SERVO DRIVE RANGE COMBINES UNIVERSAL REAL-TIME ETHERNET CAPABILITY WITH SUPERLATIVE ECONOMY
--- advanced capability (real-time Ethernet, STO, digital encoder support..) at ~25% cost reduction! --- drives are also adaptable for custom applications and private label business
Braunschweig, Germany, November 26, 2013 --- At SPS/IPC/DRIVES, Metronix
with an outstanding new combination of capability and economy. Called
blueServo, the packaged drives combine a universal real-time Ethernet
capability with safe torque off functional safety and comprehensive encoder
interfacing capability - including the single-cable HIPERFACE DSL scheme.
All of these features and more have been integrated thanks to a brand new
hardware platform that has been designed-from-scratch to lower costs by
around 25%.
"Downwards price pressure is here to stay and with this brand new drive
family we began the design project with a goal of reducing hardware costs by
approximately 25% compared with current European drive ranges," says Frank
Essmann of Metronix. "We looked at the problem from all angles and as a
result the new drives have some interesting features that help lower costs.
Metronix is also known for its customization and private label capability,
and this too was part of the specification - allowing us to offer exciting
possibilities to OEMs with this technology."
Metronix will launch the new blueServo range with an initial choice of six
packaged, panel-mounting single-phase and three-phase drives offering
continuous output power ratings from 0.5 to 6 kVA. The hardware feature set
chosen for the new drives is a combination of the most-commonly required
features by Metronix's broad customer base, along with some brand new
capability.
The use of real-time Ethernet communications protocols is a major trend in
the industry and to meet this demand Metronix has embedded a universal
Ethernet capability into the drive. It allows the drive to be used in
automation systems employing EtherCAT, PROFINET, Sercos III or Ethernet/IP
protocols for example, in addition to the commonly-used CANopen network
interface.
A broad encoder interfacing capability is another major element of the servo
drive family. Metronix blueServo drives allow connection to resolvers,
analog/digital incremental encoders, and single/multiturn absolute encoders
such as HIPERFACE or EnDat. The drives also support the digital HIPERFACE
DSL interface - which allows automation engineers to cut system building
costs substantially by using only a single cable connection between drive
and motor.
Enhanced machine safety is another important trend, and Metronix has
included support for Safe Torque Off (STO) functional safety in the new
drives. This is designed to meet Category 4/PLe according to EN 13849-1 -
the maximum rating achievable single-axis safety level in this category.
Further features include an integral line filter and brake resistors - a
typical characteristic of Metronix drives - allowing blueServo to offer a
standalone and ready-to-use solution for many common automation
applications. A powerful and easy to use Windows-based software tool for
parameterizing and analyzing the new drives is additionally available.
A key element of the new drive design is its low cost. This has been
achieved by several factors. These include a carefully selected feature set
that satisfies a large proportion of applications, and the implementation of
these features directly in the embedded system rather than by means of more
versatile, but more expensive techniques such as expansion slots - as used
on some of Metronix's existing drive families. Metronix also increased the
flexibility of the drive - without increasing costs - by partitioning the
electronics design across two boards to reduce printed circuit layers and
allow single-sided component mounting, and assembly/manufacture using simple
processes. The two-board design serves to support Metronix's large custom
drive business. One common request for example is to integrate an OEM's
application-specific drive control electronics with Metronix's power stage -
this is easily accommodated with the carefully-partitioned blueServo design.
"With blueServo we have created a drive that is designed and built to the
most demanding professional standards, yet is also extremely price
competitive," adds Frank Essmann. "We believe that machine and automation
builders can rely on it to help make their future generations of equipment
as price competitive as equipment sourced from any world region - including
low-wage-cost economies."
Metronix will deliver engineering development samples of blueServo in Q1,
2014, and plans to start volume production of the new range towards the end
of Q2, 2014.
Metronix has been producing motion control technology for industrial
machines and automotive applications for over 30 years. Its product range
includes smart servo drives with integrated positioning capability, plus
motion controllers and accessories that provide cost-effective solutions for
multi-axis motion control and automation, and decentralized machine control
requirements. A key feature of Metronix's motion products is their rich
networking and encoder interfacing capability, which ensures that drives can
be integrated easily into virtually any industrial system or machine - even
if an OEM has custom PLC or control hardware. This feature is highly valued
by many OEMs as it allows them to create and continue developing innovative
brands of machine offering unique features. Metronix complements this
capability with what is probably the most sophisticated and capable custom
drive engineering service on the market today. Motion control products
designed by Metronix are marketed under its own brand, and in custom forms
by a number of well known industrial OEMs.
The company additionally makes geophysical instruments and customer-specific
digital controls for measurement and control applications. Metronix is part
of the Apex Tool Group, headquartered in Sparks, Maryland, USA. The Apex
Tool Group has more than 7,600 employees in over 30 countries. Metronix's
design and manufacturing facility is located in Braunschweig, Germany.
Featured Product
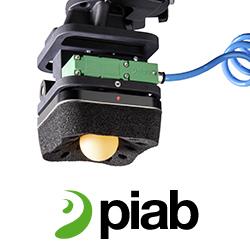
The piCOBOT Electric vacuum generator
Fully electric, slim design and absence of air-tubing and cabling. The new piCOBOT® Electric heads towards another success for Piab's piCOBOT® program. A secondary effect of these achievements is the absence of entangling air tubing and cabling. It simplifies the installation, and as the new piCOBOT® Electric only needs a single connection on the cobot arm, the clean set-up allows a completely unrestricted movement. The new piCOBOT® Electric package will contain plug & play software to fit UR e-series cobots, but many other useful adaptations will be introduced in the coming year