The ElectroCraft CompletePower™ Plus Universal Drive takes the guesswork out of selecting and configuring a drive and motor combination by incorporating all of the features and functions necessary to provide optimal control of a wide variety of brushless DC motors.
ElectroCraft Drives Feature Easy Setup and Operation
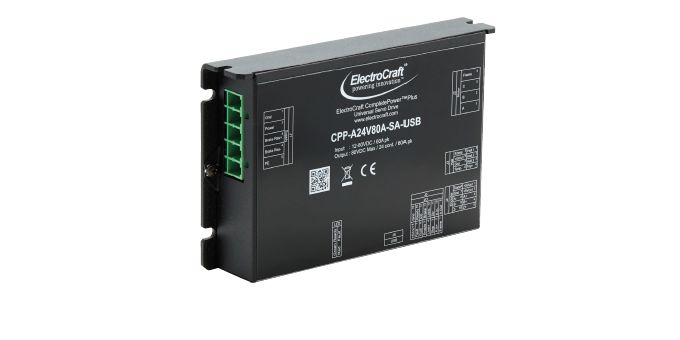
Scott Rohlfs | Electrocraft Inc.
DC motor drives are widely used across multiple sectors, including medical and life sciences, industrial automation, robotics, agriculture, military and defense, energy and transportation.
The function of a drive is to interpret digital or analog commands from a control system, and convert those commands into electrical current. The current is transmitted to a motor in order to produce motion that is proportional to the command signal. Typically, a command signal represents a desired motor speed, torque or position.
DC motor drive technology can range from very simple analog speed control with two-quadrant operation and trapezoidal commutation to very complex four-quadrant operation with sinusoidal commutation and field-oriented control, capable of providing precision speed, torque and positioning control.
DC drives are also typically designed to control a particular type of motor technology among brushless DC motors, permanent magnet DC brush motors or stepper motors. While a wide range of motor and drive combinations are possible, it is important to select a drive that is optimal for a particular motor type and capacity.
When selecting a drive, there are multiple specifications that should be considered, including continuous current, which is the maximum current available to the motor during continuous operation; peak current, which is the maximum current available to the motor during intermittent operation; supply voltage, which is the voltage supplied to the drive; and motor voltage, which is the voltage supplied to the motor from the drive.
Motor feedback should also be considered, which includes Hall sensors for motor commutation and speed feedback; encoders for motor commutation, speed and position feedback; or a combination of Hall sensors for commutation plus encoder for speed and position feedback.
ElectroCraft's Universal Drive technology
The ElectroCraft CompletePower™ Plus Universal Drive takes the guesswork out of selecting and configuring a drive and motor combination by incorporating all of the features and functions necessary to provide optimal control of a wide variety of brushless DC motors, permanent magnet DC motors and stepper motors, all within the same platform that also includes an intuitive and highly configurable user interface.
A major benefit of ElectroCraft's Universal Drive is that users only need to understand how to operate a single product that can be easily configured to control different types of motors with various operating modes and control methods. Users can select from preconfigured settings and tuning parameters using the built-in motor database, meaning that most of the device setup can be completed in seconds with an easy-to-use interface.
The drive hardware is scalable and offers four different capacities, supporting 12 to 80 V DC motor windings and providing up to 24 A continuous and 60 A peak output current, enabling operators to match drive and motor specifications. The benefits from this flexibility include cost savings and performance enhancements that result from properly matched equipment.
As mentioned, the Universal Drive is fully compatible with a wide range of motor types, including brushless DC and permanent magnet DC (PMDC) brush motors, as well as open- and closed-loop stepper motors.
For more information contact ElectroCraft:
The drive features multiple control methods to suit individual application demands. These include analog speed control, analog torque control, as well as step and direction positioning control. Speed, torque and position control will also soon be available via built-in controller area network (CAN) bus interface.
Users can select between two-quadrant or four-quadrant operation as well as trapezoidal or sine-wave commutation for brushless motors using either Hall sensors or encoder feedback. These drives also include advanced field oriented control (FOC) for brushless and closed-loop stepper motors. The FOC features provide high dynamic response, resulting in a robust motor controller with low torque ripple that produces smoother, more efficient motion.
Figure 2. The ElectroCraft CompleteArchitect™ allows automatic drive configuration and more. Source: ElectroCraft
The drives are easy to set up and configure via a Universal Serial Bus (USB) interface and the ElectroCraft CompleteArchitect™ Windows-based software. The USB interface is convenient for connecting to most modern devices. It provides fast communication and enables real-time monitoring and diagnostics of critical signals and waveforms.
The software will automatically configure the drive settings for ElectroCraft motors, making it nearly plug-and-play. The software also provides built-in tutorials and help functions, eliminating the need to read a manual or seek training. Built-in diagnostics and monitoring functions also provide detailed information, including real-time graphs of critical waveforms, letting users fine tune the drive quickly and easily.
ElectroCraft's PRO series drives
For applications that require even more advanced control capabilities, ElectroCraft's PRO series drives incorporate a fully programmable motion controller with built-in networking.
Drives are available in a variety of hardware configurations, including stand-alone, PCB mount or as part of an integrated motor drive solution.
Networking options include CANopen® or EtherCAT®.
Whether controlling a single drive or multiple drives in a networked system, configuration and programming are easy using ElectroCraft's Motion PRO suite.
For more information contact ElectroCraft:
The content & opinions in this article are the author’s and do not necessarily represent the views of RoboticsTomorrow

Electrocraft Inc.
ElectroCraft, Inc. is a global provider of dependable, application-engineered fractional-horsepower motor and motion products. Our products are found in thousands of different applications within industrial, commercial, and consumer product markets. While ElectroCraft provides a wide array of standard products with many configurable options, we have built our brand on custom OEM solutions that meet the precise performance, cost and quality our customers require.
Other Articles
Why this wheel drive is getting so much attention from design engineers
ElectroCraft’s MPW Wheel Drives Offer Best-in-Class Mobile Robot Solutions
Integrated Wheel Drives Lower Cost of Mobile Robot Ownership
More about Electrocraft Inc.
Comments (0)
This post does not have any comments. Be the first to leave a comment below.
Featured Product
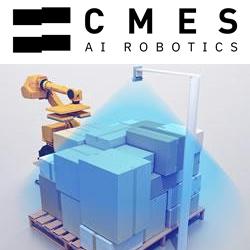