Here, Nigel Smith, CEO at TM Robotics, explains how the use of robots in injection moulding processes, including its recently-expanded 6-axis robot range, can help manufacturers embrace a bioplastic future.
Robots Can Support the Future of Bioplastics - Economical Manufacturing With Bioplastics Needs 6-axis Robots
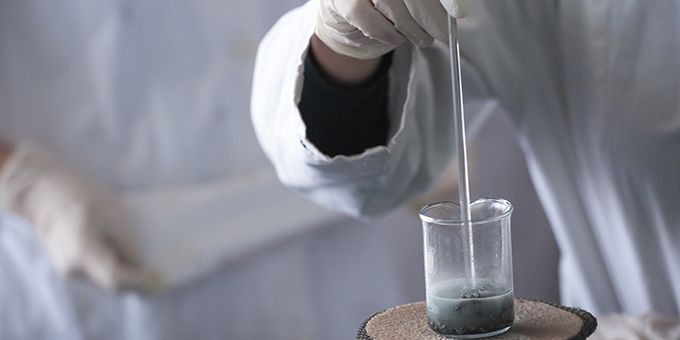
Nigel Smith, CEO | TM Robotics
The bioplastics market is tipped to reach $215 billion by the end of 2027, growing in sectors including consumer electronics, medical applications, agricultural machinery and more. Advanced automation will be essential to ensure products are of the highest quality and accurately cut, formed and measured. Here, Nigel Smith, CEO at TM Robotics, explains how the use of robots in injection moulding processes, including its recently-expanded 6-axis robot range, can help manufacturers embrace a bioplastic future.
Bioplastics are made from sugar that comes from corn, sugar cane or sugar beets. They are more environmentally friendly than traditional plastics manufacturing since they can be made from renewable resources. This type of plastic is rising in popularity as an alternative to petroleum-based plastics, as manufacturers become increasingly conscious of plastic waste littering our oceans.
While there are real opportunities in bioplastics, there are also challenges. Like all plastic moulding operations, production runs, both small and large, must run uninterrupted to produce a certain number of products per hour. There must be standards in place for loading and unloading moulds in a predictable and efficient fashion, and smooth working between machines and human workers on the production line. These standards must be met for injection moulding, one of the most common manufacturing processes.
Longer arms
For robots in bioplastics, six may be the magic number. 6-axis robots are among the most widely-used industrial machines, and are already known as being the trusted workhorse of injection molding applications. However, many manufacturers are still reluctant to invest in robots — why is this?
Cost and space are common barriers for many manufacturers. But another, less reported, obstacle is that many manufacturers are wary of the cultural and procedural changes that robotics may demand. That includes whether their human production line workers have the technical understanding and skills required to use robots.
Manufacturers are wary of stepping away from the established ways of doings things — whether it’s a production process, method of communication, or a trusted machine or tool — as such a change invites risk. First, robot designs must fit into smaller spaces to suit manufacturers’ growing concerns over “machine real estate,” meaning robots must fit their goal that every square metre of production space is used for production. Second, in its Digital Factories 2020 report, Pricewaterhouse Coopers (PwC) cites “insufficient digital company culture, or a reluctance on the part of human workers to embrace digital change,” as an obstacle to robotising production lines.
Nevertheless, the good news is that robots are increasingly evolving to apply to manufacturers existing ways of doing things. They are becoming smaller, faster and more flexible and adaptable to specific production lines. TM Robotics, the premier partner of Shibaura Machine — formerly known as Toshiba Machine — robotics, offers a greater variety of robots, having recently expanded their range to offer an even more comprehensive choice of its six-axis robots to suit all applications — including bioplastics.
Crucially, these robots are also easily integrated with Shibaura Machine’s injection moulding machines. Among the newest equipment is the SXIII range of injection moulding machines. The all-electric range is an enhanced performance model that provides significantly faster injection speeds than traditional moulding equipment. When paired with a fast cycle 6-axis robot for loading and unloading, manufacturers can expect increased throughput.
TM Robotics’ series of vertically-articulated, 6-axis robots are available in three models that all offer low headroom, wider reach and other benefits. Each robot has varying reach and payload specifications, and a longer arm length compared with previous robot ranges. They include its TVL range that are compact, lightweight and space saving, but with all the functionality of a 6-axis robot.
And there is the newest TVM range of highly productive, reliable robots aimed at a multitude of industries, including automotive components, medical, packaging and pharmaceutical ― and plastics. The largest, the TVM1500, provides a maximum reach of 1715 millimeters, the TVM1200 can reach up to 1418 millimeters and the smallest model, the TVM900, provides a maximum reach of up to 1124 millimeters. In addition to three distinctive arm lengths, the operating range of each model can be expanded by mounting the robot on an optional linear actuator.
The machines are designed for enhanced versability and performance, with a streamlined design. With these features, the range can provide support significantly faster loading and unloading speeds for moulding applications. But, what about the reluctance of human workers to embrace digital change?
Easy to program
Plug and play installation is now very much a reality. Robots themselves are becoming easier to program, which makes it easier to win the buy-in of human workers while also reducing training costs. The end result is better collaborations between machines and human workers on injection molding lines.
As McKinsey & Company puts it: “The production systems of the future will still require people in many of the roles they hold today, but the nature of those roles will change. Operators will need new capabilities as low-skill tasks are automated and increasingly sophisticated equipment requires skilled people to run it.”
But, of the growing options available, how can manufacturers be sure to choose the right robots for them? This is where a trusted partner like TM Robotics comes into play. Its team has a cumulative 75 years of experience working with Shibaura Machine equipment, and has long supplied robots for loading and unloading of injection moulding applications. Through its expertise, manufacturers can find their ideal automated injection moulding set up.
As bioplastics grow in popularity over the coming decade, expanded automation will be crucial for ensuring injection moulding is as economically viable as the bioplastics themselves. To this end, 6-axis robots can play a vital behind-the-scene role in helping to reduce the levels of plastic waste littering Earth’s oceans and environment.
The content & opinions in this article are the author’s and do not necessarily represent the views of RoboticsTomorrow
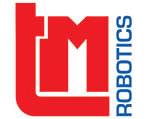
TM Robotics (Americas) Inc
TM Robotics, in partnership with Shibaura Machine, formerly known as Toshiba Machine until 1st April 2020, offers a comprehensive range of industrial robots ideally suited for high-precision assembly, machine loading/unloading and material-handling applications that can be dust proof, clean room, or IP65/67. The company's extensive product line starts with a Cartesian solution available in thousands of combinations from single actuators to four-axis solutions; six-axis solutions that can include precise vision-control; and a complete range of SCARAs from low cost to the industry-leading SCARA with 1200-mm reach that can carry up to 20 kgs. TM Robotics sells and services robots throughout Europe, the Middle East, India, Russia, and Africa, as well as North, Central, and South America, from headquarters in Hertfordshire, England and Elk Grove Village, IL, USA. For more information, visit www.tmrobotics.com or follow us on Twitter, LinkedIn and YouTube.
Other Articles
Investing in the UK’s injection moulding sector - The case for all-electric machines and robotic integration
Robotic solutions for pharmaceutical packaging - Automated system addresses key limitations of manual processes
Automating pick-and-place in food manufacturing
More about TM Robotics (Americas) Inc
Comments (0)
This post does not have any comments. Be the first to leave a comment below.
Featured Product
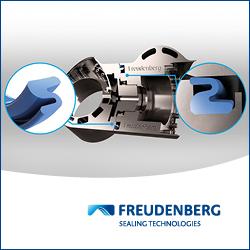