These systems can be configured and supplied as individual components or as complete integrated motion systems with custom interfaces, cable management solutions, vacuum feedthroughs and application-optimized integrated granite and aluminum structures.
Comparing XY-Theta Motion / Positioning Stage Options for Precision Automation Applications
Article from | PI
High accuracy 3-axis XY-Theta stages (XYT assemblies) are critical in many test and production processes related to laser precision machining, semiconductor and photonics test and production, and medical device manufacturing. PI offers a broad and deep solution set for integrated XY-Theta Motion Systems with Industrial Motion Controllers. These systems can be configured and supplied as individual components or as complete integrated motion systems with custom interfaces, cable management solutions, vacuum feedthroughs and application-optimized integrated granite and aluminum structures.
XY-Theta Precision Motion and Positioning Assemblies based on Air Bearing Stages
An ultra-high performance, granite based XY-Theta stage assembly based on an A-322 planar air bearing XY stage with an air bearing rotary table.
Compact, air bearing-based low profile XY-theta stage assembly. See the A-311 XY-air bearing stage in motion
The engineering teams at PI have extensive expertise and experience with air bearing technology and multi-axis motion stage systems. The ultra-precision performance of engineered air bearing positioning systems along with their non-wearing nature make them ideal solutions for semiconductor applications involving combined linear and rotational motion.
Custom XY-Theta stage based on the A-311 Long Travel XY Air Bearing Stage, and A-621 Rotary Stage for 360° Theta-Z Rotation
In the image above, a custom, low profile A-311 Air Bearing Planar XY Motion Table is combined with a high-precision A-621 Series Air Bearing Rotation Stage into a precision XYT assembly.
When more degrees of freedom are required, XY-stages can be combined with a low-profile Z-Tip-Tilt (ZTT) motion module to form 5-axis systems such as the 5-DOF wafer stage for semiconductor metrology applications, shown in the video below. The ZTT module can also be added to XY-Theta stages for 6DOF motion applications.
EtherCat®-Based Industrial Motion Controllers
PI XY-Theta 3-axis stage assemblies make use of ACS Industrial Motion Control components. PI controllers based on ACS use optimized configurations for best applications performance. This includes pre-configured systems with optimized system parameter information ready for out-of-the box operation-including motion synchronized device triggering through Laser Control Module (LCM) / Laser Control Interface (LCI) hardware as well as functional safety features like Safe Torque Off.
The ACS laser control module
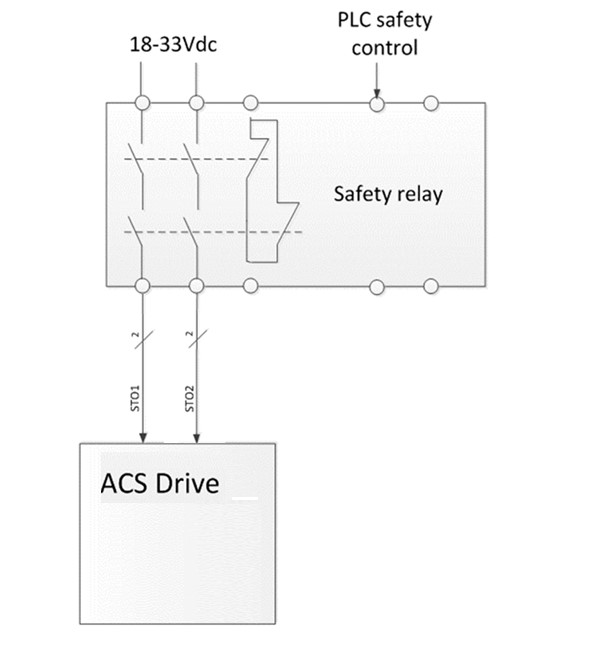
PL e / SIL 3 certified Safe Torque Off (STO) functionality provides machine builders a simple and cost-effective way to implement machine safety. STO is available in select PI motion controllers.
XYT Precision Motion and Positioning Assemblies based on Mechanical Bearing Stages
In many applications, compactness is critical for tool integration. The V-508 low profile linear stage / V-610 low profile rotary stage direct-drive, multi-axis motion system, is one example of a lightweight, high-performance 3-axis assembly that is extremely low profile, highly compact, and also technologically flexible to optimally address both rapid step and settle as well as smooth coordinated scanning applications with error tolerances ranging from nanometers to microns.
XY-Theta stage assembly with clear aperture for light path, providing 25x80mm travel. The assembly consists of two V-508 compact linear translation stages and a V-610 direct-drive rotary stage.
High-throughput industrial automation applications of precision motion typically involve repetitive moves with higher loads and accelerations. Here, the V-817 Series Precision Automation Stage Assembly with a direct drive rotary table, shown above, provides high acceleration and high duty cycle motion with efficient 3-phase linear motors and torque motors offering high continuous and peak force. Stiff stage construction and design using aircraft grade aluminum alloys provide stiffness to handle high impulse over short time durations with suitable precision. Precision truck and rail bearings are implemented for both load characteristics and long operating lifetimes. The integrated high-speed direct drive rotary stage with high torque output is used for dynamic step-settle and scanning performance.
PI XY-Theta automation systems are scaled specific to the application using travel, performance, load, and space criteria. The solutions shown here are a small cross-section of available options to address XYT motion and show the diverse array of motor, bearing, encoder, and design elements that have contributed to making PI the market leader in precision motion.
High-load, high speed direct drive 3-axis XY-Theta automation stage assembly. More information on the V-817 linear translation stage family and its motion controllers
Low profile V-508/V-610 based XYT stage assembly. The scanning performance of a V-508 XY stage is shown in a video here.
XYT Stage Assembly Questions – Get Support from an Engineer
The XY-Theta stage solutions shown in this article represent a diverse array of proprietary technologies developed in-house at PI, including motors, encoders, bearings as well as materials and design. PI is a global leader in multi-axis precision motion control, pioneering high precision linear stages, rotary stages and multi-axis stages for numerous high technology applications. We have been continuously improving our high precision XY-Theta multi-axis motion systems and have helped many customers in semiconductor manufacturing, laser materials processing, and medical device manufacturing achieve higher throughput and quality.
The content & opinions in this article are the author’s and do not necessarily represent the views of RoboticsTomorrow
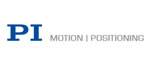
PI USA (Physik Instrumente)
PI is a privately held company that designs and manufactures world-class precision motion and automation systems including air bearings, hexapods and piezo drives at locations in North America, Europe, and Asia. The company was founded 5 decades ago and today employs more than 1700 people worldwide. PI's customers are leaders in high-tech industries and research institutes in fields such as photonics, life-sciences, semiconductors and aerospace.
Other Articles
High-Throughput PIC Production Needs Precision Alignment Equipment for Photonics Arrays, Fibers, Lenses
Fast Hexapod Improves Aircraft Manufacturing Process
Fiber Alignment and Photonic Chip Test & Assembly Just Got Easier
More about PI USA (Physik Instrumente)
Comments (0)
This post does not have any comments. Be the first to leave a comment below.
Featured Product
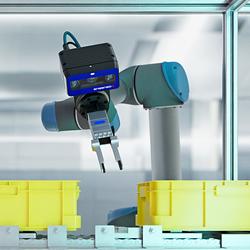