Replacing legacy application-specific integrated circuits (ASIC) with x86 architecture allows the company to deliver products just in time and to achieve about 20 percent of overhead in inventory.
Contributed by | Nexcom
Introduction
As commerce becomes increasingly global, manufacturers face evermore competitive pressures and threats. Every penny of extra cost must be cut and every ounce of efficiency must be extracted from a plant in order to remain competitive.
To that end, one of NEXCOM’s customers examined its smartly tuned network of 300+ factories and plants and asked the question: Where can we save? Their answer surprised everyone: a distributed control system (DCS) with Intel Inside ® . The DCS is widely used around the world for process automation applications. However, for smooth operations, long-term maintenance, and minimum disruptions of obsolescence, an Intel processor-based DCS solution was selected with the aim of cutting total cost of ownership (TCO) and boosting operational efficiency.
NEXCOM, an Associate member of the Intel ® Internet of Things Solutions Alliance, explains that its customer, Formosa Plastics Corp (FPC), called on its substantial manufacturing prowess to discern the inefficiencies in its proprietary DCS system, and address its uncertain product cycle and high-inventory risks. Once identified, FPC began an overhaul of its DCS strategy, which involved development of a custom solution built on non-custom Intel processor-based parts. FPC expects to realize substantial TCO reductions as a result, along with a significant boost to both operational and maintenance efficiency when all new systems are fully deployed.
Business Need
FPC is a large, world-class petrochemical manufacturer with more than 300 plants dispersed around the globe. These include oil refineries, steel mills, petrochemical factories, and power plants. To ensure smooth operation of these large-scale facilities, the company used a variety of DCS systems—as many as 26 different brands—to address the varying requirements of different control environments.
While this approach gave FPC the needed versatility for its many different plant types, it was highly inefficient from a maintenance and operational standpoint and also carried a high TCO. An extensive inventory of spare parts and a wide- scale investment in knowing how to maintain these systems only added to operational cost and complexity. Company leaders surmised that a standardized solution, such as an Intel ® architecture-based system, could eliminate much of this overhead and boost FPC’s overall competitiveness by leveraging its in-house customization capability.
Technology Requirements
The first requirement for a standardized DCS solution was a unified hardware platform that could be used in all of FPC’s facilities and configured to provide different features and carry out varying tasks as needed. FPC decided that an open architecture with long-life support and generational compatibility would be essential to its goal of reducing inventory and maintenance costs and lowering overall TCO. Plus, a scalable architecture would allow FPC to craft a single solution with the flexibility to adapt to the specific requirements of different environments—a much easier approach than using a different system for each control scenario, such as MMI, controller, gateway, etc.
Because the DCSs had become a vital tool to ensure smooth plant operations and help avoid production interruptions, FPC required built-in mechanisms for high reliability and fault tolerance. In addition, the DCS solution had to support the real-time control units directly and indirectly linked to it; accuracy and precision were key. For these reasons, the company required a computing platform with the ability to handle multiple tasks simultaneously at high clock speed without interruption.
Solution
FPC‘s standardized solution for DCS, called FORMOSA- FX*, is composed of several subsystems. Each is made up of multiple units, and all can use the unified hardware platform that was developed in collaboration with NEXCOM. The unified hardware platform itself comprises multiple Intel ® processor-based components, including an industrial PC and NEXCOM’s NISE* 3660, which plays two roles simultaneously: redundancy controller and man- machine interface (MMI).
The FORMOSA-FX* DCS uses NEXCOM NISE* 3660 as an MMI.
The FORMOSA-FX* system uses NEXCOM NISE* 3660 as a DCS controller.
With all of the different factory environments in mind, FPC developed a best-of-breed DCS solution that works across multiple control processes, including MMI, control, and I/O. The solution has been used in power generation, cogeneration processes, and midstream and downstream processes.
