The start-up company NISI (HK) Limited is currently developing a miniature surgical robot that can be inserted though natural openings in the body and only unfolds inside the abdomen.
The Surgical Robot that Unfolds Inside the Abdomen
Stefan Roschi | maxon Group
In the world of medtech, there are many astonishing new developments these days. The world of surgical robots could soon be disrupted: In summer 2018, the Hong Kong-based startup NISI announced that they have successfully performed a series of gynecological operations on live pigs. This may not sound like anything special at first, however: The essence is that the surgeons used a small robot that had been inserted rectally. This is a world’s first in medical history, according to the company.
NISI was founded in 2012 and works with the universities of Hong Kong and Cambridge to develop a robotic system that enables complex, minimal-invasive surgeries in the abdominal and pelvic area without leaving visible scars. “We want to become the world’s leading expert in non-invasive surgical robotic technology,” says Dr. Corinna Ockenfeld at NISI. The successful surgeries in the summer of 2018 have given the medtech start-up a lot of momentum. Initial surgeries on humans are planned for 2021.
The idea behind the NISI’s novel surgical system is as follows: The surgical robot is inserted through a natural orifice, usually the anus or the vagina. By doing so, only a small cut inside the body is necessary to get multiple robotic instruments inside the abdomen. Current systems require several incisions, one for each instrument. The new technology has obvious benefits: Less blood loss during surgery, less wound related complications, shorter recovery time for the patient, and no visible scars.
The robot itself has two small arms that unfold inside the abdomen and can be controlled by the surgeon using a control panel. The two robotic arms are directly controlled by micromotors from maxon and have up to eight degrees of freedom. The system also has a high-resolution 2D and 3D camera and delivers haptic feedback, so that the surgeon is able to feel what is happening at the other end and can work with even higher precision.
Bringing surgical robots to the next level requires more than outstanding technicians and engineers: Quality components are a key element. NISI is therefore testing various concepts and combinations of components. “We want to push the boundaries of medical and robotic technology,” says Dr. Corinna Ockenfeld. With regard to the motors, this requires an extremely small size and extremely high power density. “We are working closely with maxon and have a weekly exchange of information. We really appreciate the support we’ve received over the past years. The collaboration with maxon is highly productive and extremely valuable for both sides.”
The prototypes of the NISI surgical robotic system currently use various brushless DC motors from the EC series, with diameters ranging from 4 to 8 millimeters, complemented by matching customized gearheads. Both partners are pushing the precision drives to their limits, sometimes running them outside the nominal specifications. However, the BLDC motors are customized for the specific needs. They require high power density, must fulfill extremely strict quality standards and be sealed against body fluids. In the future, the drives will also be biocompatible.
The next steps are to make the entire system even smaller, to make the motors even more dynamic, and to expand the working range of the robot. “We take care of every little detail and take innovative approaches to solving problems,” says Dr. Corinna Ockenfeld. Step by step, NISI is coming closer in fulfilling its vision of making non-invasive surgery without scars a commonplace reality.
The content & opinions in this article are the author’s and do not necessarily represent the views of RoboticsTomorrow
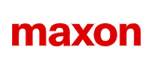
maxon group
maxon is a leading supplier of high-precision DC brush and brushless servo motors and drives. These motors range in size from 4 - 90 mm and are available up to 500 watts. We combine electric motors, gears and DC motor controls into high-precision, intelligent drive systems that can be custom-made to fit the specific needs of customer applications.
Other Articles
Multi-axis motion control drives pipe-based robots
Automate 2025 Q&A with maxon group
Understanding Torque and Speed in Electric Motors
More about maxon group
Comments (0)
This post does not have any comments. Be the first to leave a comment below.
Featured Product
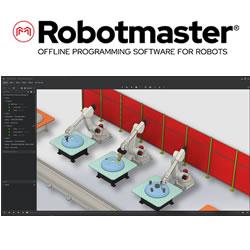