Regardless of the palletizing method, the goal of any supply chain operation is to ship out the most product possible. This can only be done by making the best use of the space on each individual pallet, even if it means just one more package per pallet.
3D Time-of-Flight Camera Aids Robotic Palletizers
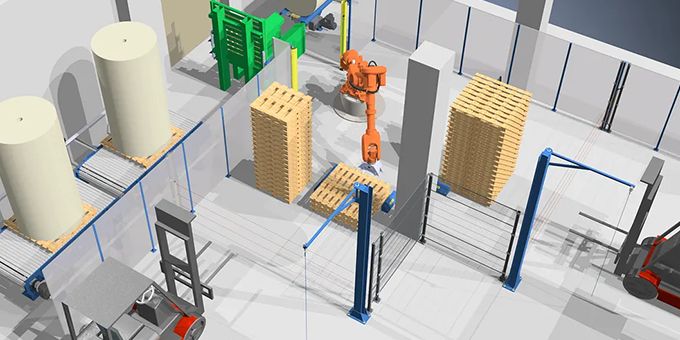
Case Study from | LUCID Vision Labs
Loading or unloading pallets efficiently with the help of robots requires an automated system to carry diverse loads of pallets with diverse shapes and sizes to be handled with precision and care at fast cycle times. Layers of the pallets are not guaranteed to be flat, may contain bulky objects or may arrive slanted, putting the layers on the pallet at a slope. Regardless of the palletizing method, the goal of any supply chain operation is to ship out the most product possible. This can only be done by making the best use of the space on each individual pallet, even if it means just one more package per pallet.
Germany-based companies MSB Düren and codesolo GmbH use a conveyor system where the pallets need to be placed in a structured and precise manner with the help of a robot. For this purpose, a robot operates several pallet towers. Each tower consists of different types of pallets. When a new pallet tower has been delivered by the forklift, LUCID’s Helios2 Time-of-Flight camera which is mounted on the robot head detects the new pallet tower and measures the dimensions of the pallets to determine the specific type from 20 different pallet formats.
Challenge
In the past, similar palletizing systems were implemented with LiDAR line scanners, however this was severely limited at the achievable speed. A new solution using Time-of-Flight cameras proved to be the best method due to its accuracy, resolution and SDK at an attractive price. One of the challenges with the ToF solution was to overcome the handling of more than 20 different types of pallets which sometimes only differ slightly in dimensions. In addition, sometimes the pallets are not manufactured very precisely or are minimally damaged. Various logic links have been implemented for this purpose, for example, if the primary measured values were not sufficient for a clear identification, then additional determined properties are used until there is a clear match. Another challenge to be addressed was due to the material of the pallets – some of the pallet types were covered with a semi-transparent plastic film. This sometimes led to measurement errors or “ghost data” in the 3D measurement values of the ToF cameras same as with LiDAR systems. However, by combining the 3D measurement value images and the intensity images provided simultaneously by the Helios2, robust reliability could be achieved in conjunction with the logic links.
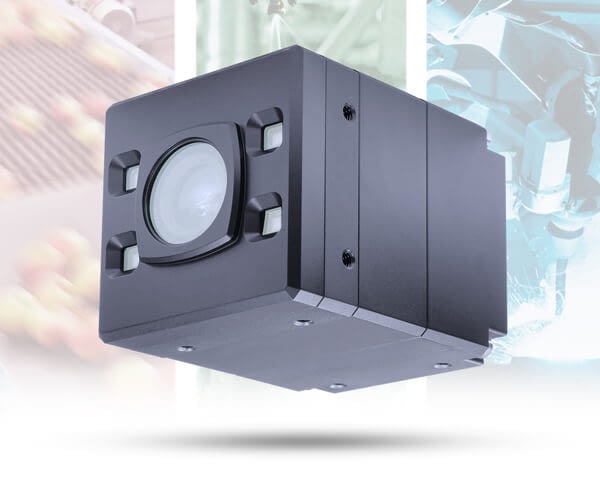
While LiDAR line scanners are limited for palletizing systems, the Helios2 3D Time-of-Flight camera achieves the desired speed and provides accuracy, high resolution, and IP67 protection for robust reliability.
