Cobots, or Collaborative robots, take away some of the environmental, and spatial, dangers traditional robots may cause, allowing them to work alongside humans. Their interaction with humans is more natural, they share the same workspace, and Cobots are very easily reprogrammed.
Greg Conrad | AX Control
Alongside modern industrial automation, terms like ‘Cobot’ are showing up in the web space more than ever. You might be wondering, “What are cobots?”, So let me give you a brief description and a little history first. Robots have replaced human labor in risky and crucial factory jobs since the industrial revolution but they operated within safety measures. Cobots, or Collaborative robots, take away some of the environmental, and spatial, dangers traditional robots may cause, allowing them to work alongside humans. Their interaction with humans is more natural, they share the same workspace, and Cobots are very easily reprogrammed.
Cobots Background
Although Cobots have only been commercially available for about a decade, they were actually invented back in the 90s. General Motors funded research grants to make robots work in collaboration with humans as helping hands between 1994 and 1995. In 1996, two professors at Northwestern University J. Edward Colgate and Michael Peshkin invented Cobots. General Motors came up with an alternative term Intelligent Assist Device (IAD), although in reality, the term ‘Cobot’, or 'Collaborative Robot' was more accepted. A draft of IAD/Cobot safety standards and procedures was prepared in 2002, updated later in 2016.
What benefits can Cobots offer?
Business in the 21st century is highly competitive and falling behind the competitors may cause irrecoverable disasters to a company. Collaborative robots can offer higher efficiency to industries as well as many other benefits.
Here’s a list of 5 benefits Cobots offer, right out of the box.
-
Better Robot-Human Interaction and Efficiency: In a typical assembly line set up, the human workers load up the mechanical robots with the necessary parts and robots do the rest of the job. If human intervention is required, either the entire production operation needs to be put to a stop or it is a long wait until the machines finish the production. In a collaborative robot set up, humans work with robots in the same workspace, therefore efficiency is greatly increased. Various studies show how Cobots can reduce human idle hours in production by 85%!
-
Suitable for Small-Scale and Mid-Scale Production: Typically the larger industries with higher production volume opt for a robotics centered solution, whereas small and mid-sized industries stick to manual labor for cost optimization. With Cobots, the case is no longer the same. Most collaborative robots don’t require a hefty setup process and they are flexible to adjust for different outputs. Cobots are widely available for purposes like cutting, shaping, sanding, polishing, lifting, sorting, and packaging – exactly what a small or mid-sized industry might need.
-
Increased Return on Investment (ROI): Once cobots are installed, Industries have better efficiency, flexibility and production capability. Thus, higher ROI is naturally ensured. Cobots can be conveniently placed anywhere and relocated whenever needed, which essentially leads to eliminating any non-productive activities during the production hours. As a whole, this increases ROI. Labor and maintenance costs are reduced, resulting in a bigger profit margin.
-
Safer Work Environment: Since Cobots are designed with human involvement and collaboration in mind, each of these units are thoroughly checked for safety right off the production line. Cobots ensure a safer work environment, especially in applications where human errors can hinder progress, like in medical operation scenarios, these robots can effectively take over and accomplish their tasks without making mistakes.
-
Cobots are the Future: Further automation in production is inevitable. As machines take over, it is fairly difficult to determine what human roles are going to look like after a decade, or two. But with Cobots, both machine output and human efforts go side by side. By 2020, cobot sales are expected to hit $3.1 billion, but as extensive research and development is done, I expect this number will continue to rise as we get closer to that date. The sooner an industry moves forward with Cobots, the better.
Conclusion
In the near future, collaborative robots will play major roles in the next industrial revolution. There is one downside though – a lot of unskilled labor jobs could be rendered useless overnight. However, new jobs will open up. With some retraining and adaptation to the new positions, we should not see a significant loss of industrial jobs due to cobots.
The content & opinions in this article are the author’s and do not necessarily represent the views of RoboticsTomorrow
Comments (0)
This post does not have any comments. Be the first to leave a comment below.
Featured Product
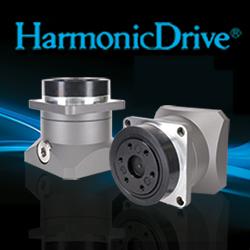