Virtual Testing Helps Precision Gear Start-up Increase Understanding of Design Performance and Reduce Costly and Time‑intensive Physical Prototyping
Designing High-ratio Drives for Precision Applications
Case Study from | MOTUS LABS
When Motus Labs first started operations in 2018, their process relied heavily on physical testing. Carlos Hoefken (CTO) comments: “In our early start-up days, we were designing new products and going straight to building and testing physical prototypes – we weren’t using any simulation to prototype different scenarios in the design phase. This was very costly and the whole process was just taking too long. We were under a lot of pressure to deliver a quality offering, and it was clear that we had to move more of our testing to the virtual realm so we could iterate faster and ultimately speed up our development cycles, reduce impact on resources (people, materials, cost), and increase confidence that our designs would work first time. To do this, we needed instant access to an engineering team who could help us bridge the gap between concept and product without the time and expense of physical iterations.”
When Motus Labs first got in touch with Hexagon, Motus Labs only had a handful of employees and, as with all start-ups, resources were extremely tight. Robert James (VP, Product) comments: “We wanted to see what simulation could do for us and Hexagon opened our eyes to significant possibilities for improvement using a range of tools across their portfolio. We started by exploring how Adams could help refine our drive system development process. The problem was, none of us had used Adams before, and we simply didn’t have the time to learn the software and do the work. So, alongside introducing us to their software portfolio, Hexagon supported us with expert-level consultancy – they provided their time and expertise, and they showed us the value that Adams could bring.”
Hexagon provided support on one specific design project, during which they helped Motus Labs to achieve their requirements for this application whilst also demonstrating a robust, repeatable, efficient design process which Motus Labs could themselves follow for future projects.
DESIGNING HIGH-RATIO DRIVES FOR PRECISION APPLICATIONS
For the project which Hexagon supported, Motus Labs was looking to design a very high ratio robotic gear drive (close to 100:1 rotation). Due to the precision environment in which these drives would be used, they had to be well controlled, accurate and stiff, exhibiting minimal compliance and ‘zero’ backlash, while maintaining a highly consistent output ratio (less than 4-5% variation).
The gear design was unique – the solid rigid cup enables their patented Orbital Flex Design™ to interface with a compliance flexure to deliver zero backlash and high torque density. Significant fine-tuning was required to get the correct system behavior. It was also essential to understand the challenges of manufacturing the product and to perform various tolerance investigations to ensure a robust design that would tolerate manufacturing variation.
Initially, Adams/View was used to test and compare various early design concepts. Two key designs were further evaluated, with Adams providing the engineering answers that gave the team the insight and confidence to select which candidate best met the design requirements. The first design, which featured a very complex mechanism that relied on precise timing to work properly, was deemed to be unsuitable from a manufacturing perspective. However, the second design was much simpler in terms of part count and function, and performed well in initial tests. This design was further refined to ensure that performance aspects such as transmission error, efficiency, tooth engagement and backlash requirements were met. The Adams model was then used to correlate with prototype testing to ensure manufacturing constraints were satisfied. Motus Labs commercially launched the ML2000 gear series that utilizes Orbital Flex™ in Q1 2023.
Alongside the support from Hexagon on how to apply Adams to solve real world challenges, Canada-based partner Advanced Mobility Products was brought in to provide specialized gearbox manufacturing expertise. As part of their engineering process, AMP uses Hexagon’s Romax software and were able to help Motus Labs better understand the manufacturing feasibility of these new designs. Robert James comments: “AMP were extremely knowledgeable and helpful in the design of our ML2000 gear series. They were able to leverage years of experience in project simulations to provide relevant guidance regarding design changes to strengthen our overall design.”
DEVISING A ROBUST, EFFICIENT WORKFLOW FOR FUTURE PROJECTS
After the success of the services engagement, Motus Labs licensed Adams and have now embedded it as part of their design and development processes. Hexagon have provided mentoring, tech transfer, and advanced training customized to Motus Labs’ models. Gary Hofer (COO) comments: “Thanks to working with senior design engineers from Hexagon and AMP, we have been able to steadily upskill our team to the point they are confident using the tools and taking on the work themselves. We intend to continue leaning on the Hexagon team to leverage their expertise to address new challenges we face, and we are excited to be incorporating additional Hexagon tools into our design workflows to help us continue to provide great solutions to our customers within more efficient processes.”
In addition to Adams, Motus Labs is expanding their use of Hexagon tools to include Apex and Nastran. While they use Adams to characterize gear/gearbox loads and to predict backlash, transmission error and efficiency, they use Apex for more simple static analyses and basic‑level FEA, applying torques and moments to the gears and analyzing the resulting stresses. To complement their process, they use Nastran (and SOL 400) for non‑linear analysis, looking at gear pair contact and analyzing stress on the gear teeth.
Robert James comments: “We have gained several benefits from working with Hexagon. First, we have implemented more efficient processes which allow us to get to the right answer, and to discount wrong answers, very quickly. Second, we have enhanced our understanding of the system performance during the design phase. Prior to leveraging Adams for simulation, we were spending a lot of time creating 3D models and then cutting metal to prove a design concept. Hexagon has shown us how we can do more of our testing digitally, which is saving us a lot of time in iterating and building prototypes. We are able to focus on improving the design early in the process and the design is already 85% vetted by the time we cut any metal. Our original objectives of speeding up design work and reducing the number of physical prototypes has been accomplished thanks to what we have learned from Hexagon.”
The content & opinions in this article are the author’s and do not necessarily represent the views of RoboticsTomorrow
Comments (0)
This post does not have any comments. Be the first to leave a comment below.
Featured Product
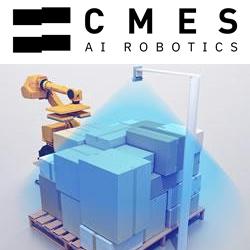