as repeatable but not precise, robotic systems can be repeatable and precise!
About AV&R Vision & Robotics
AV&R Vision & Robotics specializes in complex automation projects requiring a high level of precision. May it be for quality control (such as detection of surface defects, assembly validation of complex components, high-precision measurements) or part finishing (such as profiling, deburring, polishing, blending), AV&R's automated systems are designed to meet its customers' obligations and requirements as well as industry standards.
About Eric Beauregard, CEO of AV&R Vision & Robotics
Graduated from the University of Sherbrooke with a degree in Economics in 1991, Eric Beauregard began his career in business development with two American companies specialized in information technology. Hired at Netergy in 1999, he has been Sales Director for Europe and General Manager.
Thereafter, Mr. Beauregard was named Vice-President and General Manager at Silicomp Canada, (now Orange Canada) where his role was to structure the company and make it grow. At his departure in 2005, the company had about thirty employees.
Finally, Mr. Beauregard joined AV&R as CEO in 2006. At first, his role was to structure the former Averna group as an independent company and, then, with his team, to find a market niche for the company. Mr. Beauregard now concentrates on leading AV&R to be recognized as a world leader in Robotic Finishing and Automated Visual Inspection for gas turbine parts.
Member of the Aerospace Advisory Board of the Department of Foreign Affairs and International Trade Canada (DFAIT), Administrator on the Board of the CRIAQ, member of the Board of Directors of the Quebec Aerospace Association (AQA), advisor on the AÉROÉTS’ Industrial Advisory Board, Vice-President of the Regroupement des équipementiers en automatisation industrielle (REAI) and speaker for the Board of Trade of Metropolitan Montreal's "Back to school" operation, Mr. Beauregard is highly involved in giving back to society.
The content & opinions in this article are the author’s and do not necessarily represent the views of RoboticsTomorrow
Comments (0)
This post does not have any comments. Be the first to leave a comment below.
Featured Product
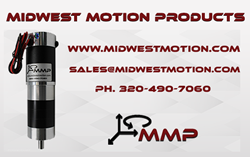