CWIEME Chicago 2017: Day 1
CWIEME Chicago — the world's leading exhibition for the transformer and electric motor manufacturing industries — welcomed international visitors for three days of discovering new products, technologies and the latest industry trends, plus networking.
CWIEME Chicago, which runs from Oct. 3 through 5, kicked off with a CWIEME Technical Program that provided a global overview of electric motors and automation opportunities in electric machine production. Global economic growth picked up from 2.5% in 2016, to 3.1% in 2017, and is expected to increase slightly to 3.2% in 2018, led by the United States and emerging markets, according to IHS Markit, a London-based market research company. While motor and drive suppliers are still enduring tough times, strong opportunities exist within the construction, commercial HVAC and water industries, according to IHS Markit.
When it comes to electric motors, IHS expects increased supply chain costs to be passed on to customers starting in 2018. But with consumers still remaining cost-conscious, leading motor suppliers are offering broader solutions where they are not just offering products but also solutions and inserting themselves in customers supply chain to better understand customer needs.
"Manufacturers are focusing on smart solutions and applications with design changes around sensors, and the ability to track vibration and temperature on internal motor components," said Preston Reine, group manager, IHS Markit, during the shows first seminar. "We are seeing a move away from preventative maintenance to prescriptive maintenance and being able to track that."
As for technology changes in manufacturing and machinery, IHS reports a shift toward Internet of Things (IoT), where there is open access to data from one or more monitoring and control systems by third-party applications to provide unique, additional value to stakeholders.
"Efficiency will improve, but IoT has brought forth other solutions that can dwarf the benefits of simply buying one efficient product," Reine said. "Full solution offerings continue to be a better business model than niche product manufacturing, and uptime as a service is likely the future."
BMW i3
As the automotive industry is producing more and more new hybrid electrical vehicles (HEV) and electric vehicles (EV), James Hendershot, president and lifetime IEEEE Fellow with Motorsolver, discussed how BMW i3 electric traction drive was designed to have a high saliency ratio, which corresponds to a high reluctance torque component as a consequence. The BMW i3 traction motor was also designed to have a very sinusoidal back electric motor force, which is rare in motor designs.
"Their goal was to use reluctance technology to get some reluctance torque out of the machine without using a lot of magnets because magnets were expensive when they first started designing," Hendershot said.
Magnetic discovery
During an afternoon seminar, Dr. Wen Hao Cheng, director and chief scientist at Shenzen Radimag Magnets, a Shenzhen, China-based company specializing in manufacturing radially ring magnet technology, discussed the benefits of radially ring magnets. The companys product received two patents in China and is used in applications ranging from coil pump motors to electronic power steering motors.
Cheng says with their inventions, the orientation field is limited at a small part of the die cavity and the orientation field also doesnt cross the total die cavity—it crosses only half the cavity.
"Our patented inventions provide advantages such as making it easy to achieve 1 to 1.5 Tesla orientation field, and, in theory, the outer diameter and height of the radial ring can be made without limitation," Cheng said. "Plus, production is very efficient—it takes only about 40 seconds to press a ring."
Featured Product
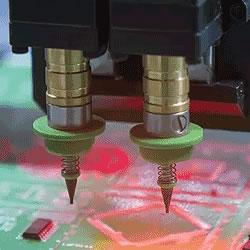