GROUNDBREAKING SAFETY PLC SPEEDS AND SIMPLIFIES SAFETY ENGINEERING FOR COMPLEX CONTROL PROJECTS
* special features simplify complex motion-related applications including wind power, cranes, hoists and robotics
New Berlin, WI, October 8, 2013 --- ABB has launched a new safety PLC
speed and simplify the development of safe control solutions for the most
complex control applications. The safety PLC - the AC500-S - is a new
addition to ABB's well-known AC500 PLC range and features a dual processor
architecture that complies with SIL3/PL e functional safety levels. Prior to
commercial release, the new controller has been extensively field tested
over three years in some 10 pilot applications including different types of
cranes, mining hoists, automatic guided vehicles, and robotics.
Among many pioneering features for the safety PLC market segment, ABB's new
AC500-S includes support for Structured Text (ST) programming - in addition
to conventional graphical function block diagram (FBD) and ladder diagram
(LD) software. This provides users with a high level programming approach
that can greatly simplify the development of solutions for sophisticated
applications requiring complex algorithms and mathematics. The feature is
complemented by the inclusion of a powerful suite of functions for
trigonometric calculations, including COS, SIN, TAN, ASIN, ACOS and LOG. The
mathematical capability is ideal for ensuring safe control of movement in
applications involving complex kinematics - such as on cranes, hoists and
manipulators.
Existing AC500 PLC users can convert to safety PLC architectures, and start
programming applications very easily using the new PLC. This is because ABB
already includes support for the safety PLC programming in its CODESYS-based
integrated development environments for control, motion, robotics and HMI.
The new safety PLC hardware also shares the same look and feel as ABB's
standard AC500 PLC family for non-safety applications, as well as identical
dimensions to standard ABB CPU and I/O modules, and the same mounting and
wiring scheme. Both types of modules may be mixed in the same PLC, allowing
it to perform both safety and non-safety functions. This can reduce the
complexity and cost of many projects, and open up new options for
applications such as direct variable mapping and data exchange between
safety and non-safety elements of the control system.
To support the development of safety related applications, ABB has developed
its own safety code analyzer tool, SCA, to verify the safety programming
rules or guidelines according to IEC 61508-3 under FBD, LD and ST. This
powerful tool - believed to be an industry first - has been certified by TÜV
SÜD, who subjected the software to stringent tests. The results are
documented in a technical report, which verifies the analyzer's features,
compliance with standards, and performance in terms of syntax analysis of
safety application source code. A valuable side effect is PLC code that is
more reliable, better structured, and more easily readable, which
contributes to lower certification effort and post-release maintenance
costs. Lower costs and faster development are further aided by the AC500-S
safety programming editor's support for the well-known PLCopen Safety
Library - which includes all the standardized function blocks used in safety
applications such as E-Stop, Mode Selector, Two-Hand-Control, etc. AC500-S
additionally supports the entire range of IEC data types, giving programmers
much greater flexibility.
Unlike some safety PLCs on the market, ABB's AC500-S Safety PLC has a
separate safety processor. The Safety CPU can be configured to work even if
the non-safety processor is in STOP or maintenance mode, or during an online
change. The dual processor architecture means that users can easily upgrade
the performance of a safety PLC during its lifecycle by plugging in a faster
non-safety CPU module. ABB offers a choice of SIL3/PL e certified safety
I/O modules including digital input and outputs, and a dedicated analog
current input module covering the 0-20 mA (or 4-20 mA) range. The latter
module makes it possible to measure parameters such as pressure,
temperature, position and torque on applications directly - without any need
for A/D conversion or proprietary electronics. This can simplify the
implementation of a wide range of safety-related machinery control
applications such as braking systems in hoists and lifting equipment, to
positioning systems and temperature control on cranes, and selective
shutdown systems on wind power turbines.
To simplify system design, safety-related control modules may be installed
as part of the main PLC solution, or be sited in a remote I/O rack linked
using the PROFINET/PROFIsafe protocol. Network-connected control systems
like this save cabling and assembly costs, and avoid problems with
interference. Moreover, ABB's I/O modules include integral power supplies,
reducing hardware costs and space requirements compared to some other PLC
vendor approaches.
One other valuable option for safety related control system designers, is
the availability of safety PLC modules in ABB's renowned XC 'extreme
conditions' variants. This option allows users to configure functional
safety PLC solutions that are also ruggedized and suitable for operating in
harsh conditions and extreme climates - as are commonly found on crane,
winch and wind power applications for instance.
More information: www.abb.com/plc
Featured Product
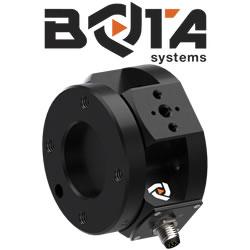
Bota Systems - The SensONE 6-axis force torque sensor for robots
Our Bota Systems force torque sensors, like the SensONE, are designed for collaborative and industrial robots. It enables human machine interaction, provides force, vision and inertia data and offers "plug and work" foll all platforms. The compact design is dustproof and water-resistant. The ISO 9409-1-50-4-M6 mounting flange makes integrating the SensONE sensor with robots extremely easy.
No adapter is needed, only fasteners! The SensONE sensor is a one of its kind product and the best solution for force feedback applications and collaborative robots at its price. The SensONE is available in two communication options and includes software integration with TwinCAT, ROS, LabVIEW and MATLAB®.