The introduction of modern automation technology into the sensitive production areas of pharmaceutical and medical technology was rapid. However, the conditions for the entry of systems, components and robots into this sector are anything but easy to meet.
Case Study: Grippers from Zimmer Group Automate a Cleaning Machine for Sterile Glass Vials
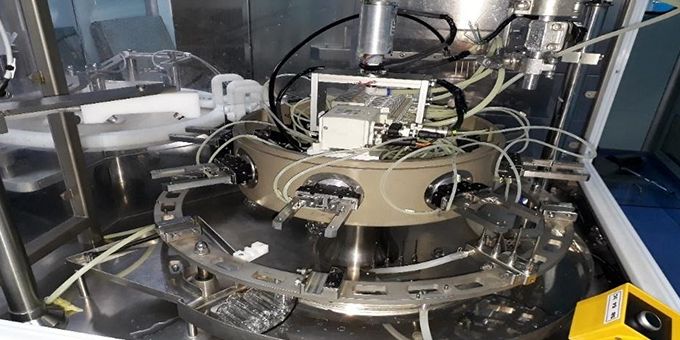
Case Study from | Zimmer Group
The introduction of modern automation technology into the sensitive production areas of pharmaceutical and medical technology was rapid. However, the conditions for the entry of systems, components and robots into this sector are anything but easy to meet. For example, systems for medical technology must in most cases meet demanding clean room classifications and the components must also be suitable for use under such adverse environmental conditions.
In the search for a new gripper solution for a newly developed application that is part of an automatic packaging line of a pharmaceutical company, the Tunisian automation specialist SEA electronics therefore found what it was looking for at Zimmer Group France - a French subsidiary of the German Zimmer Group. This is because the company's extremely broad product range includes a number of cleanroom-certified and cleanroom-suitable components such as grippers and swivel units. The fact that the Tunisian automation specialist has already been working successfully with the French company on other projects for many years was a great advantage.
SEA electronics from Sousse - a port city and at the same time the third largest city in Tunisia - was founded in 1994. Initially, the young company helped the local industry to increase its productivity. Relatively quickly the company became successful and became a certified Siemens Solution Partner. A few years later, the company founded SEA Trading and SEA International to devote more attention to foreign projects.
Glass vials are cleaned automatically
But now back to the application: The original automated cleaning machine, which can clean small sterile glass bottles called vials, consisted among other things of a rotary table and eight standard pneumatic rotary grippers from a market companion. By means of a filling device, the vials are filled with sterile water, then reach a rotary table for cleaning. Afterwards, the vials are grouped in a fours and fixed by a gripper attached to a swivel unit. The gripper then rotates through 180° to empty the vials again. The turntable then moves to the second position. There a cleaning process is started for the gripper or for the vials which it still holds with the opening pointing downwards. A washing needle penetrates into the bottles and cleans them with a jet of water. The gripper then moves back to its starting position (180° turn in the opposite direction). In the last step, the gripper places the bottles on a conveyor line for the drying and product filling process.
Problems with downtimes
The Tunisians were particularly worried about the many successive stoppages of the washer due to alarms (malfunction of the encoder). During an inspection of the machine's functional sequences, it was discovered that one of the grippers used was turning with difficulty, which jammed the transfer turret at the discharge guide and subsequently caused the machine to come to a standstill. After a precise diagnosis of the malfunction, for which the gripper had to be removed, the experts from SEA electronics had noticed signs of corrosion and rust on the bearings and inside the cylinder, and could therefore conclude that the problem was primarily due to the gripper's tightness.
The defective and rusty grippers could not withstand the adverse conditions in the press and had to be replaced
It was decided to replace the existing gripper with a new sealed gripper, which can ensure perfect functioning and adapt to the very humid climatic conditions of the washer. The Zimmer Group was able to score here with its pneumatic GPP5004N-21-A gripper.
Designed for universal use
The grippers of the GPP5000 series with their robust, hard-coated steel-in-steel profile linear guide were designed for true universal use. Depending on the variant, they have a number of features (speed, high gripping forces, long gripper jaw lengths) and thus offer the right solution for every application. When using a protector, the grippers have a sealing class of IP67 - ideal for use in clean rooms or in the damp ambient conditions of a cleaning machine.
Space problems in the bottle washer
The space available at the customer's premises was limited, so a very compact design was required. Here, the Zimmer Group grippers, which feature a variety of detailed solutions and thus facilitate daily use, were able to gain further plus points by often eliminating the need for accessories. For SEA electronics it was also not insignificant for the trouble-free operation of the machine that the GPP5000 grippers with their low coefficient of friction and good emergency running characteristics are able to handle 30 million cycles without maintenance.
Since the grippers must perform a rotary movement within the cleaning machine, the developers at SEA electronics also installed the flat swivel unit MSF44N-D2 from the Zimmer Group. The swivel unit ensures a gripper rotation of 180 degrees. With a weight of the gripper, jaws and the bottles of about 600 grams, this unit had to ensure the rotation in 0.2 seconds.
The grippers and swivel units of the Zimmer Group installed in the machine
After the successful commissioning of the bottle washer with the new grippers, Nouira Majdi of SEA electronics draws an all-round positive conclusion: "The machine runs well and absolutely trouble-free. Our expectations of the grippers have been fully met. The speed or cycle time with the grippers from the Zimmer Group was identical to the previous models. Productivity was also significantly increased because there were no more machine stops". The end customer was also impressed by the technical performance of the Zimmer Group grippers and its wide range of products.
The content & opinions in this article are the author’s and do not necessarily represent the views of RoboticsTomorrow
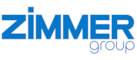
Zimmer Group US, Inc.
Are you interested in premium products in the fields of mechanical and plant engineering? Do you want to learn more about our solutions in the fields of automation, damping, linear, processing, tooling, and machine tooling technology?
Other Articles
Converting Passenger Aircraft to Freight Aircraft - the Zimmer Group Is on Board!
Automated Loading and Unloading of CNC Machines
2021 Top Article - How to Find the Right Damper for Your Application
More about Zimmer Group US, Inc.
Comments (0)
This post does not have any comments. Be the first to leave a comment below.
Featured Product
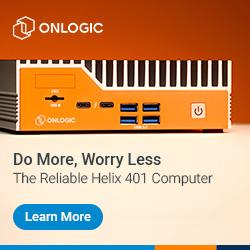