KUKA Systems Commercializes New PULSE Line Technology
PULSE technology is extremely fast and flexible – 30% faster than conventional friction-based transfer systems.
Sterling Heights, MI| Augsburg, Germany - KUKA Systems North America LLC has announced the commercial launch of its new, ground-breaking PULSE carrier conveyance system for automotive car body assembly lines. PULSE, a patent-pending concept developed by KUKA Systems in the US, utilizes linear synchronous motor technology provided by MagneMotion of Devens, MA to move body sections through robotic work stations along assembly lines as joining and other functions are performed.
PULSE technology is extremely fast and flexible - 30% faster than conventional friction-based transfer systems. The speed boost allows for greater use of other process equipment, which in turn allows for a reduction in the footprint of the overall production line. With its solid state linear motors, a PULSE line has fewer wear components - including sensors, connectors and cables - that require maintenance or can fail, causing unscheduled downtime. And it has a major safety advantage, too; it can stop much faster than conventional systems.
A PULSE line can be configured to handle up to four models. It costs much less to add a second model-handling capability than it would with a conventional transfer system. PULSE also has great design flexibility; it can be adapted to the physical conditions at each assembly plant.
KUKA Systems began developing PULSE as an in-house research and development project in 2009. It entered the laboratory testing phase in 2013, and is now being commercialized.
"PULSE offers a very strong business case and were sure it will become a preferred technology for our customers in future plant retoolings", says Kevin J. Laurence, Advanced Engineering Manager at KUKA Systems North America, who came up with the original technology concept.
About KUKA Systems
KUKA Systems, part of Germany-based KUKA AG, is an international supplier of engineering services and flexible automation systems for the Automotive, Aerospace, Energy, and Industrial Solutions segments. Some 5,800 employees worldwide work on ideas, concepts and solutions for automated production and the provision of products and services for virtually all tasks in the industrial processing of metallic and non-metallic materials. The range is presented and marketed internationally via subsidiaries and sales offices in Europe, America and Asia. KUKA Systems had sales revenues of 1.28 billion euros for the 2014 business year. KUKA Systems North America LLC, based in Sterling Heights MI, is responsible for the North American business and the worldwide aerospace group.
Featured Product
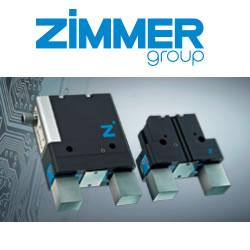