Using a myriad of technology including sensors, lidar, infrared and machine vision, mobile robots are now able to operate in less stable environments. This means that mobile robots are no longer simple, guided machines.
Making the Move to Mobile
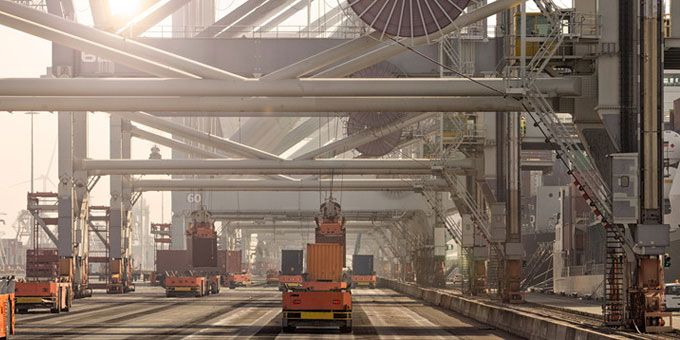
Jonathan Wilkins | EU Automation
Automated guided vehicles (AGVs) have been an industry staple since 1953. However, their reliance on environmental markers and the fact they follow a pre-determined route, means AGVs are best suited to working in structured environments in the absence of humans. Here Jonathan Wilkins, director at automation equipment supplier EU Automation, discusses the rise of mobile robots and what challenges need to be faced for their widespread uptake.
AGVs were the original mobile robot technology but advances in both machine vision and navigation means that more and more businesses are instead turning to autonomous mobile robots (AMRs). According to Research and Markets, the global autonomous mobile robot market accounted for $4.98 million in 2017 and is expected to reach $14.79 million by 2026, at a compound annual growth rate of 12.9 per cent. The warehousing and logistics industries are turning to mobile robots to solve employment and flexibility challenges in both factories and warehouses.
Using a myriad of technology including sensors, lidar, infrared and machine vision, mobile robots are now able to operate in less stable environments. This means that mobile robots are no longer simple, guided machines they are intelligent devices that can respond to environmental changes. To use an analogy, an AGV is more like a bus, following a pre-determined route, whereas AMRs are like taxis, they’ll go wherever is required.
AMRs will extend the benefits of collaborative robotics, or cobots, into applications that require movement around a facility. In fact, KUKA’S KMR iiwa is a cobot mounted on a mobile robot, combining the strengths of a robot arm with those of a mobile technology.
Reaching its potential
At the moment, robotics manufacturers are working hard to develop mobile robots that overcome challenges in power, payload and navigation. Mobile robots by nature, charge themselves, but to get the most out of the fleet requires optimized, intelligent charging. To achieve this, WiBotic has developed wireless charging solutions to enhance the working efficiency of robot fleets, maximizing battery life for each individual robot and creating an operational plan for batteries of the entire fleet.
Another challenge facing the technology is payload. For AMRs to appeal to a broader range of applications, they must be able to carry heavier loads. Waypoint Robotics is working on this and has launched an omni-directional AMR called MAV3K, which boasts a carrying capacity of over 1,300 kilograms — double that of previous models. It can be set up in less than 15 minutes and will remain charged throughout the working day. With the payloads of AMR’s increasing, so too are the number of applications, particularly in the aerospace and automotive industries.
The other obvious challenge for AMRs is navigation. Companies such as Mobile Industrial Robots (MiR) are working to tackle this, by incorporating laser scanners, 3D cameras and proximity sensors to detect features of the environment. The company is also adding artificial intelligence capabilities across all of its AMRs to improve route planning and driving behavior.
While many vendors are still offering the traditional AGV technology that has served us so well until now, the advanced navigation and obstacle avoidance of AMRs are causing manufacturers to make the move to mobile.
About Jonathan Wilkins
Jonathan Wilkins is the marketing director of industrial automation components supplier, EU Automation. A professional brand advocate and commercial marketing strategist, Jon focuses on delivering growth via a multi-channel approach that has a significant positive impact on business. He has been part of the EU Automation team since its humble beginning ten years ago and has over a decade of experience in marketing.
The content & opinions in this article are the author’s and do not necessarily represent the views of RoboticsTomorrow
Comments (1)
Featured Product
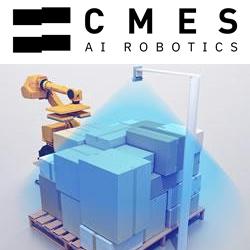