Applied Robotics releases a Safety Control Module & Solution for their Sigma family of Tool Changers
Applied Robotics, Inc., a leading manufacturer of robotic end-of-arm tooling and connectivity solutions, announces the release of the Performance Level d (PLd) compliant Safety Control Module (SCM) for their Sigma Family of Tool Changers.
What is Performance Level?
ARI's SCM is a Tool Changer Safety Circuit within a Safety System
A Tool Changer Safety Circuit ensures the tool changer will not uncouple while it is not in a "safe condition." A "safe condition" is defined as a tool changer engaged in a tool stand (not moving) or in movement without a tool attached to it. Therefore, the tool changer will not drop the tool. Even if the uncouple command is sent, the Safety Control Solution WILL NOT ALLOW the tool changer to uncouple, unless either safe condition is met. (More details are available in the SCM Users' Guide, available upon request from ARI)
ARI's Safety with Diagnostic Coverage
The diagnostic coverage monitors the status of the tool stand present, tool present, and the output valve spool position through a set of normally open and normally closed contacts. In order for proper operation of the system, all dual channel devices need to operate simultaneously. Using an LED status indicator, or a hard wired signal, the end-user can identify when the system becomes unsafe, and can prevent the system from operating in these unsafe conditions. (More details are available in the SCM Users' Guide, available upon request from ARI)
The machine safety world continues to change and evolve, and these new functional safety standards will ultimately provide safer machine control systems and more flexibility to achieve and cost-justify safer designs.
About Applied Robotics
Applied Robotics Inc., headquartered in Glenville, N.Y., is an ISO-9001 registered, employee-owned company serving the world's automation market. Founded in 1983, Applied Robotics designs and manufactures end-of-arm tooling and connectivity solutions intended to solve complex automation problems and improve efficiencies. Serving a wide spectrum of customers and industries ranging from large Fortune 500 companies to small privately-held businesses, the company's wrist-down solutions can be found in manufacturing, welding, assembly, material removal and material handling applications throughout the United States, Canada, Pacific Rim, Mexico, South America, South Africa , Australia and in countries throughout Europe, via Applied Robotics, Europe. More information can be found on the company's website at www.arobotics.com.
Featured Product
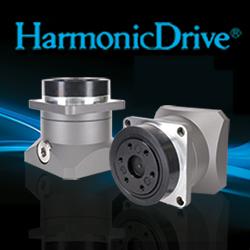
Harmonic Drive - HPG-R Drive Trains for AMR / AGV
The Harmonic Gearhead® gearbox design allows for backdrivability while ensuring high efficiency performance, maximizing elapsed operational time before recharging is necessary. High-capacity cross roller bearing supports heavy payloads.