Pack Expo - Universal Robots Raises the Bar on Collaborative Robotics at Pack Expo
The Danish robot manufacturer, that pioneered the safety systems of collaborative robots, showcases product features that help lower the automation barrier, making a robot truly collaborative. The features on display at Pack Expo 2015 in Las Vegas are portability, ease of use, and integration.
EAST SETAUKET, N.Y.-- Having a built-in safety system that enables a robot to stop operating if it comes into contact with an employee, has long been the defining feature of collaborative robots. Universal Robots is now expanding the term "collaborative" to include user-friendliness, re-deployability and simple setup.
"Weve been the frontrunners of collaborative robotics since the term was coined. While safety is imperative, we believe that being collaborative is just as much about accessibility; placing robots within reach of manufacturers regarding automation as too costly and complex," says Scott Mabie, General Manager of Universal Robots Americas division.
Universal Robots will showcase its complete line of collaborative robots; the UR3, the UR5 and the UR10 robot arms named after their payload in kilos, at Booth #S-8072 at Pack Expo 2015 in Las Vegas, September 28 - 30.
The Universal Robot arms support Flexible Manufacturing initiatives. Whether it is adjusting to seasonal lines, or to variation in co-packing lines, employees can teach the robot new moves as production schedules change. Using the teach pendant and moving the robotic arm, human coworkers simply change the movements of the UR robot without having to code or reprogram.
"We see a collaborative robot as a tool on demand as needed - one that can quickly be transitioned between packaging tasks to streamline production planning. Flexibility in manufacturing involves ability to deal with variation in volumes, design and material handling as well as variations in the process sequences," says Mabie.
Unlike investments in traditional robotic cells that are caged, pre-programmed and designed for a single purpose, the multi-purpose UR robot offers a lower threshold for investment and offers more possibilities over the life of the investment. The robot arms can be plugged directly into a wall outlet and are so easy to program and set up that the typical "out of box experience" is less than an hour.
At Johnson & Johnsons plant, a UR5 robot has significantly optimized the packaging process of shampoos and skincare products. The robot arm works 24/7, picking up three bottles simultaneously from the production line every 2.5 seconds, orientates them, and places them in the packing machine. While manual labor can handle 45 bottles per minute, the UR robot handles 70. The flexible robot can pick up various types and sizes of bottles. Any employee can quickly reprogram the robot for new tasks by using the arrow keys on the touch screen tablet or by simply grabbing the robot arm showing it the desired path of movement. This has saved Johnson & Johnson the cost of hiring external programmers.
The collaborative robots innovative force- sensing technology enables the robot to automatically stop operating if it comes into contact with an employee, enabling human-robot interaction. This is the case at Scandinavian Tobacco Company, where a UR5 robot now works directly alongside employees handling the lids for tobacco tins. The robot spares employees from having to make back-breaking repeated movements and has freed 1-2 people that previously performed the packaging by hand. There was no room to fence off the robot in the setup at the factory, Scandinavian Tobacco chose Universal Robots because the UR robots were the only ones approved for operation without safety guarding, simplifying setup and costs significantly.
A Universal Robot can interface seamlessly with external machinery. At Orkla Foods, the robot works independently packing vanilla cream bags into cartons but is part of a network with a carton erector, a carton sealer and is fed by a filling machine. The payback period for the UR10 robot installed at Orkla was only six months - which is not unusual, the average ROI for a Universal Robot is 195 days, the fastest payback in the industry.
About Universal Robots
Universal Robots is a result of many years of intensive research in robotics. The product portfolio includes the collaborative UR3, UR5 and UR10 robot arms named after their payloads in kilos. Since the first UR robot entered the market in December 2008, the company has seen substantial growth with the user-friendly robots now being sold in more than 50 countries worldwide. Average payback period for UR robots is the fastest in the industry with only 195 days. The company is headquartered in Odense, Denmark, where all development and production is carried out. www.universal-robots.com
Featured Product
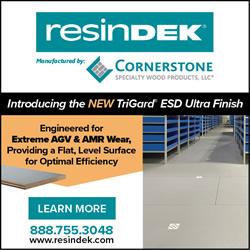