Universal Robots to build architectural scale pavilion in direct collaboration with attendees at Autodesk University
The Autodesk University conference merges traditional craftsmanship with computational design and manufacturing processes as the Hive Pavilion takes shape during the three day event in Las Vegas December 1-3. The Pavilion will be designed and built with the collaborative Universal Robots working in tandem with attendees, showcasing the future of digital construction and human-robot collaboration.
East Setauket, NY, November 24 2015: "The Future of Making Things" is the theme of this years Autodesk University conference featuring the Hive Pavilion as a very hands-on example. The Pavilion is a result of Autodesk teams working with the Institute of Computational Design at the University of Stuttgart, offering attendees a unique opportunity to explore how robots become humans intuitive tool.
The collaborative robot arms from Universal Robots were chosen for this project because of their combination of safety, performance, ease of use and portability.
"These robots are ideally suited to this type of one-off project where the most efficient approach is for robots to be used as augmentation of peoples abilities, adding strength, precision, and repeatability. This project will help communicate our belief that interesting and novel use of collaborative robots will have a significant impact on our major manufacturing and construction industry partners," says David Thomasson, Principal Research Engineer at Autodesk.
In contrast to traditional industrial robots that stay hardwired inside safety enclosures, collaborative robots belong to a new breed of robots that can work flexibly directly alongside humans due to the built-in safety system that automatically stops the robot arms operation if it encounters objects or people while moving.
General Manager of Universal Robots Americas Division, Scott Mabie, sees the Hive Pavilion as a perfect showcase of humans and robots working together safely and dynamically:
"Each unique building block in the Pavilion will be created in a process neither robot or human could have produced alone. A synergetic scenario we now see replicated in the manufacturing industries that have started to embrace collaborative robots."
The Hive Pavilion will be built at "winding stations" equipped with a UR robot and a spool of fiber where attendees fabricate unique tensegrity nodes out of irregularly sized pieces of bamboo and fibers. Participants help the robot load three random pieces of bamboo, fasten specialized tips to each end, and measure the length and configuration of the pieces. The UR robot then generates the necessary movement sequence to hook the fiber on the tips, creating a unique tensegrity element.
Next step is for the human to remove the element and bring it to the assembly site, where the pavilion will be built top-down and lifted as each row is completed, so the assembly occurs at standing height. The design algorithm accounts for each new piece as it is fabricated and identifies the optimal placement. LEDs embedded in connecting hardware indicate the correct orientation of each new addition. The goal is for users to experience a seamless integration between robotic manufacturing, wearables, RFID tracking, and intelligence embedded in the building pieces
Discussion about the pavilion, human/robot collaboration, and the future of construction will be housed in the Autodesk University App.
About Universal Robots
Universal Robots pioneered collaborative robotics and remains a market leader and first mover within this emerging technology. The product portfolio includes the collaborative UR3, UR5 and UR10 robot arms named after their payloads in kilos. Since the first UR robot entered the market in December 2008, the company has seen substantial growth with the user-friendly cobots now being sold in more than 50 countries worldwide. Average payback period for UR robots is the fastest in the industry with only 195 days. The company is headquartered in Odense, Denmark, where all development and production is carried out. U.S. offices are located in New York, Ann Arbor, Los Angeles and Dallas.
Featured Product
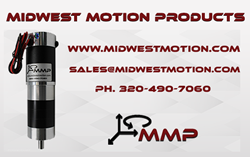