As a robotic center with deep expertise in industry automation, Campetella is exceptionally positioned to use HP 3D Printing to produce robotic components and automatic machines parts.
HP MULTI JET FUSION Helps Campetella Robotic Center Reduce Lead Time and Cost
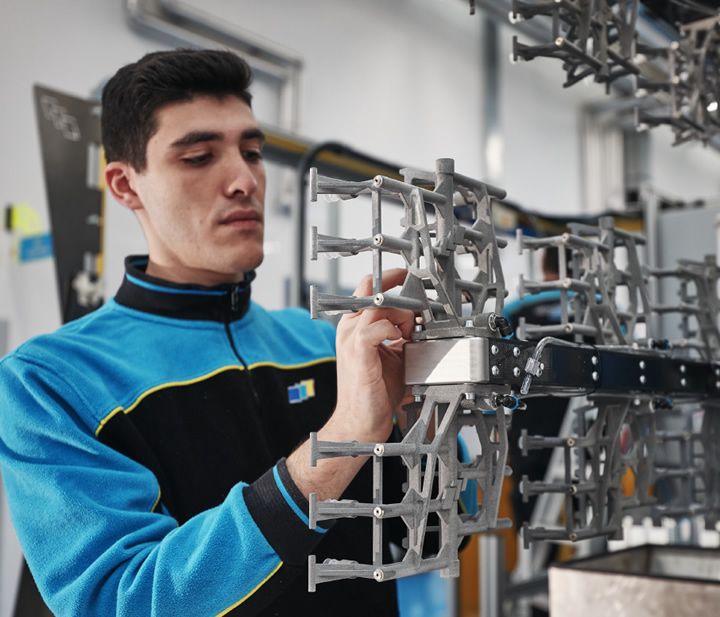
Case Study from | HP Industrial 3D Printers
INTRO
Campetella Robotic Center is an Italian company specialized in the production of industrial robots and automation systems. Since 1897, Campetella has been involved in producing technological machinery. The company developed a lot over the years, and it’s now dealing with software, system installation, sales, and after-sales service of robotics products all over the world. Their core business is IML (In-Mold Labelling) equipment to insert labels directly into a mold to be melted into a container (food container, or pharma container, etc.).
Campetella produces both Cartesian and cylindrical coordinate robots, and a variety of components that are used to make the systems, and they integrate anthropomorphic robots where necessary.
It was natural to consider additive manufacturing as a new technology to improve and evolve further for a company with such a strong innovative nature.
CHALLENGE
Campetella has an internal area that deals with the production of parts, workshops, machining centers, numerical control lathes, and much more. Hence, the first areas on which Campetella Robotic Center chose to test the new technology and increase their know-how were some test pieces and prototypes intended for internal use.
Many of the parts were suitable for additive manufacturing, and after a short time, the company decided to abandon outsourcing and purchase a small fleet of 3D printers in-house.
The HP MJF 4200 3D printer was chosen because it fully met Campetella Robotic Center's primary needs:
• Robust and isotropic parts • User-friendly workflow • Top-level service and support
After bringing the MJF 4200 into the company, the technical skills of the engineers at Campetella Robotic Center skyrocketed.
“Doing automation over time has changed. When we started, we were asked to find solutions to help the operator work better. Today, doing automation means industrializing processes with increasingly shorter lead times,” says Carlo Campetella, Chairman of Campetella Robotic Center. “The advent of 3D printing has been a huge enabler, opening up a world to us that is only held back by imagination.”
SOLUTION
With HP MJF, “most 3D printed components of our automated cells are customizations of the final product” said Marino Di Giampaolo, Mechanical Designer at Campetella Robotic Center. As of now, Campetella can 3D print end-of-arms tooling, dummy cores, label holders, and so on.
In the new, additively manufactured version, “end-of-arm tooling has the same functionality, if not better, of the ones produced with traditional technologies” adds Marino. “This allows us not only to create high-performing machines but also to reduce both energy consumption and cycle time.”
We asked Elia Campetella, CEO of Campetella Robotic Center, why they chose HP 3D Printing Technology. “HP support is crucial because of both the service and the technology provided, not to mention the field assistance. A technology partner like HP always guarantees fast and reliable customer service.”
RESULT
Additive Manufacturing has been a game-changer for Campetella as they specialize in machines that insert labels into various types of molds and HP MJF led to a reduction of 50% of the weight of spindles of labeling systems, that were previously produced through CNC.
Additionally, since the addition of HP MJF technology, tooling time-to-market dropped from 8 to 4 weeks, thanks to the very fast 3D printing time.
HP MFJ “opened a new world where the only limit is the designer imagination.” said Carlo Campetella, Chairman of Campetella Robotic Center. “Today, thanks to Additive Manufacturing, we can make a customized machine that, at first sight, looks like a product ready for the market since the very first prototype.”
But mostly, bringing 3D printing into the company has led to a change in the habits of the technical department. According to Elia, “something that has completely changed our process to design customized systems and the time required to develop new prototypes or fulfill new orders.” In his own words, “Flexibility turned into technology”.
The content & opinions in this article are the author’s and do not necessarily represent the views of RoboticsTomorrow
Comments (0)
This post does not have any comments. Be the first to leave a comment below.
Featured Product
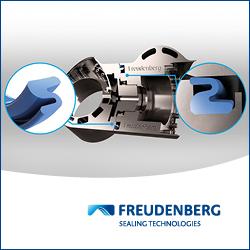