One of the major problems with a robot is sensor irregularity, where the sensors provide data that at times is accurate and at other times inaccurate.
Sensing, Measurement and Process Control Robots
Len Calderone for | RoboticsTomorrow
In order for robots to be more human-like, they need sensing capabilities. This gives robots the capability to see, touch and move, using algorithms that require feedback from the surrounding environment. Visual sensing utilizes cameras, lasers and radio frequency identification (RFID). This allows the robot to sense, estimate and match real life information with memory data.
Using visual sensing, a robot can figure out its position in relationship to an object, as well as the distance and angle from that object. It can also determine contour and seam measurement, as well as guide an object through assembly.
Robot sensors do virtually the same things we do but without thinking about it. Sensors allow the robot to see what in its vicinity. They can tell the robot what's near or far. Some sensors can determine the weather and others the exact location of the robot. There are sensors designed to discern light, sound, vibration, touch, temperature, humidity, pressure and more.
One of the major problems with a robot is sensor irregularity, where the sensors provide data that at times is accurate and at other times inaccurate. Sensors will intermittently generate noise in their output, or a proximity sensor might give problematic information. Sometimes this noise can be filtered by the software.
Another sensor problem is a failure to notice data. In this case, a sensor reading is not detected. This can be caused by surrounding conditions or battery strength. Therefore, care must be taken when programming the sensors.
More importance is being placed on the measurement of parts as they are being produced during the manufacturing process. By identifying defective parts early, the waste of completed materials can be avoided.
Measuring robots have been developed for inspecting large components. A robot arm, which contains a measuring head and probes, is employed in the production line, while multi-arm configurations are employed to inspect a wide range of products of different sizes. Such an arm is fitted with a multiple measuring head for fast and repeatable insertion of the probes in different positions, allowing complete inspection of a component with a single set-up.
KCS 780 Measuring robot from KINE Robot Solutions
The robot arms are mounted on the side of a work surface fitted to allow X-axis movement. The Y-axis is counter-balanced by an adjustable pneumatic system, which offsets the weight of the different probe configurations. The arms can be setup with different probes, such as thickness detectors.
A microprocessor controls the system processes, and records the data. An easy-to-use controller permits an unskilled worker to produce efficient measuring and data processing instructions for the machine. Production line changes can be made effortlessly, with a system that has self-teaching capabilities, which facilitates a program to be generated automatically when the first item of parts is being inspected manually.
Once the measurements are made, the system will produce the resulting data faster than it can be interpreted by the supervisor. This data is continuously prepared in statistical form, making it possible to develop cumulative results, from which movement can be quickly spotted and corrected before any components are manufactured with incorrect specifications.
A robot gauging control can be very beneficial when the parts that are being lifted by a robot need to meet exact specifications. Companies that build transportation vehicles have several parts that need to have specific weights. If these weights were to change significantly during the production process, it could affect the safety or cohesiveness of the entire vehicle. By using gauging controls on the robot’s probes, these weights are checked during the loading and unloading process, guaranteeing the accuracy of the production process.
Robotic control gages can also be utilized in grinding and material removal processes. When material is removed from a part, it weighs less than it did before removal. By employing robot gauging controls when removing a metal work piece from the material removal station, inspectors will know exactly the weight of the finished piece by subtracting the final weight from the beginning weight. This can help alert the inspectors of possible errors during the removal process.
The ROMER tube inspection solution from Hexagon Metrology Inc. uses infrared and laser technology to measure bend paths for tube inspections and reverse engineering applications. The system is able to be upgraded to interface directly to a CNC tube bending machine for instant corrections.
The process control robot is an automated flexible gauge, which is designed to work next to or even in the middle of machine tools. It has the ability to carry out automatic inspection routines on parts without interruption. It is designed as a single or dual horizontal arm measuring machine and can be placed in any production line. An integral rotary or flat table, which allows for access in pallet or gantry loading, can be added to the system.
The LPCS™ (Laser Process Control System) is a real-time quality control module for laser welding applications. The use of the LPCS allows detection of minute sized defects based on temperature and back reflection analysis of the molten weld pool.
The LPCS control algorithm is established for every weld configuration through pre-production welds and quality control. Weld pool data of production welds are processed by the algorithm and provide quality assessment with go/no go indication for every weld.
Process control requires the capability of providing direct feedback of gaging data. A measuring robot is used to supply accurate gaging data to help control the process and guarantee a successful manufacturing system. The measuring robot should have the capacity for electronic linkage with the control computer for the transfer line or flexible manufacturing system. Planning the gaging element in any automated system is critical to that system's success.
Furthermore, the gage is required to be as flexible as the manufacturing system in which it resides, and fast enough to keep up with the output of the manufacturing system. As users will be automating production of the most complex parts, which have rigid tolerances, the gage has to be highly accurate. Since temperature changes occur often, the robot must have as much thermal stability as possible in order to function under adverse conditions.
Manufacturers of coordinate measuring machines have developed a new type of measuring machine called the process control robot. The process control robot can be easily reprogrammed and retooled, and it has the design, operation, and control characteristics of a robot.
The process control robot is a highly integrated system of mechanical components, software, operating system, probes, and computers, which as a whole comprise sensing, measurement and process control robots.
For further information:
Len Calderone - Contributing EditorLen contributes to this publication on a regular basis. Past articles can be found with an Article Search and his profile on our Associates Page He also writes short stores that always have a surprise ending. These can be found at http://www.smashwords.com/profile/view/Megalen.
|
![]() |
The content & opinions in this article are the author’s and do not necessarily represent the views of RoboticsTomorrow
Comments (0)
This post does not have any comments. Be the first to leave a comment below.
Featured Product
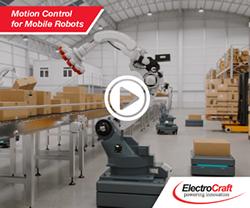