EuroMold 2013: New Plastic System EOS P 396 Reduces Secondary Processing Times by up to 60 Percent
Significantly reduced costs per job, increased production efficiency, greater process stability and construction capacity, all with consistent component characteristics
FRANKFURT, Germany--EOS, the German market and technology leader for design-driven, integrated e-Manufacturing solutions for Additive Manufacturing (AM), introduced the EOS P 396 production system for the manufacture of plastic parts at this year's EuroMold (December 3-6). The successor model to the successful EOSINT P 395 that is already established in the market offers a multiplicity of features that comprehensively meet the growing demand for increased manufacturing efficiency, process stability, and building capacity. The latest CO2-laser generation and a completely revised temperature regulation enable double-digit increases in productivity. Global distribution of the EOS P 396 begins in April 2014.
"With the presentation of the EOS P 396 at EuroMold we are sustaining a leading role in plastics-based Additive Manufacturing, a position that stands alongside our metals technology. The EOS P 396 seamlessly supersedes our highly successful EOSINT P 395 model in the mid-frame segment. We have made a number of improvements that allow our customers to produce both plastic prototypes and serial parts with an even higher quality and cost efficiency," explains Adrian Keppler, Managing Director at EOS.
Reducing production costs and timeframes
With the unveiling of the new EOS P 396 the company has introduced a number of improvements. Dependent on the fill level and spectrum of parts, potential increases in manufacturing efficiency of up to 30 percent are possible. A reduction of the secondary processing times is achieved by a number of features, including a new point pyrometer and a low wearing, high speed recoater. Primary processing times are shortened thanks to the introduction of a new and significantly higher performance laser. The energy and material consumption of the system per manufactured component also has been further improved. This results in a reduction in operations costs and in an optimized product carbon footprint (per part). When the system is viewed in combination with highly economical materials such as PrimePart® PLUS, then combined cost savings of some 30 percent per part are achievable in relation to the system's predecessor.
A newly integrated point pyrometer continually measures the temperature of the powder surface for coating with a high degree of precision. This enables secondary processing times to be further reduced leading to a corresponding increase in productivity. Furthermore, this feature forms the basis for a more stable regulation of the production process, thereby improving process reliability. With the availability of Release 3.7 of the EOS process-software (PSW) at the start of series production, the functional scope is once again expanded, and furthermore the Windows 7 operating system supported. The building capacity of the EOS P 396 is in line with that of its predecessor, at 340 x 340 x 600 mm.
With the introduction of the EOS P 396, the plastic materials PA 2200 and PrimePart® PLUS (PA 2221) will also be commercially available for this system from April 2014. Further materials will follow over several stages, until all of the powders approved for the predecessor system are available.
About EOS
Founded in 1989 and headquartered in Germany, EOS is the technology and market leader for design-driven, integrated e-Manufacturing solutions for Additive Manufacturing (AM), an industrial 3D printing process. As an industrial manufacturing process, AM allows for the fast and flexible production of high-end parts based on 3D CAD data at a repeatable industry level of quality--with freedom of design, optimization of part structures and other design benefits. For more information visit www.eos.info.
Featured Product
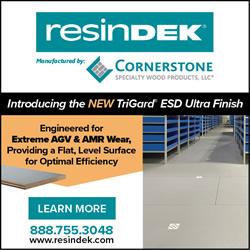