Using ATI’s QC-11 Tool Changer and RCT-151 Radially-Compliant Deburring Tool along with a Renishaw probe, they produced a demonstration highlighting their expertise in aiding potential customers to maximize productivity of the robots already installed in their facilities
Productivity Inc. Wants Your Robot to Do More
Case Study from | ATI Industrial Automation
Productivity Automation Group (a FANUC authorized system integrator), located in Plymouth, MN, specializes in machine tool-tending applications that focus on providing innovative solutions to assist their customers in maximizing their automation efforts. Using ATI’s QC-11 Tool Changer and RCT-151 Radially-Compliant Deburring Tool along with a Renishaw probe, they produced a demonstration highlighting their expertise in aiding potential customers to maximize the productivity of the robots already installed in their facilities.
Productivity’s automation engineers knew that in many machine tending applications like inspection, laser marking, part-cleaning, machine casting, and forging, the robot is not in use most of the time. They set out to demonstrate to customers the versatility of a single robot, beyond just loading and unloading parts. By incorporating a tool change platform in their robot cells, they could expand the robot's capabilities and decrease machining cycle times.
Recognized for its lightweight and compact design, coupled with a robust high-strength locking mechanism, ATI’s QC-11 Tool Changer plays a crucial role in Productivity’s demo by facilitating the swift and automatic exchange of robotic end-of-arm tooling. To further enhance robot flexibility, ATI Tool Changers can be configured with a wide array of standard add-on Utility Modules, enabling support for various end-of-arm utilities and applications.
The demo shows the deburring path being generated using Fusion360 after Renishaw’s probe was used to locate the part and set a user frame to create a toolpath for the RCT-151 Deburring tool to follow. Using that framework as a work coordinate, they ran a toolpath on the robot that was generated from the same CAM software as the machine tool program to deburr the part, saving additional programming time.
Increasing feed rates with uniform quality, no matter how the tool is oriented, is simple work for ATI’s RCT-151 Radially-Compliant Deburring Tool. The pneumatically controlled, articulated design is ideal for removing parting lines by allowing the cutting bit to follow the part profile and compensate for surface irregularities, part location, and robot repeatability while maintaining a constant force that can be controlled and adjusted on the fly.
ATI’s end-effectors and Renishaw’s probe on FANUC’s robot arm enable seamless transitions throughout the process: from using the probe to gather data, to having precision deburring performed on the part, to moving the part and preparing to repeat the process with a new unit. The ease of completing the task highlights how solutions like this could save time and labor, while also enhancing process stability.
The content & opinions in this article are the author’s and do not necessarily represent the views of RoboticsTomorrow
Comments (0)
This post does not have any comments. Be the first to leave a comment below.
Featured Product
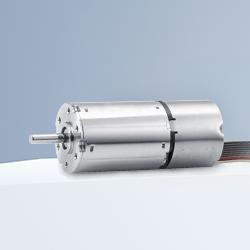