OPS+ Collision and Overload Sensor
The OPS+ effectively protects the robot and end effector from being damaged during a crash. The OPS+ will allow the EOAT to deflect and comply in the event of a crash. At the same time, a mechanical switch will detect the deflection and send a signal to the robot controller, and then an E-stop can be issued. This protects the system from the damage that would have otherwise occurred without the sensor.
After a crash situation, the OPS+ will be deflected off center. But it can easily be reset manually which returns it to the normal operating position to within 20 microns.
The stiffness of the OPS+ can be adjusted with air pressure. This allows the unit to be adjusted so that it is rigid during normal operation, but it will comply during a crash before any damage is done to the end effector. The sensitivity of the mechanical switch can also be adjusted to trigger at different levels of deflection.
About SCHUNK: SCHUNK is the worldwide competence leader for clamping technology and gripping systems. Totaling more than 60 years of experience, SCHUNK is a family owned operation and a global player in one. For more information, visit www.schunk.com.
Featured Product
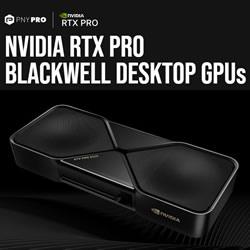
VIDIA RTX PRO™ BLACKWELL DESKTOP GPUs
NVIDIA RTX PRO™ - Built for Professionals - NVIDIA RTX PRO Blackwell Desktop GPUs feature the latest breakthroughs in AI, ray tracing, and neural rendering technology to power the most innovative workflows in design, engineering, and beyond.