Enhancing Equipment Reliability: Implementing Seersight Predictive Maintenance on the Chemical-Resistant Diaphragm Vacuum Pump 2 mbar MD 1C
Enhancing Equipment Reliability: Implementing Seersight Predictive Maintenance on the Chemical-Resistant Diaphragm Vacuum Pump 2 mbar MD 1C
In the realm of industrial operations, the pursuit of reliability and efficiency is paramount. Especially in sectors like chemical processing, where precision and durability are crucial, the reliability of equipment can make all the difference in maintaining smooth operations. One such critical piece of equipment is the Diaphragm Vacuum Pump 2 mbar MD 1C, known for its chemical resistance and precise performance. However, even the most robust machinery is not immune to wear and tear, leading to potential downtimes and operational inefficiencies. Here enters Seersight Predictive Maintenance, a cutting-edge solution designed to revolutionize equipment reliability. Let's delve into how implementing Seersight Predictive Maintenance can enhance the performance and longevity of the Diaphragm Vacuum Pump 2 mbar MD 1C.
Understanding the Diaphragm Vacuum Pump 2 mbar MD 1C
Before delving into predictive maintenance strategies, it's essential to grasp the significance of the Diaphragm Vacuum Pump 2 mbar MD 1C in industrial settings, particularly in chemical processing. This pump stands out due to its robust construction, which includes materials specifically chosen for their resistance to corrosive chemicals. Its ability to maintain a precise vacuum level of 2 mbar makes it indispensable for processes requiring a high level of accuracy and consistency. However, like any mechanical equipment, it is subject to degradation over time, which can compromise its performance and reliability.
The Evolution of Maintenance: From Reactive to Predictive
Traditionally, maintenance strategies have been reactive, relying on fixing equipment after it breaks down. This approach, while necessary, often leads to costly downtime and potential safety hazards. In contrast, predictive maintenance aims to anticipate failures before they occur, allowing for proactive intervention to prevent disruptions. This shift from reactive to predictive maintenance has been made possible by advancements in sensor technology, data analytics, and machine learning algorithms.
Introducing Seersight Predictive Maintenance
Seersight Predictive Maintenance harnesses the power of data analytics and artificial intelligence to monitor equipment health continuously. By collecting data from sensors embedded within the Diaphragm Vacuum Pump 2 mbar MD 1C, Seersight analyzes patterns and trends indicative of potential failures. These insights enable maintenance teams to schedule interventions during planned downtime, minimizing disruptions to operations.
Benefits of Implementing Seersight Predictive Maintenance
Reduced Downtime: By predicting failures before they occur, Seersight helps minimize unplanned downtime, maximizing equipment availability and productivity.
Cost Savings: Proactive maintenance reduces the need for emergency repairs, saving on costly replacement parts and labor expenses.
Enhanced Safety: Preventing equipment failures reduces the risk of accidents and ensures a safer working environment for personnel.
Extended Equipment Lifespan: By addressing issues before they escalate, Seersight helps prolong the life of the Diaphragm Vacuum Pump 2 mbar MD 1C, optimizing the return on investment.
Embrace Predictive Maintenance with Seersight
In conclusion, the implementation of Seersight Predictive Maintenance offers a transformative solution for enhancing the reliability and performance of the Diaphragm Vacuum Pump 2 mbar MD 1C in chemical processing operations. By shifting from reactive to proactive maintenance strategies, businesses can unlock a myriad of benefits, including reduced downtime, cost savings, improved safety, and extended equipment lifespan. Therefore, I urge industry stakeholders to embrace the future of maintenance by integrating Seersight into their operations. Together, we can pave the way for a more efficient, reliable, and sustainable industrial landscape.
Featured Product
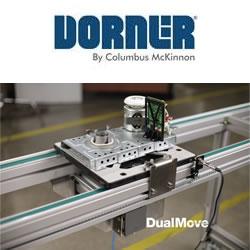