Solid Concepts' 3D Printing Enhances 737 UAV
Georgia based company Area-I turned to Solid Concept's manufacturing solutions for their 737 scale model unmanned aerial vehicle (UAV) PTERA. PTERA's purpose is to provide a low-cost testing platform for new control and monitoring technologies.
Valencia, CA December 17, 2013
Solid Concepts provided multiple Selective Laser Sintered (SLS) 3D Printed components for Area-I's scale 737 model reducing time and assembly work for the engineering team at Area-I. The 3D Printed components for PTERA, which stands for Prototype Technology Evaluation Research Aircraft, include fuel tank, ailerons, control surfaces and flaps.
SLS 3D Printing works via a bed of powdered nylon and a CO2 laser which sinters the nylon in consecutive layers until a final product is achieved. Originally, Area-I hand-built the ailerons for PTERA; however, "before we had Solid Concepts build the ailerons out of SLS it took us 24 man-hours," says CEO of Area-I Dr. Nick Alley. "When we grew the ailerons with SLS, they were designed, built and assembled on PTERA within three days. SLS is easy to work with, installs quickly, is efficient and, from an aesthetic standpoint, produces parts that are gorgeous." The control surfaces incorporated all hinges and mounting structures into the initial build, eliminating costly and time-consuming post-processing as well as eliminating the extra weight of bulky additives for attaching features via traditional methods.
"Additive manufacturing has completely changed the way we design aircraft," says Alley. "We used to shy away from certain complex designs, opting for structures that are more basic. With additive manufacturing, we can now create even the most complicated designs. It has completely opened up design capabilities that we would not be able to make with any other manufacturing method."
PTERA's fuel tank also benefitted from SLS, with anti-slosh baffles designed and built directly into the inside of the tank which significantly aided in the balance and flight length of PTERA. "With the latest build technologies available, we're now able to get parts for our aircraft faster than ever before," says Alley. Normally fuel tanks are built out of steel or other metals, but Area-I was able to 3D Print PTERA's tank with SLS and coat the inside of the tank with a special sealant resulting in a much faster turnaround and far lighter fuel tank.
Solid Concepts conducted an exclusive interview with CEO Nick Alley at Area-I's headquarters in Georgia. The flight of PTERA and interview with the engineers at Area-I can be viewed here: https://www.youtube.com/watch?v=8xPYMDXGyBM&feature=youtu.be.
About Solid Concepts
Solid Concepts Inc. provides custom manufacturing solutions via additive manufacturing, rapid prototyping, CNC machining, cast urethanes, injection molding and tooling. Since 1991, Solid Concepts has provided engineering expertise from multiple fields to bring success to new products in the aerospace, medical, consumer product industries and more. Capabilities in PolyJet, Stereolithography (SLA), Plastic and Metal Laser Sintering (SLS & DMLS), Fused Deposition Modeling (FDM), QuantumCast™ Cast Urethanes, CNC, Tooling and Injection Molding allow for low to high volume production of plastics, urethanes, and metals directly from design data, resulting in significant time and cost savings. ISO 9001 and AS9100 certifications.
Featured Product
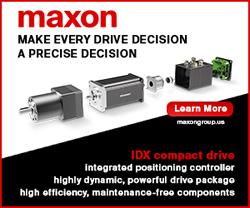
The maxon IDX Compact Drive with Integrated Positioning Controller
The compact brushless EC-i motor combined with an EPOS4 positioning controller delivers a highly dynamic, powerful drive package with field-oriented control (FOC), high efficiency, and maintenance-free components in a high-quality industrial housing. The maxon IDX drives are suitable for use across the entire speed range (from standstill to maximum speed) and have an extremely high overload capability. Together with a positioning controller, the integrated sensor (single turn) enables absolute positioning.