NEXCOM Adds Value
FPC selected NEXCOM to help with the development of its custom DCS for multiple reasons, including previous favorable experiences with an earlier generation NEXCOM MMI system. Plus, NEXCOM is one of the only industrial PC companies with DCS expertise, including domain knowledge in DCS architecture hardware design. This expertise, coupled with a long track record of developing fanless PC-based controllers and panel computers for automation environments around the globe, gave NEXCOM the winning edge for this project.
NEXCOM’s NISE 3660 redundancy controller and MMI solution (see figure below) is equipped with all the functional interfaces required by both controller and MMI applications and can be used as one or the other depending on the need. In addition, the controller-specific interfaces and MMI-specific interfaces are on two different sides of the NISE 3660. This differs from most currently available, single-purpose controllers or MMI products that require companies to maintain inventories of both items.
For use as a redundancy controller, the NISE 3660 runs a real-time operating system to perform reliable control schemes and Microsoft Windows* for use as an MMI that delivers high-resolution graphics.
The FPC FORMOSA-FX not only provides controller redundancy but also I/O redundancy as illustrated below. Every active controller is connected to a backup controller with two LANs. Based on NISE 3660, the FORMOSA-FX also supports fieldbus technology to connect to PLCs and remote I/Os; PROFIBUS compatibility has been tested and certified by the customer.
NEXCOM NISE* 3660 as deployed in the customer’s DCS
Why Intel?
Both NEXCOM and FPC offer multiple reasons for selecting Intel processor-based components for their new DCS design. The reasons include performance, long-life support, generational compatibility, and scalability. For example, multicore Intel processors run at high clock speed and can perform multiple jobs simultaneously—carrying out one major task with one computing core, while performing additional tasks with another. This enables one Intel processor to replace several legacy processors, improving the overall cost/performance (C/P) value of the solution.
FPC also expects to reduce inventory costs, while continuing to deliver the highest C/P value by following the Intel ® Embedded Product Roadmap and benefiting from the Intel commitment to long- time product availability. This enables FPC to reduce inventory for the typical 10-year life cycle of the DCS controller compared to previous solutions. And because the company’s plants are different in scale and its control systems have different functions—such as control, protection, and monitoring—DCS solutions with different computing performance requirements are needed. Intel ® Core™ and Intel ® Atom™ processors are helpful in enabling a single solution that scales appropriately.
Conclusion
FPC is in the process of finalizing the deployments of its new-generation DCS solution. The completed project is expected to yield significant gains in factory and plant efficiency, while dramatically cutting TCO through the adoption of a new Intel ® architecture-based DCS system.
According to FPC’s project manager, replacing legacy application-specific integrated circuits (ASIC) with x86 architecture allows the company to deliver products just in time and to achieve about 20 percent of overhead in inventory. Moreover, it reduces the effort of lifetime cycle maintenance and mitigates the risk of obsolete hardware components by about 15 percent to 30 percent. Also, the fanless NISE 3660 consumes little power and helps reduce energy by 40 percent compared to the legacy MMI.
Both NEXCOM and Intel are committed to delivering solutions that help customers build the most modern DCS system and minimize their total cost of ownership. NEXCOM is an authorized distributor of the DCS system for the global market. To learn more, please visit www.intel.com/industrial or www.nexcom.com.
About NEXCOM
Founded in 1992, NEXCOM has five business units which focus on vertical markets across industrial computer, in-vehicle computer, multimedia, network and communication, and intelligent digital security industries. NEXCOM five its customers worldwide through its subsidiaries in seven major industrial countries. NEXCOM gains stronghold in vertical markets with its industry-leading products including the rugged fanless computer NISE series, the in-vehicle computer VTC series, the network and security appliance NSA series and the digital signage player NDiS series.
The content & opinions in this article are the author’s and do not necessarily represent the views of RoboticsTomorrow
Comments (0)
This post does not have any comments. Be the first to leave a comment below.
Featured Product
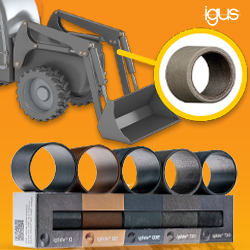