Designed, manufactured and installed by E80 Group, this distribution facility is not only an example of excellence in integrated robotics systems, but also a showpiece for energy and environmental efficiency.
2022 Top Article - World's Largest Pasta Production Plant a Showcase for Integrated Robotics and Sustainable Distribution
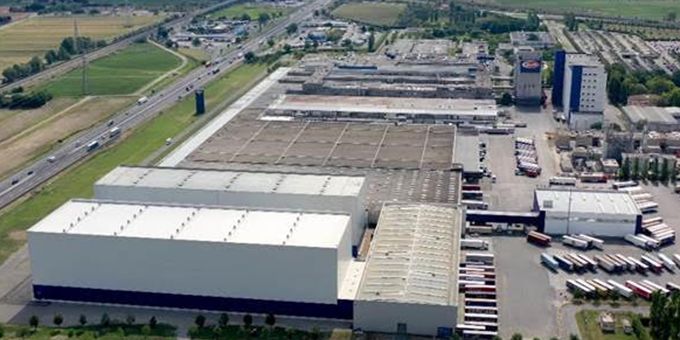
Case Study from | Jim McMahon for E80 Group
Barilla's flagship pasta manufacturing plant in Parma, Italy boasts a 430,000 square foot distribution facility – fully automated, lights-out, 24/7/365 operation – equipped with120 laser-guided vehicles, 37 robotic systems including high-density AS/RS, palletizers, labelers and stretch wrappers, handling 320,000 tons of pasta annually. Designed, manufactured and installed by E80 Group, this distribution facility is not only an example of excellence in integrated robotics systems, but also a showpiece for energy and environmental efficiency.
"Barilla has always been committed to environmental and social sustainability. A sustainable food supply chain can be achieved only by looking at the entire supply chain in its overall dimension and its integration between the individual steps. An integrated factory, therefore, has a meaning that goes beyond the efficiency of the factory, but it is rather a fundamental element to make the supply chain more sustainable." …Mr. Alessandro Spadini, Plant Director, Barilla headquarters and production facility in Parma, Italy – the world's largest pasta production facility.
Legacy of Innovation
Family owned since 1877, Barilla is the world's leading pasta maker, with 45 percent of the Italian pasta market and 35 percent of the U.S. market. The company produces pasta in more than 160 shapes and sizes, and sold in over 100 countries. In addition to pasta, Barilla owns 16 brands making the company the leading manufacturer of sauces in Europe, of bread in France, of crispbread in Scandinavia and central Europe, and of bakery products in Italy. Barilla's 29 production sites – 15 in Italy and 14 additional worldwide – had annual 2019 sales exceeding $4.3 billion (USD).
Although steeped in history, Barilla has yet been on the cutting edge of technology. Embracing the connected food movement, the Italian pasta maker is using the Industrial Internet of Things (IIoT) and analytics to provide traceability in its supply chain and transparency to consumers.
Its field-to-fork initiative tracks all stages of Barilla's food production – from local food harvesting to storage, processing, packaging, distribution and ultimately, consumption. This supports initiatives of the U.S. Food and Drug Administration’s Food Safety Modernization Act emphasizing food track and trace, quality and safety. Supporting this, Barilla, in partnership with Cisco, created a prototype of a digital passport that takes the consumer on a journey – using a smartphone to scan a QR code on the back of Barilla pasta box or tomato sauce jar – from where that specific product was grown to how it was processed and, ultimately, arrived on the store shelf.
An early adopter of sustainability practices, for Barilla this means improving the efficiency of production processes to reduce greenhouse gas emissions, energy usage and water consumption. Sixty-eight percent of electricity used in Barilla plants comes from renewable sources. Since 2010, Barilla facilities have reduced water consumption by 21 percent, and reduced greenhouse gas emissions by 30 percent.