Solution
Each time a new pallet is requested, the Helios2 ToF camera measures the exact position of the top pallet of a selected tower so that the robot can precisely lift this pallet off the tower. This works even if individual pallets deviate from an ideal typical positioning. The Helios2 ToF camera is integrated in the center of the gripper structure, which is located on the head of a robot. The camera is connected with a single cable thanks to Power over Ethernet (PoE) to an IPC running the analysis software. The IPC communicates with the robot and a Siemens PLC via a second LAN connection. The Helios2 is used partly in streaming and partly in single image mode. In this mode, up to 32 images are recorded by the camera and the average image calculated is sent to the IPC.
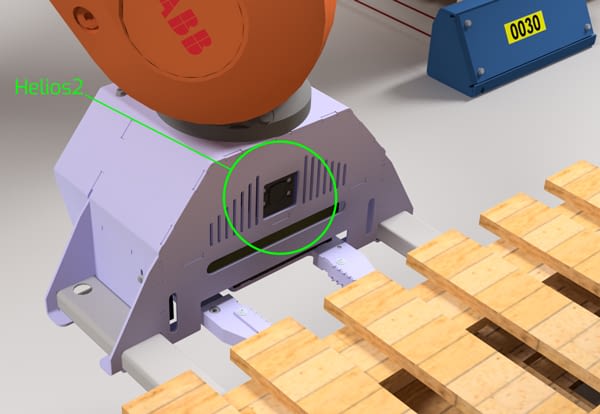
Helios2 ToF camera located in the gripper structure on the head of the palletizing robot.
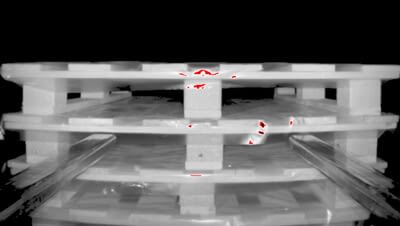
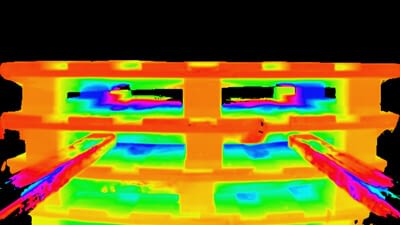
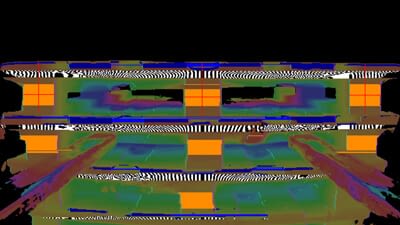
By combining 3D measurement values and intensity images, more than 20 types of pallets can be identified and measured, including pallets covered in semi-transparent, or reflective materials.
Conclusion
Previously, the pallets were placed in the set-up device by hand in a 5-shift operation. This work was unreasonable, also because some of the pallets are very heavy. By implementing an automated palletizing process and using Time-of-Flight cameras, now the preparation of the pallet towers is done in a normal shift and manual interaction is minimized. In addition, a cost reduction and faster cycle times could be achieved. After comparative tests, the Helios2 Time-of-Flight camera proved to be the best solution to load and unload pallets efficiently. Most important were accuracy, resolution and the SDK, at an attractive price.
The content & opinions in this article are the author’s and do not necessarily represent the views of RoboticsTomorrow
Comments (0)
This post does not have any comments. Be the first to leave a comment below.
Featured Product
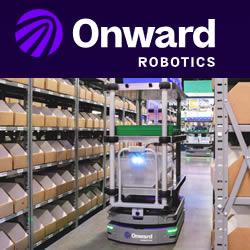