ROBUST SMALL ROBOT FROM KUKA OPTIMALLY UTILIZES THE CAPACITY OF THE TOOL GRINDING MACHINE
While smoothly loading the grinding center of type UW I F at SAACKE, the KUKA small robot KR AGILUS WP (waterproof) ensures fast and precise transfer and unloading of workpieces.
Robot-based automation of the grinding process shortens the changing times for workpieces
The KR AGILUS WP removes the workpiece to be machined - an indexable insert or a shank tool - from a pallet in the robot cell and sets it down on a pin. Following this, it positions the workpiece in front of the door of the cell, which opens automatically. The robot arm then moves through the open door to the grinding device outside of the robot cell, where a machined workpiece is already located during ongoing operation. Using the second gripper, the KR AGILUS WP picks up this workpiece and then loads the new workpiece with a quick rotation of the gripper arm. Machining of the new workpiece with the type UW I F tool grinding machine begins. In the meantime, the robot arm returns to the robot cell. There, the machined workpiece is cleaned in the blowing station and then set down again on the pallet before the robot grips the next workpiece to be ground and the work sequence is repeated from the beginning.
Waterproof KUKA small robot also works precisely under intensive outdoor production conditions
The KUKAsmall robot works extremely precisely for the optimal handling of indexable inserts weighing just a few grams as well as for shank tools of up to 2.5 kg. The robot used to achieve this at SAACKE is the KR 6 R900 sixx WP robot - the most robust waterproof variant from the KR AGILUS series. It features stable stainless steel covers, resistant surface treatment and additional seals in the interior, enabling it to be used in a machine tool environment. This prevents ingress of cooling lubricant and grinding oil into the robot. As a result, the robot fully meets SAACKEs expectations. Thanks to a shortened cut-to-cut time, the capacity utilization of the machine has been substantially improved. Furthermore, the reliable procedure has enabled the operator control requirements of the machine to be simplified to a great extent.
Featured Product
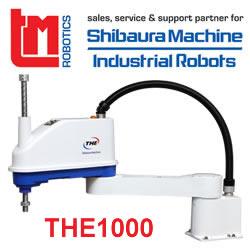
TM Robotics - Shibaura Machine THE SCARA range
The THE range from Shibaura Machine is an extensive line up of SCARA robots. Available in four arm lengths THE400 (400mm), THE600 (600mm) and the most recent THE800 (800mm) and THE1000 (1000mm), this range is suitable for assembly, handling, inspection and pick and place processes in varied industrial applications. The THE1000 boasts a 20kg payload capacity and an impressive 0.44 second cycle time, providing high speeds for processes with large components. In fact, the range has been recognised for as the price-to-performance leader compared to other SCARA models in its price range due to its impressive speed versus payload capacity.