KUKA Robotics Showcases Innovative Robotic Solutions for the Packaging Industry at PACKEX 2011
KUKA Robotics Canadato demonstrate an innovative unified controlled palletizing solution, in addition to the LWR lightweight robotic technology, at PACKEX Toronto, Canada's most comprehensive resource for Packaging and Processing in booth #1113.
Demonstrating KUKA\'s response to customer demand for a unified controlled palletizing solution, KUKA will display a KR 40 PA robot. This solution is provided by select Official KUKA Robotics System Partners. KUKA Robotics is an Encompass Partner.
KUKA Robotics will also showcase the LWR 4+, a lightweight robot with 7 axis, 7kg payload capacity that weighs in at 16kg in total unit weight, demonstrating demanding assembly tasks that require the utmost precision, and a sensitive but powerful touch. It comes amazingly close to the motion sequences of the human arm. Through force-controlled surface following the operator can manually guide the robot to different positions in the workspace while controlling and teaching the LWR using the very simple user interface.
Additional KUKA robots on the PACKEX show floor will be featured by KUKA Robotics Official System Partners: CertoTech,Inc. (booth # 147), Jantz Canada (booth #671), and Programmable Control Systems, Ltd. (booth #966). When visiting the participating booths attendees will have the opportunity to enter into the KUKA Robotics Passport Daily iPad® Giveaway. For more information on the giveaway visit any of the participating partners mentioned above or visit the KUKA booth for more information and contest rules.
Executives, Managers, Supervisors, Project Managers, Engineers, and Purchasing Agents who are charged with tasks of streamlining their company's frozen food and cold storage manufacturing operations are invited to join KUKA for the "Applying Robots in a Freezer Environment" seminar held on Wednesday, June 22nd from 3:10 - 3:30 pm in booth #447.
"Applying Robots in A Freezer Environment" is focused on educating attendees about the application of robotic technology into freezer environments. The discussion will include a review of the markets and applications, equipment challenges and a review of successful applications.
For more information or to set-up a booth appointment with a KUKA staff member please email us at: kukainfo@kukarobotics.com or visit http://www.kukarobotics.ca.
About the KUKA Robot Group
KUKA Robotics Canada, Ltd. along with KUKA Roboter GmbH, Augsburg Germany (part of the KUKA Aktiengesellschaft group of worldwide companies), rank among the world\'s leading suppliers of industrial robots and material handling vehicles. Core competencies include the development, production, and sale of industrial robots, controllers, software, linear units, and omniMove™ omni-directional motion platforms. KUKA robots are utilized in a diverse range of industries including the appliance, automotive, aerospace, consumer goods, logistics, food, pharmaceutical, medical, foundry and plastics industries as well as multiple applications including material handling, machine loading, assembly, packaging, palletizing, welding, bending, joining, and surface finishing. KUKA robots range from 5kg to 1300kg payloads, and 635mm to 3900mm reach, all controlled from a common PC based controller platform. KUKA is the market leader in Germany and Europe, and number three in the world. The KUKA Robot Group employs about 2,000 people worldwide. Of these, 1,100 are employed in Germany, either at the KUKA Robot Group headquarters in Augsburg, or at various subsidiaries.In 2009, sales totaled 330,5 million Euro. Twenty-five subsidiaries provide a presence in the major markets of Europe, the Americas and Asia. For more information contact KUKA Robotics at 1 416 585-2123 or visit their website at www.KUKArobotics.ca.
Featured Product
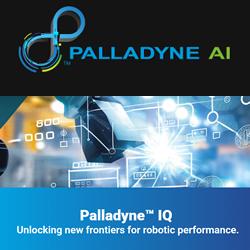
Palladyne™ IQ - Unlocking new frontiers for robotic performance.
Palladyne™ IQ is a closed-loop autonomy software that uses artificial intelligence (AI) and machine learning (ML) technologies to provide human-like reasoning capabilities for industrial robots and collaborative robots (cobots). By enabling robots to perceive variations or changes in the real-world environment and adapt to them dynamically, Palladyne IQ helps make robots smarter today and ready to handle jobs that have historically been too complex to automate.