OMRON to Introduce NX-series Safety Network Controller That is World's First (*1) to Support Two Industrial Safety Networks
Advanced Safety Control for Industrial Robot Systems
OMRON Corporation, based in Shimogyo-Ku, Kyoto, announced the global release of its new NX-series Safety Network Controller that is the world's first to support two safety protocols: CIP Safety (TM) (*2) that is adopted by industrial robot manufacturers and Safety over EtherCAT (R) (*3) (FSoE) that provides high-speed response.
In automotive and food factories where a wide variety of products are produced, the NX-series Safety Network Controller facilitates building and modifying safety systems for production lines using industrial robots and controls safety systems at high speeds, helping manufacturers create manufacturing sites which ensure workers' safety and productivity.
Safety systems safely stop production lines and facilities when people approach hazards such as robots in order to protect people from hazards.
Image1: NX-series Safety Network Controller (NX-SL5x00+NX-CSG320)
https://kyodonewsprwire.jp/img/201810028685-O1-g95jTguD
Automotive and food manufacturers now need to flexibly change production line layouts to produce low-volume, high-mix products and deal with short product life cycles. However, with the conventional safety controllers, they must check their safety system for the entire line even when changing a part of the line. In addition, since robots are increasingly adopted and manufacturing sites are located worldwide, demand for easy installation and maintenance of advanced safety systems is growing due to the shortage of experienced safety administrators.
To meet these needs, OMRON has developed the NX-series Safety Network Controller. This controller allows easy building of safety systems for large production lines using industrial robots and for manufacturing equipment requiring high-speed control, and provides modular safety control, eliminating the need to stop the entire production line when the layout is changed or maintained. "Automatic Programming" for safety systems and "Offline Simulation and Online Functional Test" for checking safety programs reduce the time required from design to safety verification. Moreover, "Safety Data Logging" allows even inexperienced workers to identify the cause of a sudden line stoppage, helping maximize productivity.
OMRON set forth a concept called "innovative-Automation!" consisting of three innovations or "i's" -- "integrated" (control evolution), "intelligent" (development of intelligence by ICT), and "interactive" (new harmonization between people and machines). OMRON is now committed to bringing innovation to manufacturing sites by materializing this concept. By using the NX-series Safety Network Controller, OMRON continues to pursue remarkable enhancements in productivity and safety for the global manufacturing industry and accelerates the materialization of "innovative-Automation!" together with its client companies.
Features
1. Two different networks in a single safety system to meet customers' needs
- The NX-series Safety Network Controller connected with the NX102 Machine Automation Controller enables the use of both EtherNet/IP (TM) + CIP Safety (TM) and EtherCAT (R) + FSoE at the same time.
- Safety systems for CIP Safety (TM) robots from various vendors can be easily built.
- The NX-SL5700 Safety CPU Unit provides up to 254 CIP Safety (TM) connections, enabling building safety systems for large production lines.
- The NX-series Safety Network Controller in combination with the NX102 Machine Automation Controller provides real-time safety control of up to 12 motors using EtherCAT (R) and FSoE.
Image2: System configuration
https://kyodonewsprwire.jp/img/201810028685-O2-WqrpcGPL
2. Integrated development environment Sysmac Studio for quick safety programming
- Automatic Programming cuts safety control programming time.
- Offline Simulation allows verification of programs without connecting hardware.
- Online Functional Test provides instructions on the screen from safety system checks at line set-up to report output, allowing even users without expertise to test safety systems.
3. Easy maintenance and quick troubleshooting
- Safety Data Logging helps to quickly identify the cause of a line stoppage.
- Safety Unit Restore allows easy hardware replacement without using software.
(Image3: https://kyodonewsprwire.jp/img/201810028685-O3-Wdr524U0)
An SD card containing logging settings is used for Safety Data Logging. When start trigger conditions are met, the specified device variables and exposed variables can be logged in a chronological order and put into the memory card. This function helps to quickly identify the cause of a sudden stoppage of the system and determine preventive measures.
The NX-series Safety Network Controller consists of the following units:
- NX-SL5500/5700 Safety CPU unit
- NX-CSG320 Communication Control Unit
- NX102-xxxx Machine Automation Controller
(Image4: https://kyodonewsprwire.jp/img/201810028685-O4-vu2O9hLR)
(*1) Based on OMRON investigation in July 2018.
(*2) CIP Safety (TM) adds safety functionality to industrial network EtherNet/IP (TM)that is widely used across the world.
(*3) Safety over EtherCAT (R) is a safety protocol for industrial network EtherCAT (R).
Sysmac is a trademark or registered trademark of OMRON Corporation in Japan and other countries for OMRON factory automation products.
EtherCAT (R) is a registered trademark and patented technology, licensed by Beckhoff Automation GmbH, Germany.
Safety over EtherCAT (R) is a registered trademark and patented technology, licensed by Beckhoff Automation GmbH, Germany.
EtherNet/IP (TM) and CIP Safety (TM) are trademarks of ODVA.
Other company names and product names in this document are the trademarks or registered trademarks of their respective companies.
"innovative-Automation!"
Recently, OMRON has developed a manufacturing innovation concept, called "innovative-Automation!" With this concept, OMRON is currently committed to bringing innovation to manufacturing sites through three key innovations, or three "i's." Through these innovations in the area of automation, OMRON aims to enable significant productivity improvements in manufacturing sites in order to achieve high-value-added manufacturing. With the first "i," "integrated" (control evolution), OMRON will seek to advance automated control technology so that virtually any operator, even inexperienced operators, can effortlessly perform work that previously required the expert skills of experienced workers. With the second "i," "intelligent" (development of intelligence by ICT), OMRON seeks to create constantly evolving equipment and production lines. By adopting a wide range of control devices and artificial intelligence (AI), machines can learn through experience and maintain themselves in optimal condition. For the third "i," "interactive" (new harmonization between people and machines), OMRON pursues the development of a new harmonious relationship between human operators and machines. Working together in the same workspace, machines will be able to assist human operators by recognizing human thoughts and behavior.
About OMRON Corporation
OMRON Corporation is a global leader in the field of automation based on its core technology of "Sensing & Control + Think". OMRON's business fields cover a broad spectrum, ranging from industrial automation and electronic components to automotive electronic components, social infrastructure systems, healthcare, and environmental solutions. Established in 1933, OMRON has over 36,000 employees worldwide, working to provide products and services in 117 countries. In the field of industrial automation, OMRON supports manufacturing innovation by providing advanced automation technologies and products, as well as through extensive customer support, in order to help create a better society. For more information, visit OMRON's website at: http://www.omron.com/
Featured Product
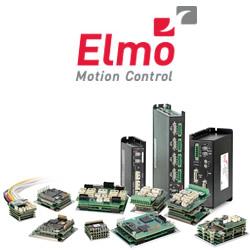
Elmo Motion Control - The Platinum Line, a new era in servo control
Significantly enhanced servo performance, higher EtherCAT networking precision, richer servo operation capabilities, more feedback options, and certified smart Functional Safety. Elmo's industry-leading Platinum line of servo drives provides faster and more enhanced servo performance with wider bandwidth, higher resolutions, and advanced control for better results. Platinum drives offer precise EtherCAT networking, faster cycling, high synchronization, negligible jitters, and near-zero latency. They are fully synchronized to the servo loops and feature-rich feedback support, up to three feedbacks simultaneously (with two absolute encoders working simultaneously). The Platinum Line includes one of the world's smallest Functional Safety, and FSoE-certified servo drives with unique SIL capabilities.