Army researchers use cutting edge 3D printers
Army explores 3D printing to speed rapid prototypes to the field.
ABERDEEN PROVING GROUND, Md. October 05, 2012
When you walk into this research lab you hear the overpowering hum of massive machines with robotic parts swinging past viewing windows as technicians spray objects with lasers attached to limber metallic arms.
Fifty years ago what goes on in this lab would have been considered science fiction, but what these Army researchers do is scientific fact.
These artisan engineers create three-dimensional objects out of plastic and metal in printers that seem like Star Trek replicators.
"It's allowed us to develop items for the warfighter quicker," said Rapid Technologies Branch Chief Rick Moore, Edgewood Chemical Biological Center. "We're able to come up with concepts and designs using our [computer-aided design] software, print them out and have them in an engineer's hand the next day."
The lab is an element of the U.S. Army Research, Development and Engineering Command, which has labs and research centers across the country. Army scientists, researchers and engineers reach out to the team as needed.
Three-dimensional objects are created with computer-aided design, or CAD, programs, but Moore and his team also use lasers to "read" an object to create a 3D file. This process allows them to reverse engineer practically anything.
For example, an Army technician scans part of a protective mask. As the laser passes over every millimeter of the object, the computer plots points in 3D space. On-screen the mask immediately comes into view as a three-dimensional object. Sending the file to the printer results in a solid copy you can hold in your hand within a few hours.
"It is kind of a magical thing," Moore said. "Seeing people who have never seen it before come through the lab finally get it and understand it ... you can see it in their face. They think it's something from the future."
The team's 3D printers churn out new objects day and night. Researchers use a variety of techniques to get the job done. Some printers use lasers, others spray heated plastic through print heads. One system uses a vat of "goo" to hold the object in place as it creates it layer by minuscule layer.
One massive printer uses a carbon dioxide laser to precisely melt powder. As one layer solidifies, the platform drops a little, a fresh layer of powder is spread and the laser goes to work on the next layer.
"In the end we'll raise the platform up and we'll have the printed object encapsulated in powder," Moore said. "We pull it out, shake off the excess powder and then we've got a part."
Modeling artist Bradley Ruprecht said other printers in the lab are similar to desktop ink-jet printers.
"Instead of depositing ink on a page, the print head deposits a photo polymer onto the platform. A photo polymer is liquid until it's exposed to ultraviolet light and then it polymerizes, or solidifies, into a plastic," Ruprecht said. "Just like your ink-jet printer can mix colors together to get a different color, we can mix materials together. So we can make a rigid plastic or adjust the shore value and make it the stiffness that you want. You can also make parts that have two different materials embedded in each other."
One recent project involved coming up with a solution to help Soldiers carry a heavy piece of sensor equipment in the field.
"The Army Research Lab asked us to develop a holder for a heavy handheld sensor called a Mine Hound, which is used as an improvised explosive device detection sensor," Moore said. "They wanted something that would cradle the handle so it's putting more weight on the Soldiers' vest and back as opposed to just their forearm."
The team scanned the sensor and came up with a myriad of design options in short order.
"The fact that we could do this many designs and print them out and have them in their hands in one week gave them the option to choose between what works best for their application," Moore said. "This is a good example of how we use the technology every day.
Moore said the part is still in the design process.
"We're going to make 10 of them for testing," he said. "Once we have their approval we're going to do the rapid tooling and use injection molding to make several thousand of the holders."
Injection molding is a more conventional manufacturing technique; however, the team uses 3D printing technology to augment, test and even make molds that otherwise would add weeks or months to the process.
"We are deftly pushing what we like to call rapid tooling," Moore said. "It uses these technologies to build molds as opposed to conventional machining a mold."
In the future, Moore sees the technology becoming more commonplace.
"I see it expanding in the materials," he said. "I see the speed increasing and the sizes of the parts increasing. There are also a lot of fascinating medical applications, which kind of overlap with what we'd like to do in the Army in the future."
Medical personnel may use 3D laser scans on a Soldier before he or she is deployed. This would ensure all physical features are on file.
"If a Soldier comes back wounded, we'd have that data on our side where we could possibly build prosthesis that are exactly how the Soldier used to look -- instead of sculpting it and scanning it," Moore said.
3D printing may have been pioneered in the 1980s and brought to the market in the mid-1990s, but combining the processes with more powerful software and accurate lasers offers potential for future manufacturing techniques.
"Every day we're building parts for the customer whether it is an exploded fragment or munitions," Moore said. "The more our customers use 3D printing, the more they're relying on it to do their testing before they do the manufacturing. So, it's become an every day thing."
Moore said he and his co-workers enjoy their jobs.
"If you take a look at this equipment, how could you not like the job?" he asked. "I make stuff every day. I make something from nothing with state-of-the-art technology. The future is definitely fascinating."
Featured Product
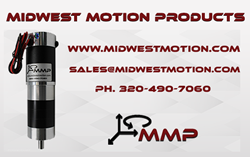
Midwest Motion Products is a leading provider of robust and reliable Motion Control Products.
MMP specializes in supplying high-quality Brushed & Brushless DC Motors & Gearmotors for Robotics and Automation Equipment with a wide range of motor windings and gear ratios. With an impressive track record of more than 8,000 released DC Gearmotors designs and over 2,000,000 individual part numbers, we are renowned for our ability to handle large-scale orders. Due to our huge on-hand inventory, we are also well known for lightning-fast delivery of our standard products. We take pride in our dedicated customer service and our team of knowledgeable sales and engineering experts who are ready to assist you with custom design solutions tailored to your specific application. Additionally, we also offer a wide range of complimentary products, such as DC Motor Controls, DC Linear Actuators, AC-DC power Supplies, and DC Servo Amplifiers and others.