Outside of the company's manufacturing facilities, promoting more sustainable agricultural and farming practices for all Barilla companies' strategic supply chains is a critical focus of its sustainability initiatives. Three thousand farming companies worldwide are involved in sustainable agriculture projects with Barilla. The company utilizes only recyclable packaging materials from responsibly managed forests, and continually minimizes the quantity of packaging and distribution materials used.
Ninety-three percent of Barilla's production volumes are manufactured in ISO14001 certified production plants. ISO 14001 is the international standard that specifies requirements for an effective environmental management system. It provides a framework that an organization can follow, rather than establishing environmental performance requirements.
In 2018, Barilla announced its plans to invest one billion euros over five years into its industrial assets, aimed at boosting sustainability by improving processes and technologies, and supporting innovation and geographic expansion. A pivotal focus of this plan was transforming the distribution operations of its flagship pasta production facility in Parma, Italy into a showcase of Industry 4.0 operation of integrated robotic processes and energy sustainability.
Robotics-Integrated Distribution
Initially starting as a bakery shop 143 years ago in Parma, Italy, the location has remained the center of Barilla's corporate headquarters since, as well as home to the company's largest pasta production and distribution facility.
This flagship plant, which is also the largest pasta manufacturing operation in the world, incorporates a newly upgraded distribution facility, a model of state-of-the art robotics, machine-to-machine communication and the Industrial Internet-of-things, integrated for optimized automation and streamlined throughput.
The distribution facility is not only an example of excellence in integrated robotics systems, but also for energy and environmental efficiency.
"The implementation of highly-automated flexible systems enables us to be absolutely suitable to the needs and the uses of the distribution facility, and this obviously implies a lower energy consumption," said Mr. Spadini. "This is accented by the adoption of components that are significantly more efficient in terms of energy consumption and environmental impact, compared to our past systems. An essential part of this distribution project is, having considered an overall and systemic integration of the project and not just single, discrete systems."
"Any distribution system that is not sufficiently flexible, that is based on a rigid scheme, sooner or later, will become an issue," added Mr. Spadini. "The solution in trying to separate the various distribution processes – like high-density storage, transport of pallets, palletizing, stretch wrapping and staging pallets at loading docks for shipping – comes from these processes ideally having flexible, adaptable solutions. Because the throughput flows and peaks that arise from just-in-time ordering and market shifts can only be managed optimally with distribution flexible solutions."
To realize such an integrated-system and energy-efficient strategy at Barilla's Parma distribution facility, E80 Group (E80) was selected to design, manufacture and install a solution. E80 is an Italian-based multinational leader specializing in creating automated solutions for companies that produce fast-moving consumer goods, particularly in the food, beverage and tissue sectors. It has been a leading manufacturer of integrated-robotics systems for distribution facilities for almost three decades, specifically laser-guided vehicles (LGVs), robotic palletizers and other end-of-line robotic systems. The company's latest technology advances have made LGVs particularly attractive for sustainability and reduced energy usage.
E80 started with planning and distribution model simulations for the Parma facility in 2013, and continued with upgrades and expansions through to 2020. Barilla’s Parma distribution facility handles approximately 1000 different packaged SKUs within its product line, divided into dry and fresh product categories.
The 430,000 square foot distribution facility is a fully automated, lights-out, 24/7/365 operation, equipped with 120 laser-guided vehicles, and 35 robotic systems including high-density AS/RS, palletizers, labelers and stretch wrappers. Combined, in 2019, these systems handled 438,000 tons of pasta.
"A considerable challenge has been keeping production going at Parma, the world's largest pasta plant, while creating a complete distribution renovation," said Mr. Vittorio Cavirani, Vice president at E80. "This has been achieved through great synergy and cooperation between Barilla and E80, but also because the integrated robotic systems are flexible and adaptable as changing throughput and needs have required."
