In this article, we will explore the key considerations for integrating servo drives with robotics to achieve smoother, more effective automation systems.
Integrating Servo Drives with Robotics: Key Considerations for Seamless Automation
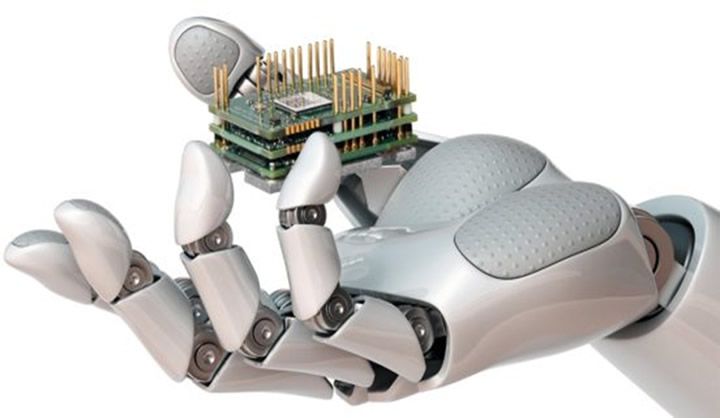
Article from | ADVANCED MOTION CONTROLS
As industries increasingly move toward automation, the integration of servo drives with robotics has become a critical factor in optimizing performance and productivity. Servo drives enable robots to perform highly precise, repeatable tasks, making them essential for modern automated systems. Their role in enhancing automation lies in their ability to improve precision, flexibility, and efficiency, allowing for more complex operations while reducing human intervention. This seamless integration can lead to significant advancements across industries, from manufacturing to healthcare. In this article, we will explore the key considerations for integrating servo drives with robotics to achieve smoother, more effective automation systems.
What Are Servo Drives, and Why Are They Essential for Robotics?
Servo drives are devices that control electric servomotors in real-time, managing factors such as speed, position, and torque. In robotics, servo drives are fundamental because they allow robots to execute highly specific movements with unparalleled precision. This precision is crucial in tasks requiring exact control, such as assembling delicate electronics or performing surgical procedures with robotic arms. Servo drives work by receiving commands from the control system, processing feedback, and adjusting motor outputs to ensure optimal motion control.
What are the Key Functions of Servo Drives?
Servo drives perform several critical functions in robotic systems:
- Motion control: But what is motion control? It ensures that the robot moves along the defined path with precise control over its position and velocity.
- Feedback integration: Collects data from feedback devices, such as encoders or resolvers, to adjust motor operations in real-time.
- Torque management: Adjusts torque output to manage load variations, ensuring stable movement under different operating conditions.
- Positioning accuracy: Enables fine control over the robot’s exact positioning, ensuring repeatable and consistent operations.
How Do Servo Drives Differ from Other Motor Control Technologies?
Servo drives offer several advantages over other motor control technologies, such as stepper motors and variable frequency drives (VFDs). While stepper motors are simpler and less expensive, they lack the precision and feedback capabilities of servo drives. VFDs, on the other hand, are often used for less complex operations, such as controlling conveyor belts, where precise positioning is not as critical.
Pros of Servo Drives:
- Higher accuracy and precision
- Faster response times
- Superior torque control
- Real-time feedback integration
Cons of Servo Drives:
- Higher cost
- More complex setup and tuning
- Requires advanced control systems
What Key Factors Should You Consider When Integrating Servo Drives with Robotics?
Successful integration of servo drives with robotics requires careful consideration of several factors to ensure compatibility, performance optimization, and long-term reliability.
How Do You Select the Right Servo Drive for Your Robotic Application?
Choosing the right servo drive for your application involves assessing key parameters:
- Power rating: The servo drive must match the power requirements of the servomotor and the overall robotic system.
- Speed: Ensure the drive can support the desired speed of robotic operations without compromising precision.
- Load capacity: The drive should be able to manage the expected load, including potential variations during operation.
- Environmental factors: Consider external conditions such as temperature, humidity, and dust, which can impact drive performance.
What Role Does Feedback Play in Servo Drive Integration?
