When HP set out to develop this technology, the aim was to push beyond prototyping and enable repeatable, higher volume additive manufacturing. We can do this by combining a powder bed fusion approach with HP’s Thermal Inkjet (TIJ) technology.
HP Multi Jet Fusion 3D Printing Technology for End of Arm Tooling
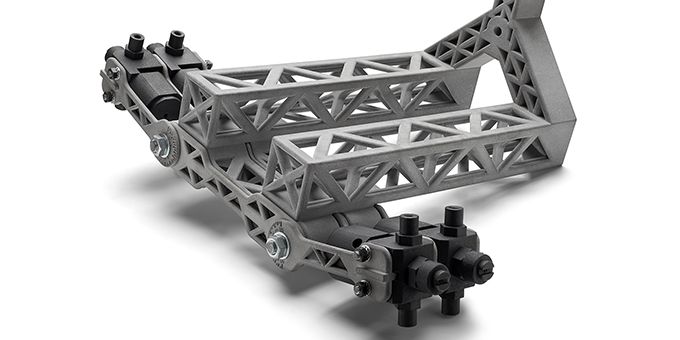
Q&A with Liz Stortstrom, 3D Printing Application Engineer | HP Inc.
Tell us about yourself and your role with HP Inc. and the 3D Printing division.
I currently support HP 3D Printing as an Application Engineer (AE), which essentially means I work with companies to figure out which of their applications are a good fit for HP's Multi Jet Fusion (MJF) 3D Printing Technology. My background is in Mechanical Engineering and I originally joined HP because of my interest in 3D printing. At first, I supported the development of the HP Jet Fusion 500 series (one of HP’s 3D printers), which gave me a lot of in-depth expertise on how the technology and machines work. Now, I leverage that experience in showing others how to best utilize the technology in a cost-effective way. Most recently, my focus has been on industrial applications, including applications for the robotics industry, like end-of-arm tooling (EOAT).
As the use of robotics in production is increasing, we are seeing tremendous growth in the use of 3D Printing for customized parts for end-of-arm tooling (EOAT). How is additive manufacturing helping manufacturers lower costs and speed up turnaround times?
Two of the main benefits of 3D printing are complexity and speed. Meaning, you can generate intricate and complex geometries very quickly. Today, industrial additive manufacturing (AM) technologies are capable of making very robust, repeatable end use parts. So instead of waiting weeks for a machined part or to cut a tool for injection molding, you can now have a functional part in hand within a couple days. This is tremendously valuable not just from a development standpoint, but also in providing your customers with extremely fast turnarounds.
Now, how do you know whether a 3D printed part is really going to be more cost effective than a traditional method? This is where design freedom is important. When converting from a traditional to an additive method, you have much more freedom in terms of part design optimization and size reduction. Usually this results in a much smaller and more efficiently designed part, ultimately saving you weight and cost. Beyond the tool alone, often there’s a trickle-down effect where you can also reduce the size of supporting componentry, motors, or an entire robot arm. Repeat that across an entire production line and you’ll start to realize very significant savings.
What are some of the barriers to implementing additive manufacturing in custom parts production?
Getting started with any new manufacturing method is a big step and the AM space can be especially daunting at first. There are many different technologies that fall under the term ‘3D Printing’, so it can be difficult to know where to even begin. Even folks with experience in one or two technologies might not be aware of the latest developments or benefits today’s industrial level additive options can provide.
There can also be a perception that 3D printed parts won’t be able to meet the strength or repeatability required for an industrial tool. Focus your investigation to industrial level 3D technologies and materials that will be able to satisfy your requirements. Being clear about what your requirements are is critical. During this time, it can be useful to work with a knowledgeable 3D printing service bureau who can help guide you through these decisions before investing in a new technology.
Equally important to awareness is identifying the right applications for the technology and then designing parts for that process. The goal is not to 3D print every single part. Instead, you want to use 3D strategically to augment your current manufacturing plan, applying it when there’s value in reducing time to part or optimizing a design. If used correctly, you should also be able to unlock cost savings and new business opportunities. As an Application Engineer, these are exactly the topics I help companies work through on a daily basis.
How can a manufacturer determine whether purchasing a 3D printer is a better option than outsourcing the work?
Outsourcing is a great option if you are still working through some of those initial questions I mentioned, like what technology and material is best or if you are only printing very low volumes. 3D printing service bureaus are often very knowledgeable, not just of additive technologies, but also a range of manufacturing and finishing processes. They’ll be able to provide some very valuable guidance while you solidify your design, manufacturing plans, and part volumes. However, at some point, it may make sense to bring the technology in house. That tipping point is going to depend on a lot of factors. You’ll ultimately need to calculate an ROI, which is something else an AE can help you with. In that analysis, also consider the added value you can achieve with faster turnaround times or new customization options. For many of our customers, they will bring an MJF system in house with one or two applications in mind and then quickly realize all the additional parts they could be printing. These could be existing parts or the result of new business that additive manufacturing enabled.
Tell us about HP Multi Jet Fusion and the technology behind it.
When HP set out to develop this technology, the aim was to push beyond prototyping and enable repeatable, higher volume additive manufacturing. We can do this by combining a powder bed fusion approach with HP’s Thermal Inkjet (TIJ) technology. Instead of printing ink on a piece of paper, though, we print a fusing agent on thin layers of a powdered polymer then apply energy with an infrared (IR) lamp. Those printed areas will absorb more energy than the surrounding material and fuse together to form a part. This approach effectively fuses between layers, leading to parts with near isotropic strength. Plus, we can reuse the unfused material in the next build at a high rate, resulting in very little waste.