Laser-Guided Vehicles
"One of the main reasons that made us decide to move forward with this renovation for Parma's distribution was the desire to get away from conveyors and adopt laser-guided vehicles for pallet transport within the facility," added Mr. Spadini. "Traditional conveying systems are sized for production peaks, and not flexible enough to manage variations in throughput, in terms of both flows and volume. Therefore, pallet conveyor systems are typically highly inefficient."
Barilla’s Parma, Italy plant has120 LGVs in operation. (Image courtesy E80 Group)
Three main types of LGVs, manufactured by E80, are in use at Parma: Those that carry a single pallet; those that carry 2 pallets at a time; and LGVs that carry 4 pallets at a time. A total of 120 LGVs are in operation.
The LGVs interact with floor-positioned pallets and AS/RS induction stations, and picking up and dropping off pallets between receiving from manufacturing, palletizing, stretch wrapping, labeling, finished-goods warehousing, and staging locations for shipping. The LGVs have roller beds that support the pallets, which allow efficient roll-on/roll-off procedure.
The LGV roller beds allow efficient roll-on/roll-off procedure. (Image courtesy E80 Group)
"An increasing number of manufacturers require 24-hour operation at continuous throughput," said Mr. Enrico Grassi, E80 President. "Parma's LGVs have been designed to efficiently meet and exceed these requirements. The most recent automation developments in laser-guided vehicles for pallet movement enable warehouse operators and plant production supervisors to optimize for system flexibility, modularity and scalability."
LGV Navigation
The LGV's laser navigation is based on target triangulation to keep the vehicles on course. Each LGV is equipped with a rotating laser which scans 360 degrees around the vehicle for laser targets mounted on columns, walls and stationary machinery. The reflections from these targets are measured relative to angles from the vehicle, and triangulated to allow the vehicle to determine its position. This position is compared to a CAD-type map stored in the LGV’s memory.
The system uses positive-positioning feedback in real time, computing algorithms hundreds of times per second. The steering is adjusted accordingly to keep the LGVs on track. It can then navigate to a desired target using the constantly updating position. This laser navigation can obtain tracking accuracy of about 0.39 inch on these LGVs.
Vision navigation is under review for use on the Parma's LGVs. Vision navigation uses cameras or lidars onboard the LGV to detect each vehicle's surroundings and understand its position.
The Latest Lithium Flash Battery® Technology
Introduced for use with LGVs by E80, lithium Flash Battery technology, developed by Flash Battery Srl, provides a higher level of performance than other batteries for industrial vehicles. Flash Battery technology uses the latest in lithium iron phosphate (LiFePO4) chemistry, which delivers low toxicity, well-defined performance and long-term stability. Having a very constant discharge voltage, Flash Battery technology allows the battery to deliver virtually full power until it is discharged.
The cells in a lithium battery have different capacities, resistances and self-discharging potential. When one cell is 100 percent charged, another may be 95 percent charged. This difference seems small, but it can increase with each charge cycle until it becomes quite large, which lowers the battery's charge potential and range of the vehicle. To prevent loss of charge and reduce balancing and charging cycle time, Flash Battery electronics act in active and passive modes to equalize the cells' charge levels during charging and discharging. This results in 20-times faster balancing, a maximum of 30 minutes in cyclic applications, greatly reducing charge balancing and recharge times.
Parma’s LGVs employ lithium Flash Battery technology. (Image courtesy E80 Group)
Supporting the performance of Barilla's fleet of LGVs and its Flash Battery technology, E80's Flash Data Center continually monitors and controls every battery of Barilla's integrated system to ensure the LGV network maintains its battery potential in peak performance to maintain plant uptime and efficiency.
"The control electronics in the lithium Flash Battery keep it balanced and efficient, eliminating the need for regular maintenance," said Mr. Cavirani. "It is also equipped with a remote monitoring system that enables the condition of the battery to be determined at any time, while reporting any malfunctions."
