Not only can robots easily assist with large payloads and separate people from traditionally dirty tasks, but they also take mundane duties off of workers’ plates, such as fastening.
3 HR Headaches Robotics Can Solve
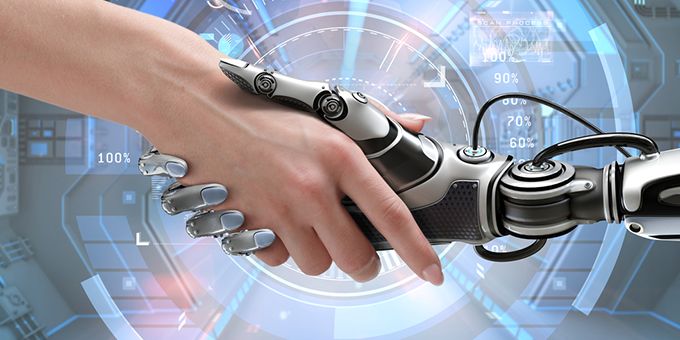
Simon Whitton | KUKA Robotics
What kinds of challenges are manufacturers experiencing in the industry?
The manufacturing industry is currently being hit hard by the labor shortage, which is also contributing to the industry’s skills gap. Since many of the Baby Boomers are nearing retirement or pursuing less laborious positions, the majority of manufacturers' talent is walking out the door. And considering the few new recruits who come in almost never have the same knowledge or skills their predecessors had, there’s a gap in the experience and skills set the manufacturers used to be able to tap into.
How do robots help improve worker retention?
I always point to the 3Ds: dull, dirty and dangerous. Robots take the heavy lifting out of the equation, both literally and figuratively. Not only can robots easily assist with large payloads and separate people from traditionally dirty tasks, but they also take mundane duties off of workers’ plates, such as fastening. When workers don’t have to worry about their safety and can focus their attention on higher-value tasks, like operations management, they’re going to feel more fulfilled at work and be encouraged to continue working for that company.
What kind of safety features do new-age robots have that minimize on-site injuries?
Sensors have revolutionized the robotics industry. Now robots are equipped with safety sensors so if someone comes too close to a robot while it’s working, the sensors will detect the proximity and will slow down or shut off completely to account for the worker’s safety. Employees working on the floor won’t have to worry as much about their safety since robots can minimize on-site injuries — whether the injury is from working with a dangerous machine or from a worker who lifted something too heavy and threw out his or her back. Robotic safety features can help improve worker safety and allow for closer collaboration.
Can collaborative robots keep up production-wise with traditional robots?
That depends on the stage of collaboration and the collaborative nature of the application. No matter what type of robot it is, if it’s around humans, it has to operate at a speed that’s safe for the operator to be there. A collaborative robot, by its very nature, is designed to be not as powerful. Therefore, its ability to harm is limited and its speed is restricted as well. It’s very safe, but it’s obviously compromised. So, even if you put a fence around it, its ultimate speed is dictated by the power it has, limiting how fast it can perform. Whereas, a standard industrial robot is not designed to work next to people and isn’t power and force limited. So, it can go as fast as the application calls for. And if you want to separate people from the robot without physical guards, you can use sensors to detect the presence of people and limit the motion of robots when they’re around.
The labor shortage is a pressing issue in the manufacturing space. Where do robots come into play?
Robots can help fill some of the gaps left by the lack of workers in a factory. They empower employees to take on more important initiatives, like production strategy, instead of concerning themselves with tasks like palletizing, fastening, assembling, etc. While manufacturers are struggling to recruit new workers, robots can help alleviate some of the production pressures by taking on some of the work that needs to be completed. We’re also seeing rise of advanced mobile robotics. Where traditional robotics has been seen as a fixed and/or static process, mobile robotics is expanding the possibilities and enabling the robots to move around workspaces to support people and processes. They’re also able to bring parts or equipment from one place to another, This not only expands workers capabilities, it allows manufacturers to utilize them in multiple applications.
What about the aging workforce … how can robots help?
Considering many aging workers are unable to take on strenuous tasks, robots can help them with heavy payloads, palletizing, moving products across the factory floor, etc. That way, older workers can keep their bodies in the best shape possible, allowing them to get the most of their work experience, whether that be working for longer or performing better in the timeframe they do work. Older workers can use some of this additional time to mentor younger workers, passing on their tribal knowledge and closing the skills gap as well.
What can we learn from Japan in this respect?
Well, Japan is battling an aging population, with a median age of around 47. They’re very accepting and encouraging of their adaptation of technology across the country. They have lots and lots of automation in people’s daily lives, like intelligent vending machines, for example. So, within industry, robots are already a widely accepted form of automation there. In fact, Japan is always among the top 2 or 3 countries across the world (along with South Korea and China). The leading adopters of robotics all have the same challenges: falling birthrates and aging populations that need automation to fill in for the reduced number of young people needed to for manufacturing. The West is experiencing these same obstacles, so it behooves us to learn how others have adapted to these issues.
About Simon Whitton
Simon Whitton is the Senior VP of Sales & Marketing of KUKA Robotics in North America where he oversees KUKA's welding, electronics and mobility centers. Simon has more than 30 years of experience in the robotics and electronics industries and has extensive knowledge in robotics, electronics, manufacturing and more.
If you like this article you may like "Is Software the Future of Robotics?"
The content & opinions in this article are the author’s and do not necessarily represent the views of RoboticsTomorrow
Comments (0)
This post does not have any comments. Be the first to leave a comment below.
Featured Product
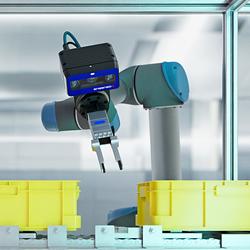