In order for a cable to withstand repeated torsional movement, its necessary for the cable to have a special design. Its important that the conductors, shield construction and jacket materials of the cable compensate for major changes in bending load and diameter.
Contributed by
Design Advice
As industrial robotic applications become more and more demanding, we’re finding an increased need for flexible cables that can handle extremely complex movements and still deliver a long service life. When specifying cables for these types of applications, there are some important features to look for.
In order for a cable to withstand repeated torsional movement, it’s necessary for the cable to have a special design. It’s important that the conductors, shield construction and jacket materials of the cable compensate for major changes in bending load and diameter. To accomplish this, igus® uses "soft" structural elements—rayon fibers, PTFE elements or filling elements—that absorb torsional forces. When data transmission is essential, we use specially engineered insulation systems to ensure performance remains within a specified range over the cable’s service life.
In contrast to conventional braided copper shields, a torsion-resistant, tin-plated copper shield sheath is used in igus®’ Chainflex® CF Robot cables. The forces affected on the cable by any torsional movement are largely absorbed by sliding and buffer elements between the sheath, shield and insulation. Using a highly abrasion-resistant, halogen-free and flame-resistant PUR or TPE sheathing mixture prevents early failure of the shield and also protects the cable components from potential damage.
It’s also important to keep in mind that robot cables, unlike traditional continuous-flex types, can withstand various "mechanical stresses", including bending, torsion, centrifugal forces or a combination of all three. However, it’s nearly impossible to determine in advance what these cables can handle, even when taking into account their design or performance during use. So, to better evaluate these cables, igus® developed a "torsion test standard”. According to this standard, all CF Robot cables have been tested in the igus® test laboratory through more than three million torsional movements to +/- 270 degrees without failure.
Choosing cables for a robotic application can be challenging so paying close attention to a cable’s construction and working with a company that performs in-house testing can be key.
The Full Scoop
igus® offers a complete line of motion cables for robotic applications and three-dimensional motions. The Chainflex® CF ROBOT cables are based on specific design principles. The tested service life is paramount for the Chainflex® cable series for linear motions just as with the torsional cables.
The motion sequences in industrial production are becoming increasingly complex, and special cables are increasingly required for torsional movements. For this purpose, igus® has continuously expanded its Chainflex® CF ROBOT family: From hybrid and control cables to motor cables, bus, data and fiber optic cables, igus® has a complete cable range for robots and three-dimensional movements from stock. Supplied from one meter in length and no minimum order size or cutting costs.
Damping elements and optimized shields compensate torsional movements
Cores, stranded packages, shields and jacket materials are constantly exposed to highly fluctuating loads with torsions. The stable, highly glidable igus® conductor structures are also supported by special damping elements. These damping elements give the cores the necessary freedom of movement. Because, the more “turned back” the cable is, approaching the load limit, the more difficult it becomes for the cable to twist.
Particularly high are the demands on the shields. igus® brings various protection elements there: On the one hand, the design engineers place mechanical damping elements above and below the shield, so that the forces acting on the shield wires are not too large; on the other hand, special glide planes are incorporated under the outer jacket that will ensure the gliding of the cores among each other in the cable. Finally, the highly abrasion-resistant and halogen-free PUR or TPE jackets protect the torsion-optimised stranding elements against potential damage. This special structural design guarantees that even glass optical fibres function reliably in torsional applications. Tests have proved this with 27 million torsional movements.
igus® standard tests: Guaranteed quality for CF ROBOT cables
Specific igus® torsional standard tests are performed in order to evaluate the forces occurring in torsional movements: In our test lab all robotic cable types are fixed with a rotary- and fixed-point distance of one metre on both sides and twisted at a torsion angle of ± 180° at least three million times. The cables that are continuously monitored electrically with the automatic measuring system are then disassembled in order to evaluate any damage that may have potentially occurred to the non-measurable elements. Only cables that do not show any function damage after this igus® torsional standard test are included in the Chainflex® CF ROBOT.
About igus
igus® develops products based on a belief in making functionally advanced, yet affordable plastic components and assemblies, including Energy Chain ® cable carriers, Chainflex ® continuous flex cables, and Triflex ® robotic cable carrier systems. No maintenance, lower costs, longer life cycles – these key principles apply to all igus ® products, systems and services. Tried and tested in terms of durability, friction properties and stability, igus ® plastics are the technological core of the company’s range.
The content & opinions in this article are the author’s and do not necessarily represent the views of RoboticsTomorrow
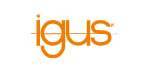
igus
The mission of igus® is to use its innovative polymer materials to develop products that provide creative solutions and exceed our customers' expectations while delivering fast, accurate service.
Other Articles
Automate 2025 Q&A with igus
Low-Cost Robotics Elevate Industrial Inspection Processes
7 Cable Management Mistakes to Avoid
More about igus
Comments (0)
This post does not have any comments. Be the first to leave a comment below.
Featured Product
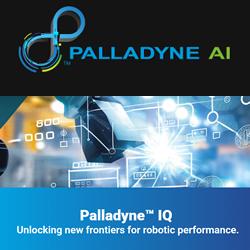