Dynamic interaction with a robot programming software has never been easier but it did come at a cost. Our entire simulation framework had to be designed from ground up to allow for instantaneous interaction.
Robot Programming for the Future
Chahe Bakmazjian | Robotmaster
Can you tell us a bit about Robotmaster?
Robotmaster is a programming software for industrial robots. Our first installation was in 2002, at that time Robotmaster was a converter of Mastercam CAD/CAM paths to robot programs. Very early on we realized that the demand for simple and effective robot programming was going to be a large part of the new type of manufacturing propelled by globalization, flexible manufacturing and off-shore competition. Recently we have also been hearing about re-shoring, all these trends are pushing companies into looking at novel ways to increase manufacturing flexibility and efficiency all the while reducing costs and lead time. Having identified that robots were going to play a large part in this trend and coming to the realization that a new breed of software was going to be required to help companies our vision was born. In addition, I can never fully talk about Robotmaster and not mention our dedicated and skilled network. Our distributors and resellers cover most of the worldwide manufacturing areas and their skill and focus enables us to offer a global channel to our equipment partners. Our network really sets us apart.
You call your software CAD/CAM for robots, how does it differ from off-line programming software?
Early on we self-classified our software “off-line programing for robots”. However talking with robot manufacturers, integrators and prospective customers we realized that the term off-line did not exactly fit the function of our software. A classic off-line programming software was developed to emulate the teaching process and what was once performed live on the robot could have now been carried out in a virtual environment. Over time, many off-line software started implementing more and more CAD functionality as the requirements for digital manufacturing dictated. However, in general, off-line programming puts more of an emphasis on total end-user control and less on automation. As robots started entering new and emerging manufacturing markets that required quick programming times by technicians and engineers that were green to robotics classic off-line programming was no longer an efficient tool. These technicians and engineers were more used to mid-range CAD/CAM software and expected a robot programming software with the same look, feel and functionality. We coined the phrase “CAD/CAM for Robots” in around 2005 and we are happy to see that the term is picking up in popularity. What differs Robotmaster from classic off-line programming is that robot paths are calculated automatically and no point-by-point intervention is required. Robot errors and limitations are identified and fixed automatically. Tasks that would require meticulous and skilled intervention can now be successfully programmed in minutes by a newbie using Robotmaster. Our best customers are the ones who have struggled before adopting Robotmaster, they are the ones who truly appreciate the power of the software.
We understand that Robotmaster V6 has been released; can you tell us what is new with this release?
Many enhancements and new features have been delivered with Robotmaster V6 but the one that stands out is our newly designed ROBOTMASTER INTERACTIVE SIMULATIONS ENVIRONMENT, we are using the acronym RISE to refer to it in short. RISE provides a unique integration of user control, speed and flexibility to Robotmaster’s renowned automation and optimization tools. This new intuitive interface elevates Robotmaster to an unprecedented standard of user experience.
You claim “Elevating robot programing to unprecedented heights” for Robotmaster V6. This is a very big claim, can you explain?
I was expecting this question as this is a pretty big claim! The new RISE interface will allow end-users to have the total point-by-point control that was possible with classic off-line software in addition to the automatic optimization and efficient programing tools available through CAD/CAM technology. It took a long time, behind closed doors, to design and orchestrate the integration of manual intervention tools with the automation. End-users can now benefit from manual intervention in a dynamic and interactive environment.
Let’s talk technology, can you explain the underlying advancement in technology and innovation that was required for Robotmaster V6?
Dynamic interaction with a robot programming software has never been easier but it did come at a cost. Our entire simulation framework had to be designed from ground up to allow for instantaneous interaction. An entire platform was designed based on how an end-user would want to interact with a robot to intuitively set and optimize a task. Meticulous analysis, testing and validation cycles were used to develop features for moving the robot, part or path as well as quickly knowing if there are any errors. Visual feedback and instant viewing of reach issues and colisions was designed. The real technological leap was designing a product that was easy and intuitive for a novice user as well as offering all the power that an expert programmer expects. In addition, to be able to provide instant visual feedback expected by a dynamic software intricate analysis was required to optimize the efficiency of our kinematic calculations as well as developing a state-of-the-art collision checking library that is as fast if not faster than the fastest available commercial libraries.
What are some of the most common applications for Robotmaster V6?
Robotmaster is ideally suited to program robots for such tasks as trimming, 3D machining, de-burring, polishing, welding, dispensing, grinding and painting, and supports most industrial robot models. For V6, many new features have been designed or enhanced for more adequate support for welding and cutting (laser, water-jet and plasma).
Where do you see robotic programming advancements going in the future?
We see a continued trend towards high-mix low-batch type manufacturing, were the emphasis is on mass customization versus mass automation. In addition, with companies looking at flexible automation versus dedicated expensive machines we see the demands on robot programming for the future are follows:
-
Easier to use, the software should be almost intuitive to use with little or no training;
-
In some instances, shop floor programing would be required, where the end-users are process experts and not robot or programming experts;
-
Programming automation is a trend we are seeing more and more. The end-user would use an interface more resembling an HMI versus a CAD/CAM software and once the choices and simple parameters are set, the programing automation is carried out;
-
Processes are being combined and one manufacturing cell is being required to do more. This trend is putting more of a demand on the programing software to manage more complex processes with more parameters to control and orchestrate.
For the manufacturer considering adopting robotics in his process, please walk us through a typical programming session.
About Jabez Technologies Inc. / Robotmaster
Jabez Technologies provides robot programming technologies that enable versatile and profitable robotic solutions for industrial manufacturing applications.
We focus on the development of easy robot programming tools that efficiently generate CAD/CAM-based robot trajectories to increase robot capacity and flexibility in the Aerospace, Transport, High Technology, Military, Medical and Industrial Manufacturing markets. We partner with progressive robot manufacturers, integrators and CAD/CAM software vendors to provide integrated solutions that meet evolving industry requirements and challenges.
The content & opinions in this article are the author’s and do not necessarily represent the views of RoboticsTomorrow
Comments (0)
This post does not have any comments. Be the first to leave a comment below.
Featured Product
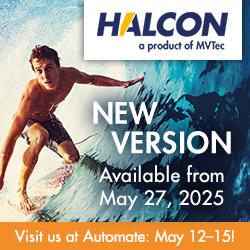