Feedback is essential in servo drive systems because it allows for real-time adjustments and ensures that the motor operates within the desired parameters. The types of feedback commonly used in servo systems include:
- Encoder: Provides precise positional feedback, allowing the system to adjust the motor's position.
- Resolver: Offers rugged and durable feedback, ideal for harsh environments.
- Tachometer: Measures motor speed to ensure it aligns with the set parameters.
Feedback loops help maintain control accuracy, a crucial aspect of high-precision robotic tasks.
How Important is the Communication Protocol for Servo Drive and Robot Integration?
Communication between servo drives and robots is vital for real-time data exchange. Common communication protocols include:
- EtherCAT: Offers high-speed communication and low latency, making it ideal for synchronized robotic movements.
- PROFINET: Known for its versatility and support in industrial automation, it is highly reliable for servo integration.
- CANopen: A robust and flexible protocol that works well in distributed control systems.
Pros of EtherCAT:
- Fast data exchange
- Ideal for time-critical applications
Cons of EtherCAT:
- Requires specialized hardware
Pros of PROFINET:
- Versatile and widely supported
- Strong for industrial applications
Cons of PROFINET:
- Higher complexity in setup
What Are the Main Challenges When Integrating Servo Drives with Robotics?
Integrating servo drives with robotics can present several challenges, particularly around synchronization and tuning.
How Do You Ensure Synchronization Between the Servo Drive and the Robot?
Synchronization between the servo drive and the robot is critical for achieving smooth, coordinated movements. Steps to ensure synchronization include:
- Calibrating feedback systems: Make sure that encoders and other feedback devices are correctly calibrated to provide accurate data.
- Adjusting motion control parameters: Fine-tune motion parameters, such as acceleration and deceleration, to match the robot’s operational requirements.
- Testing synchronization: Run test sequences to identify any lag or delay in movements, adjusting parameters as necessary.
How Can Servo Drive Tuning Improve Robotic Precision?
Servo drive tuning allows for the optimization of the robot’s movements, improving precision and control. Key tuning parameters include:
- Proportional gain (P): Adjusts the drive’s response to error in position or speed.
- Integral gain (I): Helps eliminate steady-state errors by adjusting for cumulative error.
- Derivative gain (D): Reduces overshoot by considering the rate of error change, allowing for smoother operation.
Proper tuning of these parameters can significantly enhance the performance of the robotic system.
How to Set Up a Servo Drive for Robotic Applications?
Setting up a servo drive for robotics involves a series of steps to ensure the system operates smoothly and efficiently.
Step-by-step setup process:
- Connection: Connect the servo drive to the power supply, servomotor, and control system.
- Configuration: Configure the drive settings, including power limits, motion control parameters, and communication protocols.
- Tuning: Tune the servo drive to match the specific requirements of the robotic system, adjusting PID parameters as necessary.
- Testing: Run test cycles to ensure everything operates correctly, and fine-tune based on performance data.
What Are the Essential Components of a Servo Drive Setup?
For a fully functional servo drive setup, several components are required:
- Power supply: Provides the necessary electrical power for the servo drive and motor.
- Feedback devices: Such as encoders or resolvers, used for real-time position and speed feedback.
- Communication cables: Ensures data exchange between the servo drive and the control system.
- Control software: Manages the system’s parameters and motion sequences.
What Software Tools Are Used to Program Servo Drives in Robotics?
Common software tools for programming servo drives include:
- Siemens S7: Popular for its robust industrial automation applications.
- Rockwell Automation Studio 5000: Offers flexible programming for motion control.
- Mitsubishi’s MELSOFT: Specialized in integrating servo drives with advanced robotics.
What Are the Advantages of Using Servo Drives in Robotics?
The integration of servo drives with robotics brings numerous benefits to automation systems.
Improved Precision and Accuracy
Servo drives enhance robotic precision, allowing robots to perform complex tasks with high accuracy. Some key examples include:
- Assembly of electronics: Servo drives allow for accurate positioning when assembling delicate components.
- Medical robotics: Surgical robots rely on servo drives for precise movements during operations.
