OCTOPUZ Programs Panasonic Welding Robot at Accumetal Manufacturing Inc.
After many years of manual welding and programming a Panasonic welding cell, Accumetal Manufacturing Inc. looked at OCTOPUZ for Offline Programming.
Just like there are a multitude of robot brands in the industrial robotics industry, there are also a multitude of options for programming. Manual programming, OEM specific software and third party offline programming software are some of the different approaches.
OCTOPUZ Offline Programming and Simulation Software is a third-party software solution for programming industrial robots on your PC. OCTOPUZ has the ability to program multiple robot brands, in multiple configurations, for a multitude of applications, all together in one cell.
Panasonic robots, a brand that is growing in popularity in the industry, use a unique code structure from the majority of other robot brands. Contrary to popular belief OCTOPUZ includes all the tools necessary to program Panasonic robots in an easy, fluid and efficient way.
Accumetal Manufacturing Inc., based in Stratford Ontario, is a high mix, fabrication and welded components manufacturer. They manufacture a large number of structural components for the off-road mining industry. After many years of manual welding and manual programming on their Panasonic welding cell the volume of work increased and triggered the need to look at more automation to get some relief for their welders. This is where OCTOPUZ stepped in.
We Interviewed Aaron DeJong, Welding Technologist at Accumetal Manufacturing, who shared with us how he first heard of OCTOPUZ and what the sales process was like.
"Back when I was in College one of my classmates did a presentation on the OCTOPUZ Offline Programming Software, a new technology and solution for robotic welding. Shortly after I joined Accumetal, a need for this type of software was identified and I reached out to OCTOPUZ to set up a sales meeting. Shortly thereafter, I was given a demo copy of version 1.7 just to play and experiment with. The sales process was very professional, they answered all our questions and made sure if there were any concerns we could reach out to them." - Aaron DeJong
Early this year, Accumetal elected to invest in a new Panasonic robotic welding system. This new system was paired with OCTOPUZ to not only be able to meet the new demand but to also become more profitable by reducing lead times and increasing capacity.
"We only have a base of 6-7 customers that we usually work with, since they are regular customers, with the new robot and the offline programming software we can easily shift production to our robot for the items that the regular customers are consistently ordering. This allows us to be able to take on more skews from the same customer." - Aaron DeJong
In addition to solving the problem of increased demand, OCTOPUZ was also able to help Accumetal reduce their programming time and robot downtime. Using OCTOPUZ, Accumetal is able to program the path beforehand, offline, only having to do touch ups and adjustments on the floor as needed.
"What we saw was that with our older robot, if it was constantly working, it was great for us. The problem is: what if we have something new that we want to put on there? Then we have to stop production. This way, with both the old cell and the new cell that we bought, we can generate the paths offline. That should save our programming time and reduce downtime." - Aaron DeJong
A common question regarding robotic programming is "How much time will it actually save me?". This is a tough question as it greatly depends on the size and complexity of the part. For Accumetal, it depends on not only the size but the number and the complexity of the welds.
"Without Offline Programming, I would say, depending on the part, you are talking anything from a full-day to two full-days, depending on complexity. With OCTOPUZ, I would say that we are down to half-a-day to a day for an acceptable first off, and then from there its fine tuning it. I would say we have essentially cut the initial programming time in half." - Aaron DeJong
WHY OCTOPUZ?
As mentioned at the beginning there are many robotic programming software options. So, what makes OCTOPUZ different? Aside from being able to program multiple robots of different brands at the same time, performing many different applications, we truly believe our customer care and support is what makes us different.
For Accumetal, it was our locality and ability to go above and beyond.
"OCTOPUZ is really local, being based in Stratford and OCTOPUZ in Waterloo it takes an hour for the team to get here, if the OCTOPUZ team needed to come onsite it wasnt a really big hassle, if we needed support and we needed them on site they are only an hour away." - Aaron DeJong
OCTOPUZ also did some standard development for Accumetal, specifically regarding Panasonic support. This involved giving them the ability to easily convert the OCTOPUZ code into Panasonic specific code. Once the file is loaded onto the robot, it can immediately begin running the program, with no adjustments required.
"Kudos to you applications team, they managed to map out exactly what we had to do and they made a very easy to follow video. To post the code and to convert it into Panasonic code was very simple!" - Aaron DeJong
OCTOPUZ FOR PANASONIC ROBOTS
Welding with OCTOPUZ is easy! To import CAD, simply drag and drop your CAD Models. To create a weld, select a wall and floor and click generate weld and just like that your weld is programmed.
Programming Panasonic Robots is just as simple with OCTOPUZ. At Accumetal Manufacturing they employed the generate weld paths and quickweld features with their Panasonic Robot, with the capabilities to do touch sensing, weave welding, through arc seam tracking, touch before welds, and stitch welding with OCTOPUZ.
Panasonic robot code is very different from some of the other robot code structures. With a click of a button OCTOPUZ code can be converted into Panasonic code resulting in a fluid process for the end user.
CONSIDERING AN OFFLINE ROBOTIC PROGRAMMING SOLUTION?
If you are considering automation for your facilities paired with Offline Programming capabilities contact us to learn more about what is possible with OCTOPUZ. We also have a list of integrators we can put you in-touch with if you are looking for help getting an entire robotic solution implemented.
When Aaron from Accumetal Manufacturing was consulted for advice on automation he suggested:
"My advice is, you need to consider the volumes that you are seeing now, and you need to look at the forecasts of what is coming in the future. If you are seeing medium to low volumes of new or existing parts and you are looking to automate some of that then OCTOPUZ is definitely a good fit for you." - Aaron DeJong
The OCTOPUZ team very grateful to Accumetal Manufacturing and Aaron DeJong for working with us closely to further develop the OCTOPUZ for Panasonic features and allowing us to showcase the fluid solution OCTOPUZ can offer with Panasonic robots.
To conclude Aaron mentioned:
"It has been a pleasure working with the team at OCTOPUZ especially since this is the first time that OCTOPUZ has integrated with a Panasonic robot. It was great to be able to suggest features and help develop that solution for the welding industry. The applications team is very knowledgeable, and they strive to make the solution the best it can be for every application. The support behind the product is amazing! If I have a problem I submit a request and they get back to me as soon as they can and usually when they get back to me they have an answer that I can implement myself. I look forward to working with OCTOPUZ in the future on any additional features and capabilities for Panasonic." - Aaron DeJong
Featured Product
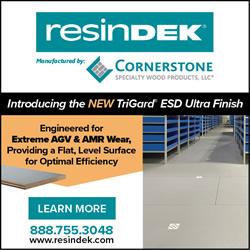
ResinDek® TRIGARD® ESD ULTRA FOR HIGH-TRAFFIC ROBOTIC APPLICATIONS
To maximize the productivity of an autonomous mobile robot (AMR) or automatic guided vehicle (AGV) deployment, it's critical to create the optimal environment that allows the vehicles to perform at their peak. For that reason, Cornerstone Specialty Wood Products, LLC® (www.resindek.com) created the TriGard® ESD Ultra finish for its ResinDek® engineered flooring panels. The TriGard ESD Ultra finish is ideal for high-traffic robotic applications characterized by highly repetitive movement patterns and defined travel paths.