The following document poses some of the questions that a robotic user should consider prior to selecting a robot and a robot programmer/installer.
Jeff Kamin | QComp Technologies, Inc.
Robots are the buzz for anyone in manufacturing, assembling, packaging or distributing products. Are you looking for ways to automate, reduce variable labor costs and be more competitive? Robots are fast, powerful, and have a great range of motion which is precisely why they are such versatile tools in automation. However, many end users considering the potential value of a robotic system are relying on the integrator or OEM to provide a solution without really understanding the potential benefits and liabilities that come with a robotic system. The following document poses some of the questions that a robotic user should consider prior to selecting a robot and a robot programmer/installer.
Safety
Robots are fast, accurate, powerful and also incredibly quiet which means robots have what it takes to get the job done, but also have great potential to cause serious harm and damage. Safely harnessing the benefits of robots without endangering human life is the goal of robot manufacturers, qualified and reputable integrators, and should be the goal of every end-user as well.
- Have I read and do I understand the applicable safety standards that apply to robots and their integration? ie; Crush zones, guarding setbacks, access areas?
- Am I committed to adhering to the safety standards and requiring all parties associated with the project to comply as well?
- Am I committed to acquiring and providing the training needed for the safe use of the cell by operations and maintenance personnel?
Equipment
On the surface robots seem to be very similar in capabilities between the various manufacturer. Digging deeper reveals vast differences in hardware reliability, longevity, implementation of safety features, operator interface, and programming methodology. Regardless of size and complexity, your first robot system is often under great scrutiny and sets the direction for all future implementations. Pre-purchase diligence will help you establish a clear automation path now and reward you in the future as well.
- Am I confident that the robot equipment I am purchasing is the best fit for the current project and is it on the path I’ve defined for future automation projects?
Once implemented, robots are often vital to meeting your production demands. While they are extremely reliable, at some point support will be needed. Is there 24/7 support from the manufacturer or integrator? How quickly could the needed support personnel be on your site? Spare part availability? What about remote diagnostics? Has the cell been designed to allow for at least limited production with the robot out of service?
- Does the robot vendor/integrator have the resources and commitment to service that I need for this important part of my company’s operation?
End of arm tooling and cable management is crucial to the success of the project. Is it designed to survive the long term stresses of the anticipated loads/accelerations? Is it able to withstand the high forces of a collision with misplaced products or improper setup? Are consumable parts (vacuum cups/grip pads/nozzles) easy to replace without requiring recalibration? Keep in mind that cable (and hose) management becomes more difficult as the range of motion increases, and becomes more critical as the cycle rates increase.
- Does my (or my integrator’s) tooling design and cable management plans anticipate the rigors and lifespan of this project?
Programming, Operator Interface, Operations
The best robot for the application with well designed and robust tooling, in a safely designed and operator friendly cell can still cripple your operation if it has not been programmed with the same attention to detail. Programming determines whether your investment in robotic automation will be a trusted dependable partner, or the madman in a cage that the operators are scared to work with and maintenance hopes to avoid.
The operator interface must be clear and easy to understand so that operators can quickly gain confidence in using the system after appropriate training. The operator controls should minimize the steps required to set up the desired operation and validate the operators input to reduce the risk of errors. To further limit the possibility of improper setup and collisions, wherever possible, the system should be “self-aware” of the work environment through the use of sensors and encoding on tools, jigs or fixtures. Repetitive or reactive operations are often cumbersome and slow if done through operator displays – judicious use of real buttons/controls on a well designed panel is usually a better solution. Alarming and operator alerts should be specific, understandable, and retained in a log for later review.
Error and fault recovery must be bulletproof. Well written programs should be able to handle and guide the operator through the recovery process from any foreseeable error conditions without risk of damage to equipment or products. Well written programs should also determine where manual (i.e. qualified personnel) intervention is required and prohibit any other operations until in a safe position.
- Will my (or my integrator’s) programming abilities, experience, and dedication to this project ensure the finished system will meet the needs of our operators and provide them with the tools they need to make this project successful?
A well designed robot system should be pretty much maintenance free. Good programming, detailed alarming, and diagnostic logging can give your engineering and maintenance personnel a real edge in quickly identifying, and resolving problems with the system. Quality safety components properly applied along with the annunciation of each safety device’s status will minimize the temptation to “override” to get things working. Well documented programming with careful references to the real labeled input and output components further reduces the time needed to restore a troubled system to operation. Calibration and detailed instructions should be provided to allow replacement components or tooling to be quickly deployed with repeatable results.
- Will my (or my integrator’s) programming abilities, experience, and dedication to this project ensure the finished system will meet the needs of our engineering and maintenance teams and provide them with the tools they need to keep this equipment functioning as designed?
Robot systems can be as simple as a stand-alone pick/place unit or as complicated as a fully integrated system that chooses tooling, paths, routines, and calculates all target positions from data supplied by a supervisory system. Would your production tracking system benefit from information supplied by the robot system? Can you eliminate the potential of human error by passing system data directly to the robot system? The higher the level of integration, the more important it becomes to select your robot supplier/integrator carefully.
- Will my (or my integrator’s) programming abilities, experience, and dedication to this project explore the potential for real integration and production tracking so my investment can be fully utilized and production improvements documented?
Reality Check
Thankfully, the innovative application and use of robotics still depends on people - people like you – people with a vision and determination to see their plans through. Robots are great tools, but they clearly are not the solution for every application. While careful design and excellent programming can provide years of dependable production; robots do not innovate, offer suggestions, buy your products, rejoice with you at the birth of a child, or offer support when you need help. People are your biggest asset; use robots to help your people make the best products possible. If your people see the robot only as a way to cut the head count, you will struggle. If they see it as a tool to help them or relieve them of demanding physical work you are on your way to success.
- What is my motivation, and how can I best utilize people and automation to succeed in this demanding competitive environment?
About QComp Technologies, Inc.
Founded in 1990, QComp Technologies, Inc. is a robotics integrator, providing automation solutions for a variety of industries. The company designs and builds automated robotic manufacturing cells and materials handling systems, as well as engineers and manufactures drive systems for paper, metal and converting industries. With headquarters in Greenville Wisconsin, QComp has sales and service offices in Wausau and Milwaukee, WI. More information can be found on the company’s website at www.qcomptech.com.
The content & opinions in this article are the author’s and do not necessarily represent the views of RoboticsTomorrow
Comments (0)
This post does not have any comments. Be the first to leave a comment below.
Featured Product
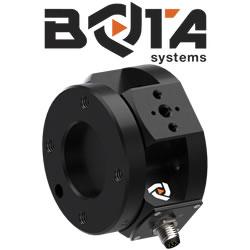