Lithium Flash Battery technology eliminates problems connected with lead-acid batteries, including high maintenance costs, low efficiency below 75 percent, short battery life, inability to partially charge, and the cost of charging salts and exhaust vacuum systems. A single lithium Flash Battery is required per LGV, compared to two batteries needed with traditional lead-acid LGV applications.
Integrated System Controls
"Controls systems are fundamental for managing traffic inside Parma's distribution facility," added Mr. Grassi. "It is fundamental because these are mobile robots, and what enables them to be efficient is the SM.I.LE80 controls system, the management and the controls that make sure that these robots are in the right place at the right time. E80 does not just manufacture robots, but rather integrated factories that use machines and robots that are governed by the controls. All of this is meant to achieve efficiency and reductions of costs in carrying out organized activities, and that is what we have achieved at Parma."
Running the LGVs, as well as all integrated robotics systems within the Parma distribution facility is E80's Smart Integrated Logistics (SM.I.LE80®) controls platform.
SM.I.LE80 continually updates the positional status of each LGV regarding such factors as whether it is loaded or unloaded, emergency stopped or soft stopped, operating in manual mode, and battery level. A simulation module simulates the LGVs in the system. An HMI graphical interface gives the operator a graphical overview of the LGV locations in the system and monitors each in real-time.
The SM.I.LE80 controls ensure the integrated and automated management of systems, communicating with AS/RS, palletizers, wrappers and shipping staging locations. The entire LGV logistics flow within the Parma distribution operation can be centrally managed from this logistics platform that ensures the efficient integration and optimization with all operations. The controls system also guarantees total product traceability and safety throughout the operational environment of the LGVs.
Operational flexibility is a key factor, not just in its capability to direct and manage the fleet of LGVs, but also in its expandability. Any number of automated guided vehicles can be added to the network at any time the facility's production and distribution needs require.
High-Density Automated Pallet Storage
Barilla's high-density automated warehouse is designed to meet the Parma plant's production needs, and perfectly integrated with its LGV technology. Six stacker cranes support 47,000 pallet locations.
The high-density warehouse uses E80's AS/RS Crane Store® systems of stacker cranes equipped with automatic product handling devices for double-depth storage. Because they can operate at heights of up to 130 feet, these systems dramatically increase warehousing capacity. The AS/RS technology also minimizes energy usage and maintenance requirements. An additional 50,000 pallet locations are utilized for LGV drive-in high-density low-bay storage.
Six stacker cranes support 47,000 pallet locations. (Image courtesy E80 Group)
Pallet-Free Robotic Palletizing
"Removing wood pallets was an innovative choice, at least for Barilla, and it came from an overall vision, an integrated vision of our supply chain," said Mr. Spadini. "First of all, removing wood from production and many distribution areas means removing an element that may pollute the environment where we produce and package our products. But also, managing pallets without wood parts opens up the opportunity of handling and reprocessing of pallets in a completely automated way, improving efficiency and minimizing environmental impact."
Eliminating wood pallets is only part of the unique palletizing process at Parma. Robotic palletizing stations form cases in palletized configurations directly on the palletizers' platform, then these are moved onto LGVs and transported to other end-of-line process stations in the facility where a pallet is inserted underneath prior to storage and shipping.
Palletless Robotic Palletizing. (Image courtesy E80 Group)
E80 designed and manufactured an automated pallet management system for the Parma facility, which controls the large volume of pallets within a small footprint. It also ensures that only pallets complying with Barilla's requirements are used in storage and shipping. It guarantees high accessibility, maintainability and availability without the need of operator interaction.
Integrated Robotic Stretch Wrapping and Labeling
As with the other systems at play in Parma's distribution operations, its end-of-line stretch wrapping and labeling are also robotic and fully integrated with its LGVs and other robotic processes.
The high production speed stretch wrappers employ automatic wrapping head changeovers, eliminating the need to stop production.
"We can manage not only very accurately the use of our stretch wrap film, but we have also reduced film usage by almost 30 percent, compared to our prior stretch wrappers," explained Mr. Spadini.
