Solving the challenge of data interoperability exists for the IT function in many situations. For the connected factory this means enabling the flow of information between machines, which in the past has been easier said than done.
Removing the Roadblocks of Machine to Machine Communication in Manufacturing
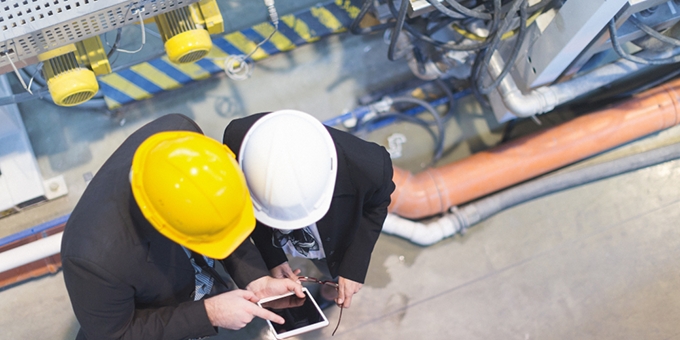
Contributed by | OTTO Motors
A big part of maximizing the value of industrial automation, and full realization of the benefits of Industry 4.0, is the flow of data and information. This has applications in a lot of environments, such as within manufacturing plants, warehouses, and distribution centres.
Also known as interoperability, this presents common challenge for companies since overcoming the difficulties of connecting machines and equipment made by different companies is rarely simple. Companies design products to make data exchange easier between their own equipment but don’t place as much importance on how those products communicate with the products of other companies.
Of course, making the connections that enable information to be shared is just the first step. The goal of Industry 4.0 is really about the ability to generate meaningful and useful data for the entire operation.
The Interoperability of Self-Driving Vehicles
In the context of material handling, this challenge can relate to the connectivity of self-driving vehicles (SDVs) and the role they play within a facility. Self-driving vehicles can be a core part of Industry 4.0 for many businesses, and are integral to the Industrial Internet of Things (IIoT) and the overall efficiency of a facility..
Connectivity that allows operators to communicate to, and receive information from, SDVs is a must. Practical examples can include an SDV calling for more inventory based on real-time lineside inventory levels, obstructions that may affect the flow of materials, and other details of what else is happening in production at that moment.
Overcoming the challenge of interoperability starts by creating a consistent framework for different machines to talk.
How does the OPC Unified Architecture (UA) platform help connectivity?
As we’ve identified, it’s a common problem for factories who operate multiple PLCs (Programmable Logic Controllers), like those in SDVs or otherwise, to end up with equipment than cannot readily communicate with other equipment. “Out of the box” they can only talk to other products manufactured by the same company. To make it work, operators are often forced to customize program connection drivers that enable these different connections to communicate with each other. This is an inherently time, resource and cost intensive process.
To make these connections easier, the industry is moving towards a broadly adopted communication protocol called OPC Unified Architecture.
What is OPC UA?
From the OPCFoundation.org website: The OPC Unified Architecture (UA), released in 2008, is a platform independent service-oriented architecture that integrates all the functionality of the individual OPC Classic specifications into one extensible framework.
This multi-layered approach accomplishes the original design specification goals of:
-
Functional equivalence: all COM OPC Classic specifications are mapped to UA
-
Platform independence: from an embedded micro-controller to cloud-based infrastructure
-
Secure: encryption, authentication, and auditing
-
Extensible: ability to add new features without affecting existing applications
-
Comprehensive information modeling: for defining complex information
Self-Driving Vehicles and Machine to Machine Communication
What does this look like in practice for manufacturers using SDVs?
The large part of the value of self-driving vehicles like OTTO is derived from their ability to make decisions and take action based on changing circumstances in real-time. When SDVs are on their job, it is vital that information on what they are doing and experiencing is fed back - especially when it involves any deviation from normal operating circumstances. There is value in other information that SDVs can feed into the network, as well. SDVs can also be programmed to provide advance notice that helps facilitate material flow, such as by signaling the shipping department that a pallet of completed product is on it’s way.
With connectivity established on the UPC UA, control over SDVs improves as well. Users can pause, unpause, switch off/on autonomy mode for SDVs. They can also query the state of the mission and understand exactly what the OTTOs are doing.
Solving the challenge of data interoperability exists for the IT function in many situations. For the connected factory this means enabling the flow of information between machines, which in the past has been easier said than done. Leveraging the benefits of a unified architecture in smart equipment enables tools, like SDVs, to become integrated and enhance the benefits of the IIot. OTTO is on a mission to create more efficient material flow in industrial environments. Part of this commitment becomes creating ways in which the entire manufacturing facility, warehouse or distribution center can benefit from the self-driving vehicle. For the connected facility, this means enabling the flow of information between machines with the use of OPC UA and the OTTO Industrial API.
Published with permission from the OTTO MOTORS blog.
The content & opinions in this article are the author’s and do not necessarily represent the views of RoboticsTomorrow
Comments (0)
This post does not have any comments. Be the first to leave a comment below.
Featured Product
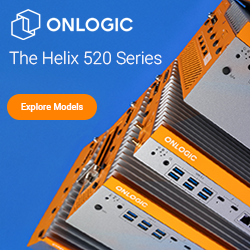