More flexible materials are necessary for safer collaborative work alongside humans and delicate tasks usually performed by humans, such as picking fruit and vegetables or performing minor surgeries.
A Guide to Self-Healing Robots
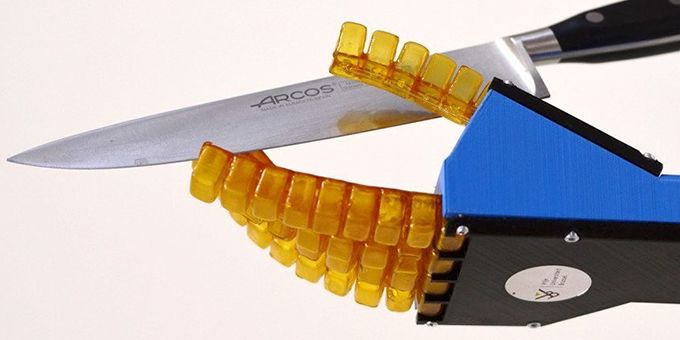
Ashley Halsey | LuckyAssignments and Gumessays.com
Robots are becoming more and more popular as automated replacements for filling low-skilled jobs. While robotic assistance in labs and factories has been commonplace for some time, but robots are soon to be even more widely in household use in the coming years. But for this to happen, more flexible materials are necessary for safer collaborative work alongside humans and delicate tasks usually performed by humans, such as picking fruit and vegetables or performing minor surgeries.
Soft, Flexible Materials
These activities require a level of dexterity which the current models of robots cannot achieve, so new materials which are softer, more flexible, described as ‘jelly-like plastics’, are being developed as a solution to many challenges faced by using robots. They are also cheaper and easier to produce, as they can be 3D printed.
Such dexterous robots are able to manipulate fragile objects carefully without damaging them, while being much safer for humans to work with/around in factory environments, for example.
This is making huge progress in the agricultural sector, as fruits and vegetables can be efficiently picked and placed securely. However, the delicate nature of the materials combined with the very smooth gripper surfaces to prevent bacteria/fungus growth (which need porous surfaces) these robots are much more vulnerable to cracks, rips, and other damages.
Consequently, these next generation robots are somewhat impractical for real-world use, until recent advancements in self-healing robotic technology have made headway.
SHERO
Funded by the EU for 3 million euro ($3.36 million), the Free University in Brussels (Vrije University of Brussels or VUB) has been working with the University of Cambridge, the Ecole Supérieure de Physique et de Chimie Industrielles (ESPCI) in Paris, the Swiss Federal Laboratories for Materials Science and Technology, and the Dutch polymer manufacturing firm SupraPolix.
Dubbed the ‘SHERO’ (Self-Healing Soft Robot) project, researchers at VUB have been developing robotics made from flexible plastics that have the ability to detect their own damage and make repairs without the need for human intervention.
David Walker, a tech blogger at Writinity and Last Minute Writing, writes: “Machine learning has been used throughout this ground-breaking process to design and integrate self-healing polymers which can create new bonds autonomously to repair damages.” Sensor fibers are embedded into these polymers, which can then detect the location of the damage and begin to actuate the healing process. The robots are then able to create new bonds in the damaged location and, depending on the location and the extent of the damage, can take anywhere from just a few minutes to a week (at room temperature) to patch themselves up.
As Jennifer Vanhoy, an IT expert at Draftbeyond and Researchpapersuk, says, “This industry-changing development means the process of repairing damage to robots is entirely automated, removing the need for heat-activated systems via human intervention (through touch).”
A Cheaper, Safer, Sustainable Solution
The cost of robot repairs and replacements is incredibly high, so the introduction of self-healing technology is not only game-changing, but can help to reduce the need for time-consuming, complex, and expensive repairs. It also has implications for sustainability, as robots will have to be replaced with new models less often, since they can perform standard maintenance independently and autonomously.
Self-repair mechanisms in robots also means they are less of a risk to the humans that may be working with or near them, since they are unlikely to cause any real damage due to their gentle, flexible nature. This makes work environments with increasingly high populations of robotic ‘workers’ much safer for human workers and the products.
By developing soft, safe materials embedded with polymers which can sense and locate damages and trigger the healing process without human interference, robots traditionally found as automated workers in factories and labs will soon begin to move into more environments, such as agriculture, and into the average household. Users or owners of such robots will avoid the need to seek out costly repairs for damages sustained and can instead take advantage of this safe, sustainable alternative, putting this at the forefront of developing a new generation of robotics.
About Ashley HalseyAshley Halsey is a professional writer for Luckyassignments.com and Gumessays.com who has been involved in countless projects across the country. Ashley is a mother of two and, in her free time, she enjoys traveling, reading, and attending business training courses.
If you like this article you may like "Smart Gripper for Small Collaborative Robots"
The content & opinions in this article are the author’s and do not necessarily represent the views of RoboticsTomorrow
Comments (0)
This post does not have any comments. Be the first to leave a comment below.
Featured Product
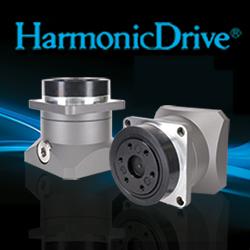