Faster Response Times and Dynamic Motion Control
Applications requiring rapid movements benefit from the high-speed capabilities of servo drives. These include:
- Pick-and-place systems: Servo drives enable fast and accurate picking and placing of items on production lines.
- High-speed packaging: Servo-driven robots can handle quick packaging tasks with minimal error.
Greater Efficiency in Energy Usage
Servo drives optimize energy consumption by adjusting torque and speed based on load requirements. This efficiency leads to:
- Lower operational costs: Reduced energy usage results in cost savings for companies using servo-driven robots.
- Longer equipment lifespan: Efficient power usage minimizes wear on robotic components.
What Industries Benefit Most from Integrating Servo Drives with Robotics?
Several industries have adopted servo drives to optimize their robotic systems.
- Automotive: Robotic arms powered by servo drives are used for precision welding, painting, and assembly tasks.
- Electronics manufacturing: Servo-driven robots assemble components with high precision in smartphones, computers, and other electronics.
- Pharmaceuticals: Servo drives ensure the accurate dispensing and packaging of medications.
- Aerospace: Servo-driven robotics assist in precise manufacturing and assembly of complex aircraft components.
How to Troubleshoot Servo Drive and Robotic Integration Issues?
Even with meticulous planning and setup, challenges may arise when integrating servo drives with robotics. Understanding common issues and troubleshooting them efficiently is crucial for minimizing downtime and ensuring optimal performance.
What Are Common Issues Encountered During Integration?
Some typical problems that can occur during servo drive and robotic integration include:
- Communication errors: Misalignment in communication protocols or faulty wiring can disrupt the real-time exchange of data between the robot and the servo drive.
- Feedback signal loss: If feedback devices, such as encoders or resolvers, are not calibrated or installed correctly, the servo drive may lose position or speed accuracy.
- Tuning problems: Incorrect PID tuning can lead to jerky or sluggish movements, reducing the precision and responsiveness of the robotic system.
- Power issues: Insufficient power supply or voltage instability can cause the servo drive to malfunction, leading to uncoordinated robotic movements.
What Steps Can You Take to Resolve Servo Drive Tuning Problems?
Tuning is a critical part of servo drive integration, and improper tuning can result in performance issues. Here are steps to resolve tuning-related problems:
- Adjust PID parameters: Start by adjusting the proportional, integral, and derivative gains to fine-tune the servo drive’s response.
- Recalibrate sensors: Ensure that all feedback devices are properly calibrated to match the system’s specifications.
- Check for mechanical issues: Misalignment or mechanical resistance can cause tuning issues. Verify that all mechanical components are properly installed and adjusted.
- Run test cycles: After making adjustments, run multiple test cycles to confirm that the system performs as expected and to make any further adjustments if necessary.
How to Optimize the Performance of Servo Drives in Robotics?
To get the most out of your servo drive and robotic system, it is essential to focus on performance optimization through both preventive maintenance and system upgrades.
How Does Regular Maintenance Impact Servo Drive Performance?
Regular maintenance can significantly extend the lifespan of servo drives and ensure consistent performance. Essential maintenance tasks include:
- Cleaning: Dust and debris can interfere with electronic components, leading to overheating or malfunction.
- Recalibration: Periodically recalibrate feedback devices to ensure they provide accurate data to the servo drive.
- Software updates: Keep control software up to date to ensure compatibility with the latest robotic systems and performance improvements.
What Upgrades Can You Make to Servo Drives for Better Robotics Integration?
Technological advancements offer several upgrade options to enhance the integration of servo drives with robotics. Some potential upgrades include:
- Improved encoders: Higher-resolution encoders provide more precise feedback, allowing for better motion control.
- Higher-resolution feedback: Advanced feedback devices can improve the system's responsiveness and accuracy.
- Software enhancements: New software tools may offer better control algorithms, more efficient communication protocols, and enhanced diagnostics features.
What Safety Considerations Should Be Addressed When Integrating Servo Drives with Robotics?
Safety is paramount in any robotic system, and integrating servo drives introduces several important safety factors that need to be addressed to protect both personnel and equipment.
