Traditional robots have been designed to perform a single task extremely efficiently. But when the item or the task changes, which is often the case with food, these traditional machines need to be reintegrated and reprogrammed
This Robot Has Soft Hands. It Could Be the Future of Sustainable Production

Carl Vause | Soft Robotics
Reprinted with permission from Soft Robotics:
In 2011, Professor George Whitesides of Harvard University helped rewrite the rules of what a machine could be. He developed biologically inspired 'soft robots', in collaboration with Harvard and the Pentagon's Defense Advanced Research Projects Agency (DARPA).
The challenge he undertook was to create a robot that could manoeuvre through a gap less than two centimetres high. While most robotic engineers tried using traditional, rigid robots, Whitesides drew inspiration from nature and living organisms. He created a new class of soft robots, made entirely from compliant, elastomeric polymers. In contrast to robots made from rigid materials, the soft robot’s flexibility enabled it to accomplish the DARPA challenge easily. It was a breakthrough in the field of robotics.
The earliest technological applications to come out of the DARPA collaboration were in the biomedical field. Soft robotics could be used, adaptively and delicately, to manoeuvre around the body during invasive surgery, or safely transport organs and soft tissue without damage. But it was not long before industrial automation would emerge as an application for this groundbreaking technology.
Industries such as e-commerce, advanced manufacturing, and food and agriculture have been under increasing pressure to find automation solutions to handle a declining labour pool, rising customer demand, and, in the case of food, increasingly stringent safety standards. However, the variable and fragile nature of these industries' products has largely excluded them from automation.
While Whitesides’ work spawned an entirely new focus area for academic research and development, in 2013 Soft Robotics Inc. emerged as a pioneering force developing the first and only commercial applications. It advanced this technology into a commercial product that could unlock automation for industrial customers around the world. By leveraging patented material science and AI, Soft Robotics builds automation solutions that can grasp items with the same dexterity as the human hand. It is revolutionizing robotic automation to feed the world, and enable industrial productivity in every market.
Why do we need soft robotics?
Food handling and packaging, primarily in produce and baked items, is a highly manual process. Labour costs represent a significant input into total product cost. Historically, workers in these markets have been sourced through low-cost migrant labour. But in the past few years, we have seen a significant reduction in the availability of labour for produce and other food production markets.
Whether it is reduced migrant labour in Salinas, California, or the impact of Brexit on labour flows to the UK from EU countries, or the newly passed regulatory barriers to ‘backpacker’ labour in Australia, this is a global problem. It is having a direct impact on the cost and supply of food around the world. As labour continues to become more scarce, producers are turning to automation to maintain productivity and, in many cases, the economic viability of their food production businesses.
Traditional robots have been designed to perform a single task extremely efficiently. But when the item or the task changes, which is often the case with food, these traditional machines need to be reintegrated and reprogrammed, which can take hundreds of hours and significant capital investment.
This problem is not just limited to food. With increased demand for consumer goods, and labour constraints in industries such as advanced manufacturing and e-commerce, the need for robots to solve dexterous manipulation is stronger than ever. Even the US government cites "flexible gripping mechanisms that allow for dexterous manipulation of everyday objects" as a "national imperative", in its 2016 Roadmap for Robotics report.
The content & opinions in this article are the author’s and do not necessarily represent the views of RoboticsTomorrow
Comments (0)
This post does not have any comments. Be the first to leave a comment below.
Featured Product
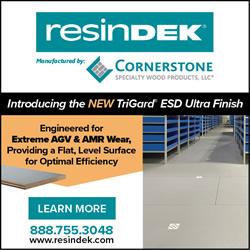