Parma's robotized labelers are equipped with anthropomorphic robots that allow the application of labels on multiple sides and levels, guaranteeing production flexibility.
Robotic stretch wrapping. (Image courtesy E80 Group)
The applicator arm is equipped with a camera to check the correct application of labels and the barcode readability. Two printers make it possible to double the operating range and carry out reel changeovers without production downtimes.
Traceability
Parma's control and identification of each case of products throughout the distribution facility is managed by the SM.I.LE80 controls system. Once cases and pallets leave the facility, the labeled identification provides a tracking mechanism for complete track-and-trace throughout the supply chain.
"For Barilla, traceability means providing the right information, correct information and timely information on all our products from the moment we received the lots of raw materials, to the moment we actually distribute and display our products on shelves," continued Mr. Spadini. "Full traceability, for us, is one of the main elements to ensure and guarantee our consumers the right to nutritionally safe products and also controlled products."
Synergy and Cooperation
E80's dream from the beginning was that of integrating factory production processes with distribution and shipping, making all the process movements function smoothly, correctly and efficiently as a fully-integrated operation. Barilla's integrated distribution facility at Parma has delivered this and a very positive impact on sustainability.
"Parma is a very large, and a very important production and distribution plant for Barilla, in terms of efficiency and effectiveness," explained Mr. Spadini. "Key to maintaining its ongoing performance is the 24/7 cloud-based predictive maintenance which is monitored remotely by E80. But underlying this is a strong cooperation, a partnership between Barilla and E80, which has enabled us to reach a high level of management of the plant and achieve our postulated goal."
About Barilla Group
Barilla is a family company, not listed on the stock exchange, chaired by brothers Guido, Luca and Paolo Barilla. It was founded by their great-grandfather, Pietro Barilla, who opened a bakery in Parma in 1877. Now, Barilla is famous in Italy and throughout the world for the excellence of its food products. With its brands – Barilla, Mulino Bianco, Pan di Stelle, Gran Cereale, Harrys, Pavesi, Wasa, Filiz, Yemina and Vesta, Misko, Voiello and Cucina Barilla – it promotes a tasty, joyful and healthy diet, inspired by the Mediterranean Diet and the Italian lifestyle.
When Pietro opened his store more than 140 years ago, his overriding aim was to make good food. Today, that principle has become Barilla's way of doing business: "Good for You, Good for the Planet," a slogan that expresses the daily commitment of the more than 8,000 people who work for the company, and of a supply chain that shares its values and passion for quality. "Good for You" means constantly improving the product offering, encouraging the adoption of healthy lifestyles and facilitating people's access to food. "Good for the Planet" means promoting sustainable supply chains and reducing CO2 emissions and water consumption.
About E80 Group
E80 Group specializes in the development of automated logistics solutions for consumer goods manufacturers in the beverage, food and tissue sectors, and other diversified areas. Its automation solutions improve profitability and efficiency by streamlining product movement from receipt of raw materials through production, warehousing and shipping.
E80 Group's main systems include palletizing robots, a wide range of laser guided vehicles, high-speed robotic stretch wrappers, pallet control systems, robotic labelers, layer picking and repacking solutions, automated storage and retrieval (AS/RS) high-density warehouses, and compact end-of-line solutions. The entire logistics flow can be centrally managed from E80 Group's proprietary smart, integrated-logistics software platform – SM.I.LE80® – that ensures the efficient integration and optimization of all operations.
The content & opinions in this article are the author’s and do not necessarily represent the views of RoboticsTomorrow
Comments (0)
This post does not have any comments. Be the first to leave a comment below.
Featured Product
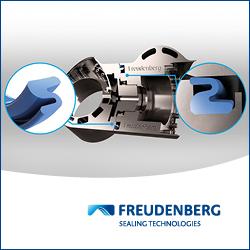