Bishop-Wisecarver Corporation Introduces Seamless Rotary Track Design
HepcoMotion PRT2 1-Trak Curvilinear Motion System Provides Unlimited Track Shapes
Pittsburg, CA -- March 7, 2013 -- The Bishop-Wisecarver Corporation (BWC), a WBENC certified woman-owned company who helps manufacturers and automation solution providers engineer linear and rotary motion solutions, announced today its latest addition to their collection of rotary motion solutions: 1-Trak, a single piece track system that is completely seamless and free running with no possibility of misalignment during installation or in service resulting in smoother, quieter motion.
While conventional track technology limits track paths to simple combinations of straights and curved track segments, 1-Trak allows any conceivable 2D shape to be realized.
"This patent pending guided motion system is an innovative addition to our HepcoMotion® collection of rotary track options as it is now possible to specify any shape with no joints," said Ali Jabbari, Vice President of Engineering at Bishop-Wisecarver. "The design can also include an integral base to form the structural part of a machine."
The entire track element is manufactured from a single piece of steel, with or without a base plate, and features a three-bearing wheel plate. The design's natural strength and accuracy makes it suitable as a structural element of the machine. The product can be customized with holes, slots and other features eliminating the time and cost involved in designing a separate mounting plate for the track system, and can be supplied mounted to an aluminum machine frame.
"This is a significant technical breakthrough for complex and jointless motion shapes," said Brian Burke, Product Manager at Bishop-Wisecarver. "Carriages maintain zero play on all areas of the track and can accommodate very tight curve radii due to variable track widths."
In addition to facilitating a high degree of flexibility in track configuration, the unique three-bearing geometry combined with the track shape ensures that the wheel plate exhibits zero play everywhere on the circuit. This is a key benefit compared to other tracks where there is 'lift off' of the wheel plate from the track between straight and curved sections.
The 1-Trak circuits can also accommodate much tighter bends than is possible with other systems, saving space and costs while allowing the manufacturer to optimize production layout.
Where the application involves higher moment loads the 1-Trak solution is also available in a wide track section. Wide slide sections with widely spaced bearings both across and along the wheel plate can also be supplied to create a very rigid platform and increased moment load capacity.
Track systems can be specified with a vee profile guide section of any size to suit bearings from the extensive HepcoMotion PRT2 or Heavy Duty HDS2 ranges from 13mm to 150mm in diameter. Wheel plates can carry loads from 67 to 51,000 N, and tracks can be made up to 5.5 x 1m or 1.9m square. Corrosion resistant versions as standard are also available.
A rack and pinion driven wheel plate is another standard option when choosing 1-Trak. Its unique design permits a correct and constant mesh between pinion and rack around the entire circuit. It eliminates the need for the pinion to be sprung against the rack to compensate for varying engagement. This substantially simplifies the wheel plate design, reduces cost and dramatically increases system driving forces.
The gear teeth on the track are precision machined and surface hardened to provide outstanding strength and durability. Gears are available from MOD 1.5 to MOD 10 and beyond, depending on application requirements. The system designer can specify pinions alone, a wheel plate complete with pinion and drive flange or with pinions mounted onto a gearbox geared motor.
Also within the new product range is the availability of rectangular flat track profiles and track roller wheel plates. This option is recommended for use when two track systems are mounted in parallel. It allows the roller bearings on one side to 'float' axially whilst the other side is fixed and captivated by the vee bearings. This type of configuration compensates for parallelism tolerances, and completely eliminates the excessive loading and binding that can occur.
For live updates, follow the Bishop-Wisecarver team on Twitter at www.twitter.com/bwcnews
Featured Product
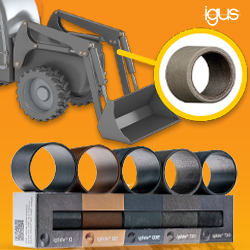