Hearing device manufacturer Oticon needed a more flexible robot to handle the tiny hearing device components in its production. The company found the ideal solution in the six-axis robot from Danish company Universal Robots.
Employing robots in the production process was not a new concept to Oticon. This manufacturer of hearing aids had been using robot technology for the past 10 years. But, as the minute components became increasingly smaller in order to make the hearing aids more comfortable, the existing two- and three-axis robots used in manufacturing were no longer suitable.
Arne Oddershede, group leader of the maintenance unit at Oticon’s test and production center in Thisted, Denmark, explains that the production tasks could not be performed by manual labor either.
“The parts for modern hearing aids are getting smaller and are often only a millimeter in size. We looked for a solution that can suction small parts out of a mold. This was impossible manually. We needed a more flexible solution that would also be economically viable for smaller production runs,” says Oddershede.
Flexible robot arm with six rotating axes
Armiga, the systems integration specialist, also based in Thisted, had the right solution for all these requirements. It was in the form of the UR 5, a six-axis articulated robot arm from Danish manufacturer Universal Robots weighing only 40 lbs and with a payload of 11lbs.
“We realized that two- or three-axis robots were not suitable for the job. Lateral and vertical movements were nowhere near sufficient. If for instance a small part is stuck in a mold, it must be possible to tip it out,” says Lars Gasberg, Sales Manager at Armiga.
Intuitive user guidance and the precision of the UR robots, were the features that convinced Oticon. Also, rapid advances in medical engineering have resulted in constantly changing production processes and a broader range of hearing aid models that require a flexible robot handling smaller batch sizes.
Suction tool for up to four components
It took just one day to install the robot for its new task in Oticon’s molding shop, where the company handles very small components such as wax filters that are barely a millimeter in size. These are fitted to the inside of the hearing device to protect the electronics from wax buildup in the ear.
Mounted firmly to the injection molding machine, the robot can position itself over the mold and suction the plastic elements using a specially designed vacuum system. This is possible due to a suction tool that can accommodate up to four tiny components simultaneously. The UR 5 is programmed to only engage the suction mechanism when the mold is open. Once it has taken the parts, the robot draws away, and the injection molding machine prepares for a new operation. All the components from the same mold are subsequently collected in separate tubes to ensure that they can be traced correctly. The vacuum system also ensures that the sensitive elements are not damaged.
More complex molded components are handled with pneumatic gripping tools. Because of its six axes, the UR 5 is very manoeuvrable and can rotate or tilt the parts in order to lift them quickly out of the mold. The robot works in four- to seven-second cycles depending on the size of the production run and the component.
Hands-on Robots
Arne Oddershede emphasizes the accessibility and logical design of the UR robots.
“Since we produce different batch sizes and components when developing new products, it must be possible to easily reprogram the robot. With a traditional robot, this involves a computer and requires specially-trained staff, typically a programmer. But with the UR 5, any member of the technical staff can literally grab the robot and show it the motion sequence using waypoints,” he says.
The robot comes with a fitted safety mode that allows staff to work alongside the robot without any additional safety shielding. There is a sensor installed in each joint that notices when the robotic arm requires more force for a given movement than previously calculated, for example when an arm or a foot is in the way. The robot will stop working immediately if a counter pressure of 150 Newton is detected. This safety mode has been certified by the Danish Technological Institute in accordance with the European ISO Standard 10218.
Cost-effective investment
The price of around € 22,000 was another persuasive factor in purchasing the robot from Universal Robots.
“The investment paid for itself within a few short months. Also, the operating costs are reasonable, since the robot works in a particularly energy-efficient manner. The UR 5 has met all our requirements,” explains Oddershede.
Oticon has now deployed a second robot for the same field of application at its production site in Poland.
About Oticon
Oticon has 3,500 employees globally and distributes products to more than 130 countries. The company is one of the three largest hearing aid manufacturers in the world.
About Universal Robots
Universal Robots has reinvented industrial robotics with the lightweight and flexible UR5 and UR10 robot arms. The Danish-designed robots automate production in all industries – even in SMEs that regard automation as prohibitively expensive, cumbersome, and difficult to integrate. The robot arms require no safety shielding, can work alongside personnel, and are easily moved around the production site to complete even the most detailed tasks. Programming is intuitive, eliminating the need for skilled programmers; simply grab the robot arm to show it the desired movement, or use the simple touchscreen.
The robots are sold in more than 40 countries. European portfolio customers include companies such as Lear, Bosch, BMW, Scandinavian Tobacco Group, LG, Samsung, LUK, and GN Resound. In Asia, UR robots are used extensively by the Bajaj company in the yearly production of 4 million vehicles, motorcycles and auto rickshaws.
The Danish company employs approximately 50 people. All development and production is carried out in Odense in Denmark.
The content & opinions in this article are the author’s and do not necessarily represent the views of RoboticsTomorrow
Comments (0)
This post does not have any comments. Be the first to leave a comment below.
Featured Product
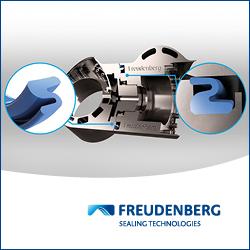