The other benefits relate to speed and complexity. Since no support structures are required, these systems can accommodate very complex designs and that complexity has no effect on time to part. As a result, MJF can support high volumes of robust, intricate parts. To see a visual of the entire workflow on the HP Jet Fusion 5200 Series, check out this video.
Can you share with us any use cases?
The best way to get a feel for what’s possible is to see these parts in action, so I’d highly encourage clicking on the links to see videos for each case. The first I’ll share comes from Gimatic. As a leader in the material handling industry, they regularly have a need to update or customize gripper components. Normally, this would be an expensive and time-consuming process, but by using MJF for their final parts, they can avoid cutting a tool for injection molding. That also enables them to provide customers with parts as quickly as a day after ordering.
There can also be a benefit in converting machined parts. CNC Würfel, an automation specialist, used to CNC machine a gripper adapter that allowed one robot arm to support 3 different grippers. This part was so complex, though, that it took about 8 weeks to make. Since complexity has no impact on production speed for MJF, they were able to easily convert this part over and achieve a 2 day lead time plus 66% in cost savings.
The last example I’ll mention comes from Ficep S3, a high tech engineering company. They set out to re-design an industrial painting machine. The original version was nearly 5 feet wide and very heavy, limiting its speed and precision. After assessing their manufacturing options, they quickly realized the assembly would be too complex for machining and overly expensive with injection molding. So they landed on printing these parts with MJF, resulting in a much lighter assembly that was only 1 foot wide. By optimizing this one tool, they were also able to reduce the size of the supporting motors and gearboxes, saving even more cost across their system.
What design challenges might a manufacturer have to overcome in implementing 3D printing?
First, we have to recognize that the design rules are different. AM unlocks a lot of design freedom but, while there are fewer restrictions than with traditional techniques, this doesn’t mean there are no rules. Each process is different and therefore there are different guidelines and challenges. Some processes may require support structures or may produce anisotropic parts, so you’ll need to really consider part orientation while printing. For MJF, while you don’t have those same concerns, you may still want to design parts for efficient packing in the build volume to optimize part cost, for example. Whatever the technology, it’s best to have a good understanding of how it works and the relevant design recommendations for that specific process.
Next, you’ll want to think beyond just printing and consider the entire workflow. On the front end is software. You may want to explore new features or programs to better enable the complexity of designs 3D printing can support, such as generative design or texturing. On the back end, know what cleaning and finishing processes are going to be used and if those have any design guidelines as well.
3D printing in color, why do you feel this is such an important feature in HP Multi Jet Fusion Technology?
Up until the HP Jet Fusion580 was released, there was no option for 3D printing functional full-color parts. Most color technologies are not capable of creating high strength parts suitable for industrial applications. The key to making this possible is using HP Thermal Inkjet technology to print multiple colored inks at once, just like a regular printer. The main difference is that instead of printing on paper, we’re printing a colored shell around a complex geometry. That allows us to apply a wide range of colors or images to a part while maintaining the strength you can expect from MJF.
The cosmetic benefits from this are clear, but the practical benefits are what I find more interesting. Imagine printing critical information like instructions, part numbers, or safety labels directly onto a part. You can now accelerate time to part even further by eliminating the need for labeling or painting. A great example comes from a systems integrator in France called Seb’Automatisme.
They printed a vacuum EOAT with their logo and color-coded air channels. Now, assembly of this tool is faster and reduces any risk of assembly error since it’s visually clear which air line needs to connect where. Small improvements like this across an entire production line can add up and make a tremendous overall difference in minimizing mistakes and saving time.
Take a look down the road a few years, where do you see 3D printing in manufacturing? Is it a solid part of the industry or still trying to breakthrough? How do you see HP playing a role in its growth?
3D printing has been around for decades, but for a lot of that time it was not ready for the manufacturing space. We’ve now crossed that hurdle. Over the years we’ve seen big improvements in strength, accuracy, reliability, throughput, and cost. I expect we’re going to see those trends continue as the additive industry focuses on enabling higher volume manufacturing. Today, there are already numerous companies around the world leveraging additive manufacturing in some way. Leaders in the automation space are already using additive to enable more agile, flexible, and sustainable production solutions. But there is still a lot of room for growth. As we drive more awareness of technologies like MJF and compelling 3D applications, we’re going to see AM become more widely understood and adopted. As a leader in the industrial 3D printing space, HP is doing its part to help spread that message. At the same time, we are focused on enabling our customers to be as successful as possible with our systems and will continue to push the envelope when it comes to innovative industrial AM solutions.
.jpeg)
Liz Stortstrom is a 3D Printing Application Engineer (AE) with expertise in using HP's Multi Jet Fusion (MJF) Technology for industrial applications. She has a background in Mechanical Design and joined HP to support the development of the MJF technology. She now utilizes that experience to help people take their businesses to the next level with additive manufacturing. Liz received her BS & MS in Mechanical Engineering from Carnegie Mellon University and currently resides in Portland, OR.
The content & opinions in this article are the author’s and do not necessarily represent the views of RoboticsTomorrow
Comments (0)
This post does not have any comments. Be the first to leave a comment below.
Featured Product
