CoaXPress 2.0: Twice the Speed, Lower Costs, Greater Flexibility
With prices dropping for single-link CXP cameras and frame grabbers, CoaXPress has positioned itself to move into mainstream applications that were once the province of Camera Link and GigE Vision.
As price pressures increase due to global competitiveness, productivity remains the key focus for successful manufacturers with 100% quality assurance its Holy Grail. Machine vision, with its ability to pinpoint the most minute defect or flaw, has long been considered a means for achieving higher quality and therefore, greater productivity. The CoaXPress standard has made this promise a reality for larger manufacturers across a spectrum of industries in high-end inspection applications.
Launched less than a decade ago, CoaXPress has carved out a market niche on the quality-sensitive, high-speed end of the machine vision spectrum. With prices dropping for single-link CXP cameras and frame grabbers, CoaXPress has positioned itself to move into mainstream applications that were once the province of Camera Link and GigE Vision.
CoaXPress or "CXP" has become a leading standard for high-end machine vision, and in such diverse fields as life sciences, security, and defense where use of coaxial cable is prevalent. CXP delivers high-speed asymmetric serial data over a maximum 100-meters of standard 75-ohm coaxial cable. It supports speeds up to 6.25Gbps, although the use of multiple cables allows scaling of bandwidth to meet the needs of a specific application. Additionally, CXP supplies power to the camera via PoCXP, plus controls the camera - all over the same coaxial cable.
One of the driving forces behind CXP's rapid adoption within the machine vision ecosystem is that it allows for the re-purposing of coaxial cable in existing analog systems, therefore providing a cost-effective, trouble-free migration to faster, higher resolution digital processing. A user can replace just their analog camera and frame grabber to gain CoaXPress transmission rates. CXP's additional bandwidth gives virtually any vision application the firepower to handle faster production runs and perform finer inspections.
RAPID EVOLUTION
Even by machine vision standards, CoaXPress has evolved rapidly. In 2015 the successor of CoaXPress 1.1.1 was launched: CoaXPress 1.2. Along with technical clarifications and minor corrections of the specification, CoaXPress 1.2 introduced screw-on coupling DIN connectors for needed robustness against shocks and vibration, especially for in-vehicle systems.
The next generation of CXP, CoaXPress 2.0, promises much more. The final draft of CoaXPress 2.0 will be ready by the fourth quarter of 2017 with the first certified products expected at the end of this year or early 2018. Central to this updated standard is the unprecedented speed to achieve blazingly fast frame rates and larger camera resolutions. CoaXPress 2.0 extends data transfer rates to an unheard of 10 Gbit/s (CXP-10) and 12.5 Gbit/s (CXP-12) per connection from the existing standard's 6.25 Gbit/s maximum data transfer rate support.
Consider this: With only two cables and CXP-12 connections, maximum data transfer rate is 25 Gbps, or 2.5 GByte/s. That will operate a 10-bit 12-megapixel area-scan sensor at more than 150 images per second, or an 8-bit 16k line-scan sensor at 150 thousand lines/s. Because the amount of data may exceed the host PC's processing power, CoaXPress 2.0 supports the distributing of camera data to several PCs in parallel, permitting them to delegate the workload. Uplink speed is doubled for both CXP-10 and CXP-12, making it possible for trigger rates exceeding 500kHz without a dedicated high speed uplink cable.
Greater speed translates into enhanced flexibility in system design, and in the reduction of total system costs. For example, by requiring only one CXP-12 connection instead of two CXP-6 connections, fewer cables are needed. Or consider the widely-used "Camera Link Full" configuration. Full configuration of Camera Link provides a bandwidth of only 850MB/s. CXP-10 exceeds that requirement, allowing for the swapping out of two complex and expensive Camera Link cables with a single coaxial cable. It will also reduce the number of PCIe slots needed for frame grabbers in multiple camera applications while helping to lower the cost of such accessories as CXP repeaters, split boxes, and cables.
One of the biggest challenges in developing CoaXPress 2.0 requirements was doubling the bandwidth yet maintaining its support of long coaxial cable runs. Amazingly, the 12.5 Gbps bandwidth does not limit CXP's 100-meter cable length, as was the case with other high transfer speed standards, such as USB3 that relies on passive cable lengths of two meters or less. CoaXPress 2.0 perserves the 100-meter maximum length without deploying repeaters that can negatively impact signal integrity.
In recognition of the global trend and increasing adoption of 3D vision techniques, CoaXPress 2.0 has extensions for 3D imaging. This addition to the standard is especially timely given that the global 3D vision market is expected to be valued at USD $2.13 billion by 2022. Growth is attributed to the increasing applications of 3D machine vision in the automotive and electronics industries.
Yet another new feature to CoaXPress 2.0 is Forward Error Correction or FEC. FEC is a way to control errors in data transmission from the camera to the frame grabber. This is achieved by the camera sending redundant data and the frame grabber recognizing only that portion that conforms to protocol. FEC does not require handshaking between a camera and frame grabber, so data can be sent to many PCs for processing simultaneously from a single camera.
SINGLE-LINK CXP AS A COMPETITIVE ADVANTAGE
Today, a new generation of CXP frame grabbers and single-link cameras is bringing CoaXPress to smaller, more cost-sensitive manufacturers.
CoaXPress single-link cameras, which traditionally were power hungry, large and expensive, are now more compact, cooler in operation, and affordable. Some of these cameras are as small as 29mm cubes. While compact, they will still transmit up to 6.25 Gb/S worth of data over the link. At this speed the system can deliver 2MP images at 300 FPS, almost twice the real world data rate of USB3 Vision cameras and significantly quicker than the latest GigE Vision cameras.
To take advantage of these new cameras' performance, low cost single-link CoaXPress frame grabbers such as the BitFlow Axion have been launched that provide all the convenience of a GigE Vision or USB3 Vision camera system. A single-link CXP camera and frame grabber can compete on price while exceeding the cable lengths in many cases. In addition, this combination can provide a host of Machine Vision features missing from GigE Vision or USB3 Vision camera systems such as triggers, encoders, strobe, waveform generators, and quadrature encoder support.
Another advantage this low-cost, high-performance single-link CXP solution over a GigE Vision or USB3 Vision is that all of the hardware and software components of the capture system are sourced from one manufacturer, instead of separate blocks from different manufacturers including Intel and Microsoft. The frame grabber company writes every line of software and firmware designed for their own hardware. In the event of a problem the frame grabber company can comprehensively support the customer and resolve the issue in a short amount of time.
CONCLUSION
To satisfy the high-end market the soon-to-be approved CoaXPress 2.0 standard will double the current 6.25 Gbps image data transfer rate to 12.5 Gbps over a single coaxial cable up to 100-meters in length from camera to frame grabber. Now, more than ever, CoaXPress is the right network interface for successful machine vision applications to help companies achieve the extremely high levels of quality and productivity needed to gain a competitive edge in the global economy.
For more information, please call 781-932-2900 or visit www.bitflow.com.
Featured Product
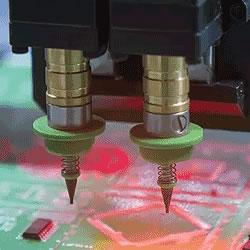