The integration of robotic technology into machining has been a game-changer for some manufacturers. No longer constrained by workspace size and CNC machine cost, there is almost no limit to the possibilities of robot machining.
The Rise of Robot Machining: Unleashing the Future of Manufacturing
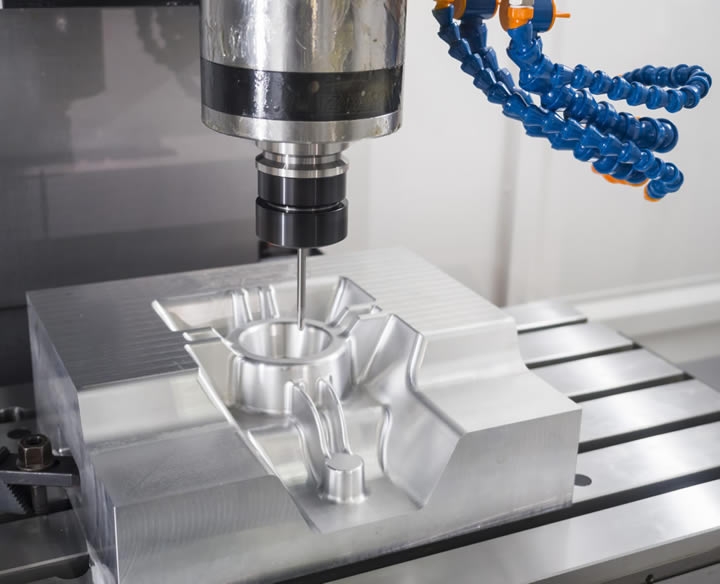
Alex Owen-Hill | RoboDK
The integration of robotic technology into machining has been a game-changer for some manufacturers. No longer constrained by workspace size and CNC machine cost, there is almost no limit to the possibilities of robot machining.
Cell therapy manufacturing is a uniquely complex process in the pharmaceutical industry. It presents unique challenges over other pharmaceutical processes as it requires manufacturers to handle and store living cells.
One company, Multiply Labs, has created a system to overcome these challenges by using robots and RoboDK.
Using Multiply Labs’ innovative approach, automated cell therapy manufacturing has the potential to significantly reduce costs while ensuring statistically equivalent outcomes to manual processes in terms of cell yields, viability, and phenotype.
This new system could bring about a new era of producing this type of therapy, surpassing the previous time-consuming manual processes, and ultimately, supporting the scalability of cell therapies for patients in need.
Let’s look at how they used RoboDK to create the system.
Why Robot Machining is the Future of Manufacturing
Manufacturing technology is always evolving. With each passing year, even simple new developments open up countless avenues for more efficient, flexible, and customizable manufacturing processes.
Robot machining has been a rising star for some time now.
The approach involves using industrial robots in place of conventional computer numerical control (CNC) machines. A machining end effector is added to the end of the robot, which is them programmed to follow the machining path.
Some benefits of robot machining include:
- Flexibility and adaptability — Machining is highly flexible compared to conventional CNC. A single robot can be used for complex projects that would previously have required several CNC machines.
- Cost-effectiveness — Robots can also be much less costly than conventional CNC machines. This cost-effectiveness is multiplied for the more complex projects.
- Simple programming — With the right programming tools, like RoboDK, robot machining can significantly simplify your life as a manufacturer.
While there will always be a place for other manufacturing processes, robot machining is now becoming a valued approach, particularly for large and complex projects.
The Key to Efficient Robot Machining: Integrate Your Software
How can you get the most from robot machining?
One key to success is to ensure that your software all works nicely together. When your robot programming system combines easily with your existing software tools, the process is as simple as any other machining operation… or, often, simpler!
For example, RoboDK includes plugins to integrate with the world’s most popular CAD/CAM software. These reduce the learning curve for robot machining and help you easily integrate robots into your existing operations.
These plugins streamline the interaction with popular machining packages, including Fusion 360, hyperMILL, BobCAD-CAM, and many more.
RoboDK also includes native support for hundreds of robot models from many manufacturers, allowing you to quickly get up and running no matter what robot you choose.
Robot Machining vs. CNC Machines and Which to Choose
But is robot machining really comparable to conventional CNC?
This is a question that many manufacturers have when they are first considering robot machining. And it is a good question. Both machining options have their own advantages and disadvantages.
There are various differences between robot machining and CNC.
CNC machines are primarily tailored to high-precision machining tasks. They tend to specialize in just one operation, such as milling, drilling, turning, and cutting. They have a limited cube-shaped workspace, take up a lot of space, and are expensive.
Robot machining, by contrast, excels at versatile operations. A single robot can be used for multiple machining tasks. They can have a huge workspace, support complex geometries, and are offer an attractive return on investment.
For a detailed comparison of the two machining approaches, read our article Can a Robot Outperform a CNC Machine for Robot Machining?
4 Exciting Projects Using RoboDK for Robot Machining
Over the years, we have seen many exciting projects where our users have employed robot machining to meet their needs.
Here are projects that we have previously featured on our blog:
- Robot Milling for Movies — This project highlights the potential for using robot milling to create large props for Hollywood movies. Robots can create impressive sculptures with precision.
- Building Facade Creation — This innovative projects showed how robot machining was used to fabricate complex facade shapes for architectural design. The project combined RoboDK with the Rhino and Grasshopper parametric design software, using our plugin.
- Custom Hockey Stick Milling — This project employed RoboDK for the creation of a milling machine for custom-designed hockey sticks. The system allowed for complex shapes and high personalization.
- Pipe Milling — This project used robot machining to create a self-contained pipe milling system. The entire system was housed in a shipping container.
With projects like these, companies don’t simply replace a conventional CNC machine with a robot. Instead, they harness the unique benefits of robot machining technology to create systems that were just not possible before people started using robots in this way.
All these projects used RoboDK as the software to create robot programs, combining it into their existing software workflow.
Revolutionize Your Manufacturing with Reliable Robotic Machining
How can you get started with robot machining for your own projects?
The entry into robot machining is much less daunting than some people imagine it will be. There are simple steps for learning to program robots that should be easy to pick up for anyone familiar with CNC programming.
If you are looking to add robot machining to your workflow, a good place to start is to look through our blog at the different projects people have already achieved. There are many resources on this website for getting started with the RoboDK software.
As robot machining technology continues to develop, we expect to see even more inventive ways to use this technology for manufacturing.
The content & opinions in this article are the author’s and do not necessarily represent the views of RoboticsTomorrow
Comments (0)
This post does not have any comments. Be the first to leave a comment below.
Featured Product
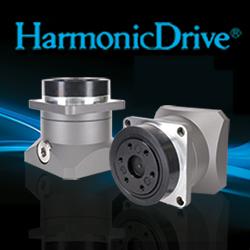