Below, we'll look at piezoelectric and piezoresistive effects. Neither of those is new, but engineers are applying them in creative ways within the field of robotics or through methods that may one day improve robotics.
Piezoelectric and Piezoresistive Effects in Robotics

Kayla Matthews | Productivity Bytes
Today's robotics feature an array of forward-thinking technologies permitting advancements that might not be possible otherwise.
Below, we'll look at piezoelectric and piezoresistive effects. Neither of those is new, but engineers are applying them in creative ways within the field of robotics or through methods that may one day improve robotics.
To clarify, piezoelectric effects produce an electric charge in response to pressure, while piezoresistive effects change a material's resistance with the application of pressure.
Piezoresistive Materials Used in Tactile Applications
The piezoresistive effect was the center of research carried out with tactile sensors. Those researchers were hopeful about the possibility of using them embedded in films to improve the sensitivity of things such as smartphone screens. However, since robotics equipment often needs to grip things, such sensors may work in that industry, too.
For example, a flexible film equipped with tactile sensors could get applied to particular sections of a robotic hand. A different study conducted several years ago found piezoresistive sensors were best for pressure-sensitive robotic applications. But, newer research might demonstrate how far scientists have come in a relatively short time.
Scientists Discover a New Piezoelectric Ceramic Material
For most modern applications within the robotics sector and outside of it, users prefer piezoelectrics in crystal form. They offer the highest electrostrain values compared to other materials. The electrostrain value is a measure of how much a material changes in response to an electrical field.
However, crystal-based piezoelectrics are expensive and difficult to manufacture, making them impractical for widespread use. Scientists at the Indian Institute of Science say they've found a ceramic a hundred times cheaper than piezoelectric crystals but capable of an electrostrain value near the record set by a crystal piezoelectric substance.
Moreover, the scientists say their ceramic is like a stretchable rubber. That elastic quality meant that the electrostrain value remained nearly constant with each application of voltage. In contrast, most ceramic piezoelectrics lose electrostrain value over time because they don't return to their original states between voltage applications.
Although the team did not specifically apply their findings to robotics, this new material could pave the way for manufacturers using piezoelectrics in broader applications using cost-effective methods.
Disney Software Allows for Creating 3D-Printed Toys With Piezoresistive Parts
Time often passes between the discovery of a phenomenon and its application in real-life uses. Such was the case with both the piezoelectric effect — discovered in 1880 — and piezoresistive effects. For example, the latter was recognized in 1856 by Lord Kelvin, an Irish physicist, but did not get formally recognized until approximately a century later.
Now, the phenomenon is relied upon in numerous applications. Lord Kelvin could not have fathomed that one day, the effect he noticed would be incorporated into toys people could make with 3D printers. However, a piece of software offered by Disney allows for using 3D printing to make toys, then applying piezoresistive wires to them for toys that can tell when they're bent and by how much.
These objects are called 3D-printed flexible input devices. The initial tests with them involved an action figure and a musical instrument. However, concerning robotics, the team believes their findings could bring about robots that make more meaningful and realistic interactions.
A Light-Sensitive Pressure Sensor Could Improve Robotic Skin
Another advancement that could lead to better robotic skin for future applications relates to a pressure-sensing technology that picks up on light passing through tiny, embedded tunnels inside silicone. The team working on the project says their achievement could get wrapped around robot components in a sheet form.
Also, since the material is non-toxic, it also offers potential applications for use directly on the human body, such as blood pressure monitors.
Piezoelectric Actuators Applied to a Miniature Flying Robot
Figuring out the power supply requirements is especially tricky when designing a tiny robot that flies. They typically require tethers because onboard batteries are too bulky for the size. However, a new development features a laser-powered robot capable of making an untethered, albeit short, flight.
The wings have two piezoelectric actuators that need about 250 volts for maximum power density. However, the solar cell that's also part of the design only produces seven volts. To compensate, the researchers made a custom-designed boost controller that operated the wings, combined with a microcontroller.
Impressively, both of those things were small enough to get incorporated onto the robot without making it too heavy to fly.
Applicable to a Range of Robotic Uses
These examples prove the possibilities are virtually limitless for piezoelectric and piezoresistive effects applied to robots.
They also emphasize how the inner workings of robots are often exceptionally complex, requiring numerous parts to work together and contribute to the functionality.
The content & opinions in this article are the author’s and do not necessarily represent the views of RoboticsTomorrow
Comments (0)
This post does not have any comments. Be the first to leave a comment below.
Featured Product
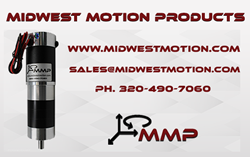