Have you experienced a series of spindle failures, causing you to wonder why? Maybe you’re a Quality Control engineer looking for reasons your cuts are going out of tolerance.
The Most Common Causes of Spindle Failure
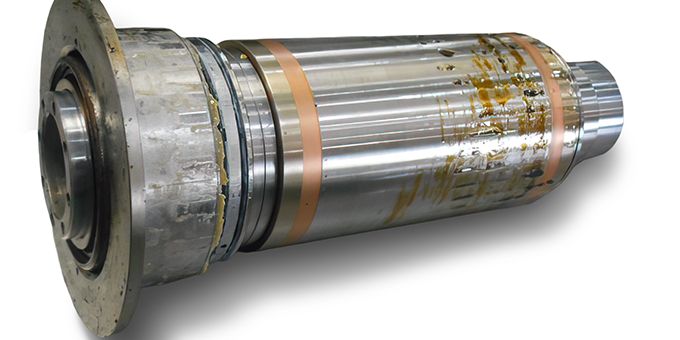
Article from | Precision Drive Systems
Have you experienced a series of spindle failures, causing you to wonder why? Maybe you’re a Quality Control engineer looking for reasons your cuts are going out of tolerance. Or, perhaps you’re looking for information that would help you design a preventative maintenance program for your CNC machine or robotic material removal system. If any of these are true, you’re in the right place.
Here, then, are the top causes of spindle failure.
1. Crashes
The most common cause of spindle failure is, by far, crashes. Many articles don’t talk about this, perhaps because it’s embarrassing. Naturally, no one wants to report a crash. However, the fact that crashes occur so often underscores the importance of training. Given how expensive CNC machines are, how much downtime costs, and the cost and time involved in spindle repairs, it pays to invest in training your people. Proper procedures and rigorous training can avoid mistakes in programming and operator error.
2. Pushing Machines Too Fast or Too Hard
It is tempting to speed up a process to make production goals. And many times, there are ways a process can be performed in less time. But spindle failure is bound to occur when the machine feed rate is too fast for the rating of the spindle in a given type of material. Consulting the manufacturer or a spindle expert can save you a lot of trouble and downtime.
We also often see failure caused by operating a spindle at an rpm that is too high for the size of the cutter. As the diameter and length of the cutting tool plus tool holder increase, the operating speed must decrease. Consult your documentation for details.
On the metalworking side, people often direct coolant spray directly at the spindle nose to get it as close to the cutting tool as possible so they can ramp up the feed rate. Over time, the coolant penetrates the spindle sealing system, floods the bearing, and shorts the stator. Take it apart, and you find the whole spindle is full of water.
3. Worn or Improper Tooling
Sometimes a company will overlook the condition of the tool in a machining operation. Using worn tooling or the wrong tool for the job can cause spindle failure. Don’t let Inexpensive and replaceable components like cutting tools and collets cost you dearly.
4. Improper Warm-Up Procedure
High-precision spindles are designed to consider the effect of the thermal expansion of their parts. Failure to follow the manufacturer’s recommendations to bring the machine up to operating temperature means the relevant components do not expand to their intended size. The consequent looseness can cause chatter marks in your workpiece and shorten the life of the spindle.
Note that a proper warm-up procedure depends on the ambient environment. A hot, moist climate will need different warm-up characteristics than a cool, dry one.
5. Improper Cool-Down Procedure
Cooling a CNC or robotic material removal machine down too quickly can cause internal condensation. The lubricant will protect against rust. But the mixture of water with the lubricant over time makes it more like sludge. That sludge can interfere with the retention force of the springs holding the tool. Insufficient retention force gives rise to quality control problems and shortens spindle life.
6. Contamination of Air or Coolant Supply
Moisture or other contaminants in the air compressor that supplies the pneumatic actuator is quite common. Regular inspection and replacement of the air filters are crucial to the proper functioning of your spindle. You may need to invest in a dryer for the air supply in moist climates.
Unfiltered or poorly filtered spindle coolant can cause failure. If the supply to the stator water jacket becomes clogged, the stator will overheat and burn out. Similarly, contaminated spindle coolant, common in metalworking, can plug up the hole through the center of the shaft/drawbar and flood the spindle.
While it is tempting to save money on consumables like filters, replacing or repairing your spindle costs a lot more. It is good advice to use the best quality filters you can. You’ll save in the long run by prolonging the life of your spindle.
7. Plunging into Material rather than Ramping In
This is usually caused by programming errors or a misguided attempt to speed things up. The too-rapid plunge causes the front bearing pair to fail.
8. Tool Sticking in Taper
A sticking tool is usually due to the transfer of heat caused by an oversized tool. It can also be caused by an improper ejection stroke of the drawbar. That can happen when there is contamination in the actuator or broken springs in the drawbar assembly.
9. Tool Slipping in Taper
A slipping tool is often caused by the transfer of heat from long heavy cuts that warp or distort the tool taper. It can also be due to an improper ejection stroke of the drawbar. In that case, like the sticking tool problem, contamination in the pneumatic actuator or broken springs in the drawbar assembly can be the culprit.
10. Shorted Winding
If there is a mismatch between the variable frequency drive and the electrical characteristics of the spindle, a shorted winding can result.
11. Actuation While Running
Spindle failure occurs when the pneumatic actuator’s piston contacts the drawbar while the spindle is still rotating. This can be caused by operator or programming errors. A malfunction of the proximity sensors that read the position of the drawbar – or a defect in the sensor or relay that senses shaft motion – can also cause this mode of failure.
Yet another possibility is the contamination of the pneumatic actuator or the exhaust muffler of the actuator. One of the most common culprits, in this case, is a faulty or leaking solenoid valve that allows air to go to the pneumatic actuator when it is not required.
Most modern spindles are sealed, with lubrication designed to last for the useful life of the spindle. So, lack of lubrication, or improper lubrication, are not common causes of failure.
How long should your spindle function? Manufacturers don’t like to put numbers on spindle life expectancy because so many factors can shorten it. Environmental factors play a crucial role. One example is air quality, and another is vibration coming from a nearby machine. However, experts with many years of experience estimate the average spindle life expectancy at between 5000 and 7000 operating hours. That said, some operations regularly get half that, and others get double.
The content & opinions in this article are the author’s and do not necessarily represent the views of RoboticsTomorrow
Comments (0)
This post does not have any comments. Be the first to leave a comment below.
Featured Product
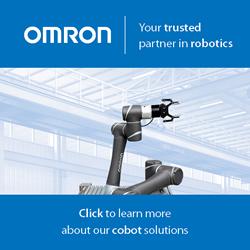