How Do You Ensure Safe Operation of Servo Drives in Robotics?
Servo drives, when combined with high-powered robots, can present significant safety hazards if not properly managed. Key safety measures include:
- Emergency stops: Every system should be equipped with an easily accessible emergency stop function to halt the robot immediately in case of a malfunction or accident.
- Overload protection: Servo drives must be programmed to detect and manage overload conditions to prevent damage to both the motor and the robot.
- Proper grounding: Electrical grounding helps protect the system from power surges, reducing the risk of equipment damage or injury to operators.
What Are the Future Trends in Servo Drive and Robotics Integration?
As technology evolves, the integration of servo drives with robotics is set to become even more advanced, incorporating new capabilities that enhance automation systems.
How Are AI and Machine Learning Enhancing Servo Drive Capabilities?
Artificial intelligence (AI) and machine learning (ML) are revolutionizing servo drive performance by enabling predictive maintenance and adaptive tuning. AI algorithms can analyze vast amounts of data from servo systems to identify patterns and predict potential failures before they happen, reducing downtime and improving overall reliability.
- Predictive maintenance: AI can forecast when components are likely to fail, allowing for proactive repairs and reducing unexpected downtimes.
- Adaptive tuning: ML algorithms can automatically adjust servo drive parameters in real-time, optimizing performance without manual intervention.
What Impact Will 5G and IIoT Have on Servo Drive-Robotics Integration?
The advent of 5G and the Industrial Internet of Things (IIoT) will have a profound impact on servo drive and robotic integration, allowing for faster communication and more intelligent data analysis.
Benefits of 5G and IIoT:
- Faster communication: 5G offers ultra-low latency, allowing servo drives and robots to communicate in real-time with minimal delay.
- Real-time analytics: IIoT devices can gather data from multiple systems and provide insights into performance optimization.
- Remote monitoring: With IIoT, companies can monitor servo drive performance and robotic systems remotely, enabling quick responses to any issues that arise.
What Are the Alternatives to Servo Drives for Robotics?
While servo drives are highly effective in many robotic applications, alternative technologies can also be used depending on the specific needs of the system.
Alternatives to Servo Drives:
- Stepper motors: Simple and cost-effective but less precise and lacking in feedback capabilities.
- Variable frequency drives (VFDs): Ideal for less complex systems that do not require high precision, such as conveyor belts.
- Pneumatic actuators: Provide powerful motion in simple, repetitive tasks but lack the precision and control of servo drives.
Pros and Cons of alternatives:
- Stepper motors:
- Pros: Affordable, simple setup
- Cons: Lower precision, no feedback
- VFDs:
- Pros: Reliable for less demanding applications
- Cons: Lacks fine-tuned control and feedback
- Pneumatic actuators:
- Pros: High power, simple mechanics
- Cons: Limited precision and control
Conclusion
Integrating servo drives with robotics is a complex but highly rewarding process that significantly enhances the precision, flexibility, and efficiency of automated systems. Key considerations, such as selecting the right servo drive, ensuring proper tuning, and optimizing communication protocols, are essential for seamless integration. While there are challenges, such as synchronization and tuning issues, careful planning and regular maintenance can mitigate these risks. By staying aware of emerging trends such as AI, 5G, and IIoT, companies can future-proof their systems, ensuring they remain competitive in an increasingly automated world.
The future of servo drive and robotic integration promises even greater efficiency and capabilities, but successful integration requires thorough planning, regular maintenance, and the ability to troubleshoot issues effectively. Whether in manufacturing, healthcare, or aerospace, servo drives are playing an essential role in advancing automation technology, and their integration with robotics will continue to shape the industry in the years to come.
The content & opinions in this article are the author’s and do not necessarily represent the views of RoboticsTomorrow
Comments (0)
This post does not have any comments. Be the first to leave a comment below.
Featured Product
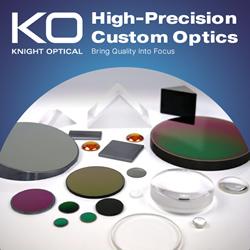